Common breakdowns, maintenance, air compressor repair
The compressor is the unit that allows you to compress gaseous substances and, under pressure, serve them to consumers. Such devices are used both for industrial and domestic purposes.
Due to its small size, affordable cost and a simple device, a piston.type compressor has become one of the most common.
Operation in accordance with the recommendations specified in the instructions will allow you not to resort to the repair of the unit for a long time, however, it will not be eliminated from this necessity forever, since the main life of any device is limited.
The principle of operation and components
The compressor is a device to increase the pressure and movement of gas to the required source (spray gun, grinding machines, nuts, airbrises and any other pneumatic equipment). The main in demand in body repair was the compressor of piston, oil type. In piston, the volume of working cameras changes with the help of pistons performing the reciprocating movement.
Have a different number of working cylinders and distinguish them by the following constructive location:
Basic design shortcomings: incomplete balance of their driving parts, the presence of a large number of friction pairs and t.D. All this is the reason for the failure and subsequent repair. Before performing the repair of the compressor with your own hands, it is necessary to study its technical structure. In the photo below the diagram of a single.stage compressor, a piston group.
- Crankshaft
- Frame
- Shatun
- Piston finger
- Piston
- Cylinder
- Valve
- Cylinder head
- Valve slab
- Flywheel
- Basils
- The crankshaft bearings
On the case near the electric engine there is an automation unit called the presettate. With it, you can adjust the compressor. It is possible to lower the pumped pressure or increase.
Modem of mobile communications on microtics
In one of the old publications there was a description of the Mikrotik RBM33G motherboard capable of working simultaneously with two cellular modems. Below I will make a brief description of how to configure Routeros for the distribution of traffic between two LTE Intections.
On the test I will use two Quectel EP06 modems.
RBM33 Microot with two modems EP06
Microatist Roter OS is a very flexible operating system and has a huge number of settings, the configuration I proposed is one of the possible, but far from the only. In general, the situation of using two gateways simultaneously for access to the Internet is not standard and has many implementations, while in any case there will be any crutches, somehow spoiling the overall picture, but so far we will not talk about bad.
To get started, we will make a standard Mikrotik RBM33G setting to enter the Internet through the modem:
- We will reset the configuration to clean (Reset configuration)
- Combine all LAN integrates into a bridge
- We will hang on him the targeted space 192.168.5.0/24
- Set up on the Bridge DHCP server
- We configure the firewall
- Pun the NAT to access the Internet from our subnet
From this moment, you should have the Internet that will work through one of the LTE intenses, the second will be idle.
Mikrotik. Simple protection against overcoming open ports
For protection, a dynamic address list will be used. When scanning ports, the source will be added to the list of blocked automatically.
For example, a certain address 8.eight.eight.8 begins to scan your external IP, scans SSH TCP Port 22. IP 8.eight.eight.8 enters the list of blocks for an hour, 8.eight.four.4 scans SIP UDP port 5060. eight.eight.four.4 falls on the list of blocked for a day. You can change the ports yourself, at your discretion.
The compressor engine does not start
As previously noted, it is the engine that fails quite often. With such a compressor malfunction, it cannot be used according to the purpose. Among the features, we note the following:
- If the installation does not start and does not appear the appropriate rumble, then the compressor disassembly is carried out only after the voltage is checking. The indicator is ideal for this. If there are phases, it is recommended to check the fuse, which also often fails.
- When the fuse is repeated, there is a possibility that a short circuit occurs in the system.
- There is a chance that the engine has serious mechanical damage. Operation under a large load, overheating or voltage changes become the reason why the device fails.
In general, we can say that there are a fairly large number of reasons why the compressor does not start.
The compressor does not turn on or off immediately after starting or during operation
First of all, they check the power cable and fuses. Also, the cause of the problem may be the wrong settings for the pressure relay. The reason that the compressor does not turn on is the operation of the thermal relay. This option is possible if the equipment has been working in intensive mode before and did not have time to cool down. The device may not turn on due to the faulty block of automation, combustion of the fuse, the operation of protection against overload. The worst option is engine combustion.
Often the compressor does not start for various reasons. This situation can be avoided as follows:
- Operation in accordance with the recommendations of the manufacturer.
- Carrying out appropriate service.
- Performing timely replacement of basic elements.
- Use only by purpose, reduction of load and ensuring the required cooling.
There are a fairly large number of different reasons why the supercharger does not turn on. Consider the most common details.
The system of the system does not start
Often the compressor does not start for various reasons. This situation can be avoided as follows:
How Air Compressors Work! (Piston Design)
- Operation in accordance with the recommendations of the manufacturer.
- Carrying out appropriate service.
- Performing timely replacement of basic elements.
- Use only by purpose, reduction of load and ensuring the required cooling.
There are a fairly large number of different reasons why the supercharger does not turn on. Consider the most common details.
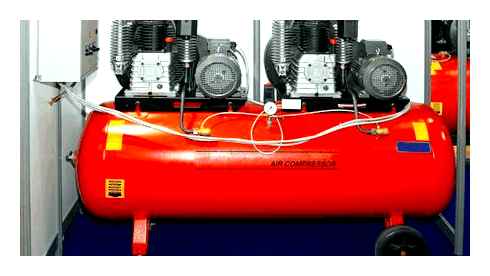
The reasons
Most of the malfunctions on which the compressor is not launched can be solved independently. The following were quite widespread:
- Proceeding the thermal protection machine. At the time of operation, the mechanism can heat up to a significant temperature. That is why the relay allows us to exclude the likelihood of such a situation.
- Incorrect operation of the pressure control relay in the system. Too much an indicator will lead to a rupture of a hose or receiver.
- Undressed voltage in the network.
- The appearance of a significant leak. Cracks or other defects in the highway become the cause of pressure loss.
Some of them can only be eliminated with the direct replacement of the main elements. The compressor does not turn on in some cases due to the break in the power supply network.
Compressors malfunctions. causes and methods of solving
With your screw compressor, something is wrong? In this article, we have collected the most popular problems with compressors and ways to solve them.
Attention! If you are not sure that you were correctly diagnosed, do not correct it yourself. It is better to entrust this to experienced specialists.
Overheating of the compressor
Often compressor owners are faced with the fact that the thermostat valve turns off the compressor due to overheating. This may have several reasons.
First, perhaps the temperature in the working room is too high. In this case, it is necessary to provide a larger air flow to the compressor and restart it by pressing the “Reset” button. Secondly, the oil cooler may be clogged. To eliminate this problem, clean the cooler using a dissolving fluid.
In addition to these most common causes, the cause of overheating can be an insufficient amount of oil in the compressor, as well as a malfunction of the thermal expanding valve. Check the condition of the heat.expanding element, replace it if necessary or share oil!
This is interesting: molybdenum lubrication. composition, characteristics, application
Causes and ways to eliminate breakdowns
The main cause of poor equipment is too low by air temperature. You just need to warm up the room in which the compressor is located.
This is due to poor closing of the suction valve. It must be removed and cleaned. It is possible that you will have to replace the elements.
Lack of compressed air in the output hole of the compressor
This speaks of closing the regulator. It is possible to eliminate the problem by checking the pressure relay, which should supply power to the electromagnetic valve associated with the regulator.
In most cases, the cause of the malfunction is extinguished by the regulator. To correct the situation, the suction filter is removed, the regulator is opened and cleaned. The best option is the dismantling of the regulator with its subsequent cleaning.
The reasons for too much oil consumption can be:- a broken filter of the oil separator, leaky seals of the oil separator filter.In both cases, problems are solved by replacing the seals or the filter itself. A leakage of oil from a suction filter indicates that the regulator is not closed or excessively high pressure is in the system.
In the first case, the functioning of the regulator and electromagnetic valve is checked. In the second case, in addition to checking the regulator and valve, the pressure gauge should be carefully examined.The cause of oil entering the control panel is a leakage of oil through the unit flange.
This problem is eliminated by replacing the compressor sealing ring.
Involuntary opening of the safety valve
The reason for the opening of the safety valve may be clogging the oil separator filter. You should check the pressure difference between the oil separator tank and a pipe with compressed air. If necessary, then the filter should be replaced.
Turning off the compressor by the thermostat
Air leaking under Pressure Switch. Air Compressor Check Valves One Way Non Return
It occurs in the case of: malfunction of the heat.expanding valve, insufficient amount of oil, malfunction of the drain system. You can solve problems as follows: replace the valve, add the oil to the desired level, check the check valve and pipelines that drain the oil.
In this case, you need to check the regulator. There may be no command to close it. Make sure that the electromagnetic valve will be disconnected.
The trigger of the chain breaker
Occurs in case of overheating of the electric motor, insufficient voltage in the network, an excessively high temperature in the room. When overheating the electric motor is checked by the relay and the heat generation from it.
With normal heat removal, the reset button is pressed, the compressor is restarted.The same actions are carried out in the presence of insufficient voltage in the network and high room temperature.
The only difference is preliminary voltage verification and providing high.quality ventilation.
To avoid the possible breakdowns of equipment, it is necessary to carry out in time. For this, Ceccato has provided special service sets.
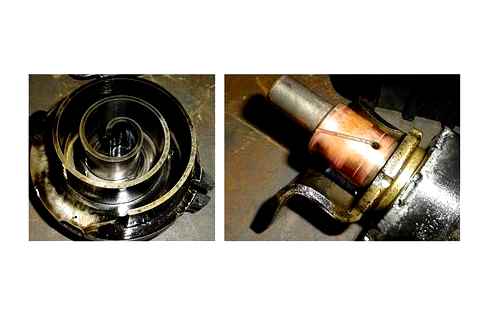
Advantages of service sets
- Reducing costs
- Attractive prices: the cost of the set is the sum of retail of elements of the kit minus 10-20%.
- Reduced administration costs.
- Reducing the time of the possible downtime of the compressor during maintenance.
- Energy saving when using original spare parts.
- Time saving
- Conducting all the necessary service procedures for 1 visit.
- Saving time for searching and ordering individual spare parts. The ease of acquisition
- All the elements in one package necessary for the compressor. The risk of incomplete maintenance is excluded
- Contains all the details to be replaced
The compressor stops and does not work
If your compressor stops, it off independently or starts with difficulty, you need to check two parameters. Perhaps the voltages in the mains are not enough. check the voltage of the electric network, from which the compressor feeds. In case of problems, eliminate them. Another option is also possible: the temperature in the room where the compressor is located is too low.
In this case, try to heat the air in the working area of the compressor. Always monitor compliance with operating standards. information about the recommended air temperature in the room is in the technical documentation of your compressor.
Repair of a piston compressor with your own hands and in the service center
Some malfunctions of the piston compressor can be eliminated with your own hands:
- when slipping the belt, pull it and clean it from pollution;
- If air enters from the receiver, you need to unscrew the valve head, clean the saddle, clean or replace the gasket;
- with insufficient oil level, add the required amount;
- Replace low.quality oil with a new one;
- When stopping the compressor, check the power circuit.
- In case of more serious failures in the operation of the piston compressor, it is recommended to repair it at the compressor repair service center or in a specialized workshop.
- If a piston compressor is not started, or there are other malfunctions, please contact Alfa-Rost Construction Service Center for the Repair of Garden and Construction Equipment.
- Self.repair and reconfiguration of complex nodes of a piston compressor can lead to more complex breakdown of equipment.
Reasons for the breakdown of screw compressors and options for their elimination
The main cause of poor equipment is too low by air temperature. You just need to warm up the room in which the compressor is located.
This is due to poor closing of the suction valve. It must be removed and cleaned. It is possible that you will have to replace the elements.
Lack of compressed air in the output hole of the compressor
This speaks of closing the regulator. It is possible to eliminate the problem by checking the pressure relay, which should supply power to the electromagnetic valve associated with the regulator.
In most cases, the cause of the malfunction is extinguished by the regulator. To correct the situation, the suction filter is removed, the regulator is opened and cleaned. The best option is the dismantling of the regulator with its subsequent cleaning.
The reasons for too much oil consumption can be:- a broken filter of the oil separator, leaky seals of the oil separator filter.In both cases, problems are solved by replacing the seals or the filter itself. A leakage of oil from a suction filter indicates that the regulator is not closed or excessively high pressure is in the system.
In the first case, the functioning of the regulator and electromagnetic valve is checked. In the second case, in addition to checking the regulator and valve, the pressure gauge should be carefully examined.The cause of oil entering the control panel is a leakage of oil through the unit flange.
This problem is eliminated by replacing the compressor sealing ring.
Involuntary opening of the safety valve
The reason for the opening of the safety valve may be clogging the oil separator filter. You should check the pressure difference between the oil separator tank and a pipe with compressed air. If necessary, then the filter should be replaced.
Turning off the compressor by the thermostat
It occurs in the case of: malfunction of the heat.expanding valve, insufficient amount of oil, malfunction of the drain system. You can solve problems as follows: replace the valve, add the oil to the desired level, check the check valve and pipelines that drain the oil.
In this case, you need to check the regulator. There may be no command to close it. Make sure that the electromagnetic valve will be disconnected.
The trigger of the chain breaker
Occurs in case of overheating of the electric motor, insufficient voltage in the network, an excessively high temperature in the room. When overheating the electric motor is checked by the relay and the heat generation from it.
With normal heat removal, the reset button is pressed, the compressor is restarted.The same actions are carried out in the presence of insufficient voltage in the network and high room temperature.
The only difference is preliminary voltage verification and providing high.quality ventilation.
To avoid the possible breakdowns of equipment, it is necessary to carry out in time. For this, Ceccato has provided special service sets.
Features of maintenance of piston compressors
After buying any compressor, there is a need to carry out proper and timely maintenance. In the opposite case, you can get a minimum of incorrect operation of the compressor, the maximum. its quick breakdown. As a rule, manufacturers of compressor equipment in operating manuals recommend conducting certain maintenance work. Consider the features of servicing piston compressors on the example of recommendations from the Belarusian manufacturer “Remeza”. The piston compressors of this manufacturer can be attributed to classic oil compressors, so the basic maintenance rules (TO) can also be extended to everything else similar equipment from other manufacturers. So, let’s consider the main preventive work and stages of the points on the items.
Conduct an external compressor inspection.
The compressor external inspection should be carried out, the compressor’s working condition visually evaluate by external signs: before starting work, check the supply cable, safety valve, manometer, pressostat on the lack of damage, which may affect the serviceability of the action. Inspect the receiver for the absence of dents, cracks, check the reliability of the ground fastening.
Set the oil level and, if necessary, adjust it.
Every day, before starting work, control the oil level. This can be done using a viewing window, which is located on a piston block. The oil level in the crankcase of the piston block should be within the red observation glass mark. If necessary, share compressor oil to the required level. When changing the color of the oil (whitewashing. the presence of water, darkening. severe overheating), it is recommended to immediately replace it. Do not allow oil leaks from the compounds and oil entering the external surfaces of the compressor.
If a low level of oil is detected, it is necessary to adjust it, then eats to add. At the same time, oils of different varieties and quality should not be mixed. As a rule, the manufacturer indicates the type (brand) of the oil to which the compressor is seasoned. Next, you need to do working operations for filling the oil:
Check the density of air pipelines
Check the density of the air pipelines for a possible air leakage. Checking the density of the air pipelines should be carried out at the unconnected installation at a pressure in the receiver no more (0.5. 0.7) MPa.Noises of air passing in the compounds should not be heard. If necessary, you need to tighten the compounds.
Drain condensate from the receiver.
After each working shift, as well as at the end of work, it is necessary to drain the resulting condensation through the condensate drain valve, which is located at the bottom of the receiver. If this is not followed by this is given to the additional moisture in the pneumolinia, and in the receiver itself, over time, there will be corrosion of metal and rust, which will worsen not only the quality of the air at the output, but can be dangerous for subsequent operation. To drain condensate, the following actions must be performed:
Clean the compressor of dust and pollution.
It is necessary to ensure that the compressor is cleaned of dust and pollution for correct and long.term operation. It is recommended to clean all the outer surfaces, the piston block and the electric motor from dust and pollution, to improve cooling. Only cotton and linen rags should be used as wiping material.
After the first 8 hours of work.
It is necessary to check the tightening efforts of the bolts of the cylinder heads of the piston block. After the first 8 and 50 hours of work, it is necessary to check and, if necessary, tighten the bolts of the heads of the piston block cylinders to compensate for the temperature shrinkage. Tightening moment according to the table below. The tightening must be done exclusively after cooling the piston unit to the ambient temperature.
After the first 50 hours of work.
Check the tightening efforts of the bolts of the cylinder heads of the piston block.
Check the tension of the belts
After the first 50 hours of operation and then, check with each 300 hours of work and, if necessary, adjust the tension of the belts, clean them from pollution. With insufficient tension, the belts slipped in, vibration occurs with exposure to the bearings of the alternating load “Tighten”, overheating of the pulleys, overheating and reducing the efficiency of the piston unit. When the belts are pulled, then there is an excessive load on bearings with their increased wear, overheating of the electric motor and a piston unit.
To check the tension of the belts, the following actions must be performed:
The tension must be adjusted by the displacement of the electric motor, having previously released the bolts of its fastening to the platform. The pulley of the electric motor and the pulley of the piston block should be in the same plane
After the first 100 hours (every 100 hours.) work.
Replace the oil.
After the first 100 hours of work, it is necessary to replace the oil. Next, every 300 hours of work, you also need to change the oil. For refueling the compressor, it is recommended to use compressor oils with a viscosity of 100 mm 2 /s at 40 ° C. As a rule, compressor oil goes with the designation of 100 VDL or 100 ISO. Do not use oil for pneumatic tools or oil for screw compressors for piston compressors.
Typical malfunctions of piston compressors
In piston compressors, like any other mechanism, malfunctions can occur during their operation associated with certain reasons. In order to understand typical malfunctions, it is necessary to classify them.
The first type includes:
The nature of the malfunction: superficial and internal pollution of the filter element
Reason: violation of the requirements for the room, the place of installation of the compressor. The presence of dust, paints, etc.D.
Consequences: decrease in compressor performance, overheating, premature wear, cylinder. Piston group.
The nature of the malfunction: the absence of a filter assembly, the absence of a filter element, violation of the integrity of the filter or filtering element (breakup, crack, breakdown)
Reason: careless operation, storage, transportation.
Consequences: dusting of dust, aerosols of paint into a valve node and into compressor cylinders. Wear and contamination of valves, channels of the valve group, wear of the cylinders, pistons, lawsuits and subsequent loss of rings mobility (resting), oil pollution (oxidation and aging of oil). Pollution of compressed air.
The nature of the malfunction: overheating, decreased compression, catastrophic wear of the cylinder-piston group.
Consequences: mechanical breakdown of the cylinder-piston group. Blinds on the surfaces of the cylinders, wear of the sliding bearings (liners) overheating, breakdown of rings, jamming of pistons, connecting rods, tunes break. Increased loads on the electric motor bearings.
Here you should pay attention to the features of lubrication of piston compressors:
a) the oil must be compressor. in this oil an order of magnitude (10 times) is less ash content compared to motor oils;
b) pour the oil recommended by the manufacturer;
c) monitor the recommended level of oil;
d) change the oil, exactly as it is written in the technical guidance of the compressor.
The second type of fault is careless operation (non.compliance with the compressor operating mode):
Compressor operating mode. repeatedly short-sum, with the duration of inclusion (PV) up to 60%, with the duration of one cycle from 6 to 10 minutes. The continuous operation of the compressor is allowed for no more than 15 minutes, but not more than once for 2 hours. From this it follows that the total time of the compressor production should not exceed 36 minutes. This applies to industrial piston compressors with air cooling. For household compressors PV less than 60%. And the useful time of work does not exceed 30 minutes. in hour.
Characteristic malfunctions: external pollution of all compressor nodes, common thing. where we paint there and store the compressor. Damage of the pipeline reinforcement, plastic protective buildings of the compressor, press facilities (pressure relay) of protective casings of the fan and the fan impeller itself, forget to drain condensate from the receiver, mechanical breakdown of pressure regulators, manometers, independent repair and reconfigure of complex compressor nodes, etc.D.
Electric malfunctions are divided into two main types: mechanical and actually electrical.
Mechanical accidents are a deformation or breakdown of the rotor shaft, weakening of the stator core to the bed, weakening of the rotor core, melting the babbit in sliding bearings, the destruction of the separator, ring or ball in rolling bearings, winging, dust and mud in moving elements, pr.
The cause of most mechanical accidents are radial vibrations due to the asymmetry of the supply network (t. n. Phase bias), mechanical overloads on the shaft of the electric motor, marriage of components or allowed during assembly. Up to 10% of all accidents have a mechanical origin. At the same time, 8% falls on the share of accidents associated with the asymmetry of the phases and only 2% in the accident associated with mechanical overload. The share of accidents related to marriage is small, and therefore it can not be taken into account in this consideration.
Electric accidents, in turn, are divided into three types:
The following are the main malfunctions that may arise, signs of their manifestation, causes and methods of elimination.
Strong engine vibration
Piston engines are characterized by strong vibration. It is not worthwhile to be concerned until the vibration becomes too noticeable. It can be assumed that the reason is in the wear of vibrations, which are easily replaced.
compressor
The cause of vibration may be weakened by bolts fastening. In this case, the repair of the air compressor consists in simple tightening the bolts.
Timely maintenance guarantees the performance of the unit
In order for the device to work properly for a long time, the recommended maintenance at the initial stages of operation should begin. Specialists are recommended the following actions from the moment of acquisition:
- When opening transport packaging, the presence of a passport for the installation, technical documentation and compliance with the factory inventory of components of components is monitored.
- Before the first launch of the engine, the level of oil is checked on the measuring probe and, if necessary, is added to the recommended mark. The oil should be poured recommended by the manufacturer and specified in the technical documentation. For better spreading lubrication and checking good operation, let’s give a compressor to work at idle for 10 minutes.
- In the absence of Комментарии и мнения владельцев, a pneumatic tool joins the compressor installation and work begins. Note: It is undesirable to supplied nutrition for the supercharger if there is excessive pressure in the receiver.
- Try to keep records of the compressor time and, after 500 hours of work, change the oil to a new. To do this, the flange cover of the crankcase is removed, the development is drained and accumulated contaminants are cleaned. Only after that fresh lubricant is poured.
- Followly clean the input air filter.
- After 16 hours of operation using the final crane, moisture is drained from the receiver. Manufacturers also recommend cleaning the inner surface of the cylinder every six months using special means.
- At the end of the work, the compressor installation is disconnected from the supply network, and air is pulled from the high pressure system.
- If the supercharger has not been operated for a long time, before starting, it is necessary to clean and grease the contact platforms of the air valve.
- Non.playing metal parts must be grounded. As a rule, manufacturers bring a grounding conductor to a plug euro.filler. And it is only required to ground the corresponding contact in the outlet into which the compressor installation is connected.
Timely compliance with these simple requirements will contain the mechanism in good condition. Such a time.consuming procedure as with your own hands will be required extremely rarely. Competent ground will avoid problems with the electrical part of the device. Regular replacement of oil and cleaning filters will warn the premature wear of the rubbing parts.
Number of blocks: 29 | General number of symbols: 24330 Kolya of the used donors: 5information for each donor: