Figure cutting of sheet metal with your own hands
DIY sheet metal cutting. How to cut off a sheet of metal with improvised materials. Cut the circle and other figures.
Sheet metal is a common building material that is used for the manufacture of fences, drainage and visors. Often on sale you can find ready.made products made of galvanized steel, such as skates or pipes for removing rainwater from the roof. But what if the product is non.standard and you need to cut sheet metal with your own hands?
Initially, when choosing tools, you need to decide on the tasks. Not only the amount of work is important, but also the time frame, the accuracy of the cut and the possibility of damage to the protective coating. At a construction site, they often use electrician. At the same time, you should not expect a very flat edge. The advantage of such a device is the speed of work.
How to cut off a sheet of metal evenly? At home, the problem is solved quite simply. using metal scissors. But this method requires a lot of time and physical strength. Scissors are not suitable if you need to cut long stripes. The most even cut can be obtained using slotted scissors. Such a tool is quite expensive and it is usually used by professionals.
Equipment for cutting a profiled and galvanized sheet:
One of the fastest ways to cut a galvanized sheet is the cutting of a corner grinder. Among the shortcomings of such processing are torn edges that will have to be additionally cleaned and aligned with.
The corner grinder is not suitable for cutting corrugated board, as sparks during cutting can damage the polymer coating.
But for simple work that does not require high accuracy and accuracy, the corner grinder is quite suitable.
Please note that when using such a power tool, purchase a special disk that will not damage the protective coating on the galvanizing sheet.
After cutting the corrugated board, the edges must be cleaned and covered with special paint. Such equipment can be used if you are building a barn from a profiled sheet or making a visor.
In this case, you do not have to purchase a special and expensive tool.
Rules when working with a corner grinder:
- Choose wheels with carbide teeth;
- Work at low speeds;
- Treat the cuts of the cut with a special anti.corrosion coating.
Many craftsmen have a knife.haired woman for metal. This is a universal and cheapest tool. It should not be used if necessary to cut the curly edges, but for the manufacture of even plates, the hacksaw is suitable. The biggest drawback of such a tool is the time to carry out work. It needs it a lot.
Electric
If you need to cut a circle in a sheet of metal, it is worth using an electrician. It works quite quickly, so you will receive a neat hole in a matter of minutes. Among the shortcomings of the equipment are the noise and the possibility of the accommodated edge when processing profiled sheets.
Subtleties of work by an electrician:
- It is necessary to use saws with small teeth;
- It is necessary to choose a reciprocating mode;
- It is necessary to control the slope of the cutting part;
- Fast failure of consumables.
A circular saw
Sometimes a circular saw is used for metal cutting. If you work with corrugated board, then the equipment must be included at low speeds. Otherwise, you can damage the polymer coating.
For work you will need a partner who will hold the sheet. Among the advantages of this tool, one can highlight that the work is performed without heating, respectively, the protective coating on the profiled sheet you will not damage.
It is best to use an aluminum circle.
To establish fast work with a circular saw, you need to prepare a pattern of plywood. The groove is not cut out in this sheet. This will be a kind of workpiece that allows you to save a galvanized or polymer coating on the sheet. An excellent tool for cutting metal is a two.disc saw. She, unlike corner grinders, leaves no torn edge and works much quieter. Unfortunately, not every master has a similar tool.
It all depends on the size of the hole. If the diameter is small, the drill is suitable. If you need large holes, special crowns are used for the drill. Pay attention to the material from which Konka is made. For processing a profiled sheet, it is worth using nozzles with carbide coating. Processing should be carried out without an increase in temperature.
For the manufacture of a large diameter hole, an electrolobian is used. With this tool, it will not be difficult to cut a circle of large diameter. During operation, use a saw with small teeth
How to cut leaf metal
DIY sheet metal cutting. How to cut off a sheet of metal with improvised materials. Cut the circle and other figures.
Sheet metal is a common building material that is used for the manufacture of fences, drainage and visors. Often on sale you can find ready.made products made of galvanized steel, such as skates or pipes for removing rainwater from the roof. But what if the product is non.standard and you need to cut sheet metal with your own hands?
How to cut thick sheet metal evenly
For cutting thick sheet metal, it is advisable to use an angular grinder with a capacity of more than 1 kW. In this case, cut the product with an angular grinder, you need to go forward from its edge. First, on the sheet, it is necessary to draw a fishing line for a trimmer along which a cut will be carried out. Then, along the drawn line, you need to put a steel corner or even wooden beam. With the help of a clamp, a corner (beam), takes a snug tightly to the surface of the sheet.
Then, along the corner, strictly along the drawn line, it is necessary to walk around the corner grinder and make a small groove, the depth of which is about 1-2 mm. After this procedure, the corner can be dismantled and the usual cutting of the metal.
The groove made on its surface, on the marked line, will not allow the saw disk to move away from a pre.given path, which makes perfectly smooth edges at the cutting places.
Important! When working with a corner grinder, it is necessary to comply with the safety rules and use personal protective equipment.
Also, during the work, it is necessary to take into account the direction of rotation of the circle of corner grinder, as well as its size. You can’t put large discs (from 150 mm or more) on small corner grinder (125 mm), having previously dismantled the protective casing for this.
Cutting the metal with scissors
Details Category: Light.leaf metal
Cutting thin.leaf metal with scissors
Thin.leaved metal can be cut with special scissors.
Hand scissors consist of two halves. Each half is made as a whole and combines a knife and a pen in itself. The halves are interconnected by a screw. By the location of the cutting knives, manual scissors are divided into left (rice. left a) and right (rice. Left b). If you look at the scissors from the knife side, the upper knife is located on the left scissors on the left, at the right. on the right.
Direct ones are distinguished by the form of cutting knives (rice. right a-g) and crooked scissors (d).
To reduce the efforts necessary to cut durable material, lever scissors are used (see.rice. left).
The cutting edges of the knives in the scissors should be well sharpened, and the cutting planes fit tightly to each other and are well fixed by the screw.The quality of the sharpening of the scissors can be checked by how well or bad they cut the paper.
Thin.leaved metal can be cut in two ways. The first way. scissors are taken with your right hand. The thumb is placed on the upper handle, and the lower handle is covered with index, middle and ring fingers. The little finger is placed between the handles: when cutting, they spread the handles of scissors (see.rice. on right). If the handles of the scissors are spread tight, then instead of the little finger you can use the index finger. In this case, it is placed between the handles of the scissors.
The second method of cutting thin.leafy metal is that one handle of scissors (the one that below) is clamped in a vice and the other is covered by the fingers of the right hand (see.rice. left).
The material in both cases is served with the left hand. This method can significantly enhance the pressure between the knives and cut more solid material.
The workpiece is slightly raised and fed, and the blade is directed exactly at risk.
After cutting, the workpiece is straightened, the burrs are removed from the edges, sharp corners are dull, checked with a ruler and a square cutting quality.
When cutting along the curve line (see.rice. on the right) there are difficulties in promoting scissors, since in the place of rounding the cut part of the metal bends worse and interferes with the work of scissors.
In order to avoid this when cutting, for example, a circle from a square sheet of tin, first the corners are cut off on straight lines, and then cut a circle, cutting off a narrow strip of tin (see.rice. left).
When working, the scissors should not be disclosed completely, but only so much so that they capture the sheet. If you open the scissors too wide, then they will not cut, but push the sheet.
When cutting thin.leaved metal with scissors, the cut part is greatly bended and the edges of the sheet at the site of the cut are made very acute. Therefore, on the left hand supporting the sheet, be sure to put on the mitten.The left hand should not be on the cutting line.
Cutting the sheet along the line of a long length, you can not completely squeeze the knives, as this can lead to cracks and even tears of the edges of the material on the cut line.The fixing of the scissors in the vice should be strong and reliable, since when they break off, you can injure your hands on the vice of the vig.
You can not touch the bare hands of the cut edges of the workpiece.
Serve scissors with handles from you, but put on the contrary.
At the enterprises of thin-leaf metal, they cut on special cerebral machines. Distinguish between mechanical scissors. guillotine and disk.
Guillotine scissors are of two types: parallel and inclined. The first knives are located parallel to each other, the second. at a slight angle.
In discs, the sheet metal is cut by the sharp edges of the rotating discs (see.rice. left).
Curtain scissors are used for curly cutting, the upper knife of which is rotated around the axis, and the lower one is motionless (see.rice. on right).
Cutting blanks at the enterprise are performed by metal cutters. They should know the properties of various metals and the device of industrial scissors well, be able to mark the blanks.
Recently, the cutting of metal with a laser beam, a stream of water under high pressure have been spreading in production. These methods are highly performance and accuracy.
§ 31. Cutting with hand scissors [1980 Makienko n.And General course of locksmithing]
Hand scissors are used to cut steel sheets with a thickness of 0.5. 1.0 mm and from non.ferrous metals up to 1.5 mm. Hand scissors are made with straight (rice. 110, a, 6) and curves (rice. 110, c) cutting blades.
By the location of the cutting edge of the blade, manual scissors are divided into right and left.
The right are scissors, in which the bevel on the cutting of each half is on the right side. Right scissors are cut along the left edge of the product in the direction of the clockwise (rice. 110, 6).
Lefts are called scissors, in which on the cutting part of each half the bevel is located on the left side. Such scissors are cut on the right edge of the product counterclockwise (rice. 110, c).
When cutting the sheet with right scissors, risk on the cut metal is all the time. When working with the left scissors, to see the risk, you have to bend the cut metal with your left hand, shifting it through the right hand, which is very inconvenient. Therefore, sheet metal in a straight line and along a curve (circle, rounding) without sharp turns is cut with right scissors.
The length of the scissors i1 200, 250, 320, 360 and 400 mm, and the cutting part I2 (from sharp ends to the hinge), respectively, 55. 65; 70. 82; 90-105; 100. 120 and 110. 130 mm. Well.sharpened and adjusted scissors should cut paper.
The scissors are held in the right hand, covering the handles with four fingers and pressing them to the palm of your hand; The little finger is placed between the handles of the scissors (rice. 111, a).
The compressed index, ring and middle fingers are unclenched, straightened with a mysine and with its effort the lower handle of the scissors is removed to the desired angle. Holding the sheet with the left hand (rice.
111, b), serve it between the cutting edges, directing the upper blade exactly in the middle of the marking line, which should be visible when cutting. Then, squeezing the handle with all the fingers of the right hand, except the little finger, cut.
In Fig. 111, in, g shows the techniques of the work with scissors.
For rectilinear cutting of a metal of small thickness, hand scissors are used, one handle of which is clamped in a vice (rice. 112, b):
Stool scissors (rice. 112, a) differ from manual large sizes and are used when cutting sheet metal up to 2 mm thick. The lower handle is tightly clamped in a locksmith or attached (driven) on the table or on another hard base. For cutting sheet steel up to 2 mm thick, stagnant fixers are used (rice. 112, a), which is not always convenient.
The stool scissors are inexpensive, they require significant efforts during operation, therefore, they are not used to cut a large batch of sheet metal.
Small.sized power scissors. Innovator a. N. Vasilyev created small.sized power scissors for cutting sheet steel up to 2.5 mm thick, rods, bolts (studs) with a diameter of up to 8 mm. The dimensions of these scissors do not exceed the dimensions of standard hand scissors
For cutting, the handle 7 is fixed in a vice, and for handle 8 (working) is driven. The working handle is a system of two sequentially connected levers. The first lever 6, on one shoulder of which a knife 4 is fixed, is connected using a screw 3 to the handle 7.
The second shoulder of the lever 6, which is in ordinary scissors with a handle, is made shortened and ends with a hinge 7, or the proper handle actually.
The end hinge of the handle 8 using two hinged links 2 is connected to the handle 7. This system of levers increases the cutting force by about twice compared to ordinary scissors of the same dimensions.
Scissors knives are interchangeable and attached to levers on secret rivets.
These scissors also have a device for cutting rods with a diameter of up to 8 mm.
The device has 5 wheels with holes fixed on the levers of scissors, and is ordinary scissors, but with special shape knives (hardened bushings). These knives are interchangeable and inserted into the disc nest.
For pruning the bolts (studs) in the bushings of one of the disks there is a cut (several threads), which protects the threads of the bolts when pruning from crushing.
Small.sized power scissors provide good cut quality.
Hand lever scissors are used to cut sheet steel up to 4 mm thick, aluminum and brass. up to 6 mm. The upper hinged knife 3 is driven from the lever 2. Lower knife 7. motionless.
Knives are made of steel U8 and hardened to hardness HRC 52. 60. Cutting angles of cutting faces 75. 85 °.
Check, lubricated before work. whether the rubbing parts, whether the lever goes smoothly, is there no gap between the cutting edges.
When cutting the metal with the right hand, the handle of 2 levers is wrapped and smoothly move to the upper position, while the upper knife 3 goes upward. Then the sheet 4 is laid so that the left hand holds it in a horizontal position, and the fishing line for the trimmer cut was in sight and coincided with the upper knife blade 3.
The hand is lowered by the lever with a knife down until part of the metal is cut, after which the lever is moved to the upper position. Then slightly raised the sheet with the 4th left hand, promote it at risk along the cutting edge of the upper knife and repeat the method of cutting until completely cut.
Scissors provide a cut without dents, cuts along the edge and sufficient accuracy.
Lever (fly) scissors are widely used to cut sheet metal 1.5 thick.2.5 mm with a strength limit of 45. 50 kgf/mm2 (steel, duralumin, etc. D.). These scissors cut metal of significant length.
Lever scissors have cast.iron bed 7 and table 2. The lower fixed knife 8 is built into the table 2, and the upper movable knife 5 with a curved cutting edge is fixed in the knife.item 6.
The upper mobile knife 5 has a counterweight 7, a balancing knife with a knife.
Sketches for plasma cutting
Both in the city and in rural areas, traditions are returned to decorate their own space with original things made to order or with their own hands. To express your aesthetic needs for decorating a house, a garden plot has become easier with the appearance of plasma cutting of metal.
Unlike hot forging, which has been used for many centuries to create fences, visors above the porch, weathercocks, fireplaces and furnace doors, the plasma cutting process requires less physical costs. Artistic cutting of metal plasma faster manufacturing process, forging, and the pattern is more deliberate and thinner.
Heating of the metal to very high temperatures does not affect its technical characteristics due to the short.term contact of the processed material with the flame. In view of this, influxes are not formed on the sections, which means that the finished product is not required.
The most painstaking work in the art cutting of metal plasma is to create sketches for cutting. Not being an artist, you will have to use the method of increasing the picture you like to the required size, designing it on a sheet of metal by means of a light bulb placed in a box located behind the image on paper. Such a home.made increase is used if the house projector has not been preserved in the house since ancient times. The image size varies by moving the picture, to a bunch of light or removing it to the required distance.
Artistic cutting for metal can be different in technique of cutting. To create garden sculpture, a clear output of the subject is necessary. It is better if the cutting is long clock lines. This method of conducting a cutting arc along the contour of the element is also necessary for cutting large elements in the fence, on the gate and other decor details. Small slots are created by short “strokes” flame on a metal sheet.
Fences
For parks and city recreation zones, we make spectacular fences, stylish street furniture, beautiful metal fences and much more that allows you to decorate the city and make its appearance modern and pleasant.
A circular saw
Sometimes a circular saw is used for metal cutting. If you work with corrugated board, then the equipment must be included at low speeds. Otherwise, you can damage the polymer coating. For work you will need a partner who will hold the sheet. Among the advantages of this tool, one can highlight that the work is performed without heating, respectively, the protective coating on the profiled sheet you will not damage. It is best to use an aluminum circle.
To establish fast work with a circular saw, you need to prepare a pattern of plywood. The groove is not cut out in this sheet. This will be a kind of workpiece that allows you to save a galvanized or polymer coating on the sheet. An excellent tool for cutting metal is a two.disc saw. She, unlike corner grinders, leaves no torn edge and works much quieter. Unfortunately, not every master has a similar tool.
Than and how to make a hole in a sheet of metal?
It all depends on the size of the hole. If the diameter is small, the drill is suitable. If you need large holes, special crowns are used for the drill. Pay attention to the material from which Konka is made. For processing a profiled sheet, it is worth using nozzles with carbide coating. Processing should be carried out without an increase in temperature.
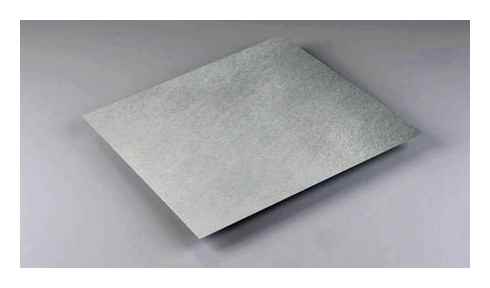
For the manufacture of a large diameter hole, an electrolobian is used. With this tool, it will not be difficult to cut a circle of large diameter. During operation, use a saw with small teeth
How to cut a thin sheet of metal with scissors: step.by.step instructions
Step 1. Buying the required tool
Buy a couple of scissors for cutting metal suitable for the type of cutting, which entails your project. straight or curved.
Many manufacturers of metal scissors use colored marking of handles to indicate three main varieties of scissors: red handles indicate that scissors are cut to the left, scissors with a green handle are cut to the right, and scissors with a yellow handle are cut directly.
Step 2. Preparation of the workplace
Install a durable, stable workbench that can withstand the size of the sheet metal that you are going to cut. As a rule, a sheet of plywood or a similar material of a suitable size, supported by two goats, becomes an ideal workbench for leaf metal projects.
Step 3. Marking Part
Place the metal sheet on the workbench and put the pattern with a tape measure, pencil and ruler.
If your project requires curved cuts, make a simple, economical and template, creating the desired curve first, using a piece of paper or a suitable material.
Make a pattern in the necessary form and place the entire composition on a sheet of metal to circle it, and then remove it.
Step 4. metal cutting
Put on the protective glasses and work gloves and take the scissors for tin. At the beginning of each cut, it is important to fully open the tool and to plant the edge of the sheet metal in the lips as deeply as possible.
Combine a tool blade with a drawing line (a fishing line drawn by a pencil for a trimmer by which you are going to cut), maintaining contact between leafy metal and the upper blade of the scissors for tin.
Squeeze the handles in one hand to make a cut, and repeat this process until the cut is completed.
If your project requires cutting holes in the center of sheet metal, draw it on metal, like any other fishing line for a cutting trimmer.
Then make a pilot hole in a pencil painted with a drill equipped with a metal cutter with a diameter of a few centimeters or more to stick the sponges of the scissors for the metal.
Pass the ends of the sponges for the scissors through the pilot hole and cut the desired radius using the corresponding curved scissors for cutting the metal to the left or right.
Step 5. Processing the finished part
Finally, process the edges of the metal with a metal file to remove the remaining burrs from the cutting edge.
Expert view: how to cut corrugated board?
Even if you ordered a corrugated board of the required length, during the installation process, you may need to cut the sheet. Sometimes a profile must be shortened or “adjusted”: for example, in the places of adjustment of the roofing material to the chimney. If you mount a roof or a sophisticated fit, you may need to cut the corner of the profiled sheet.
The question arises: how to choose a suitable cutting tool? We formulate the general requirements for it. A curriculum cutting tool should:
- cut a profile without overheating of metal, do not burn polymer and zinc coatings. The profile is a “pie” of several layers: a steel base covered on both sides by zinc, soil and a polymer layer (on the front side) or a protective coating (from the inside). Each layer performs a certain function: it protects the steel basis from corrosion, provides a professionalist with aesthetic appearance and others. If one or more layers are burned out, this will affect not only the aesthetic characteristics of the corrugated board, but also the functional. the steel base will be subject to corrosion;
- Do not form sparks during cutting. Sparks from the abrasive disk can damage polymer and zinc coatings. We indicated the consequences of such damage in the previous paragraph;
- leave a clean fishing line for the trimmer of the cut, do not deform the edges of the profiled sheet. Otherwise, the resulting “burrs” will need to be bend, and the crushed edges. straighten. This will require significant time spent;
- Do not melt the edges of the profiled sheet. Otherwise, this will lead to damage to the protective and polymer layers along the edges of the sheet and, as a result, to the occurrence of bromatic corrosion.
Consider which electrical and manual tools are optimal for trimming a profiled sheet, and which is prohibited to use.
Attention: Do not forget to process the seats of the sections with repair enamel.
Is it possible to cut corrugated board with “corner grinding”?
The profileist is strictly forbidden to cut this tool for three reasons:
- Spectacular sparks that fly out from under the disk during work harm the decorative-protective layer. They fall on a polymer coating, burn it and zinc. In places where sparks got, corrosion may appear.
- The abrasive disk saws a professionalist due to friction. As a result, the metal heats up, under the influence of high temperatures, the polymer and zinc coating along the edges are burned out, which leads to the occurrence of bromatic corrosion.
- The abrasive disk leaves the “torn” edges.
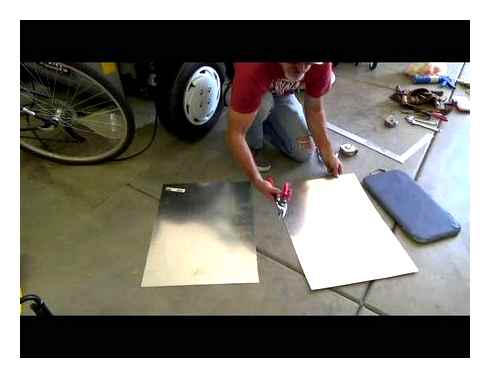
So: “Corner grinding” can be quickly cut, but it will become unsuitable for use. Therefore, the answer to the question “How to cut corrugated board“ corner grinding ”” is simple: no way.
Whether the cutting of corrugated wood is permissible with a disk saw?
Cutting corrugated board using a disk saw, even if you use a diamond disk with small teeth, is not the best option. This tool cuts metal due to heating; The disk melts the edges, and with them. zinc and polymer coating. Thus, the edges of the sheet are again unprotected from corrosion.
There are no sparks in the process of cutting, which burn polymer and zinc coatings. But due to aggressive effects on the edges of the sheet, we do not recommend using this tool.
Is it possible to use an electric jigsaw for cutting a profiled sheet?
Yes, this is one of the most popular options, especially an electrician with a laser pointer. this tool can quickly cut a sheet without getting down from markings.
In what cases do they use?
When you need to get a curly or straight section on one or more sheets of corrugated board up to 21 mm high. To cut a pack of sheets, this tool is not used. the jigsaw may fail.
An electric jigsaw is often used for cutting a profiled sheet because:
- Almost everyone has it, it does not need to be additionally purchased.
- It is easy for them to work, this does not require special skills.
- With the help of an electrician, you can cut corrugated board at any angle.
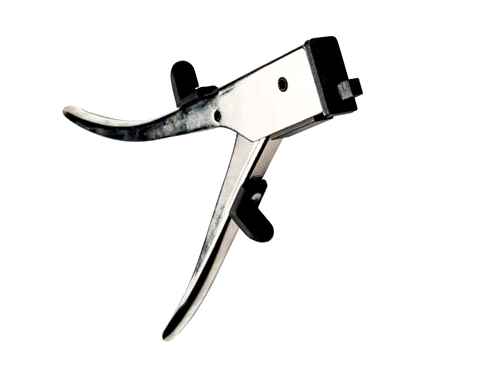
This tool is suitable only for a profiled sheet up to 21 mm high (not higher than the S-21). If you have chosen material with higher corrugations, it is better not to use an electrician: it will tear the metal. Also, he does not have enough blade length for cutting corrugated board with high waves. On the functionality of the tool, working with such a material will also not affect the best way. it may break.
When working with an electrician, there is a possibility of overheating of the metal. To avoid this, follow our tips:
- Control the power of the jigsaw. It is not necessary to turn on the tool at full power, otherwise you run the risk of overheating of the metal and burn the polymer and zinc coating.
- Periodically drip on the blade oil (any). This will help reduce friction, which means that the metal will heat less.
Attention: In the process of cutting a profiled sheet, a small metal shavings forms. It must be quickly removed with soft fabric (do not use an abrasive brush for this! You can damage the polymer coating). Otherwise, the remaining metal pieces on the surface can begin to rust and spread corrosion around.
Is it permissible to use the “cricket” nozzle on the drill?
This is also a rather popular tool. Almost everyone has a drill, for her you just need to buy an inexpensive nozzle with which the drill will work like electric wizards. Also do not forget to purchase a set of replaceable blades.
Drill with a “cricket” nozzle carefully cuts metal without deformation of the edges of a profiled sheet. The edges do not bend, they do not need to be straightened subsequently; The edges are even, without “burrs”.
In what cases do they use?
For longitudinal or transverse cutting of profiled sheets, for figurative cutting, for cutting inaccessible areas. The thickness of the metal should not exceed 0.8 mm.
Attention: During cutting, the drill nozzle should be located strictly perpendicular to the surface of the profiled sheet. In this position, the tool will work correctly.
Whether the cutting scissors are used to cut the profiled sheet?
Yes, they use it. They have three main advantages:
- Cut the metal faster than an electrician, and in speed they are comparable to an angular grinder.
- With their help, you can start cutting the sheet not from the edge, but from the middle (the tool cuts out the hole in the right place in the sheet).
- Do not deform the edges of the profiled sheet. Fishing line for the trimmer of the cut is flat.
- They cut the profile with any height of the waves and any thickness of steel.
Design
Roller scissors for metal, gathered houses with their own hands, have a common essence that remains unchanged. this is the presence of a cutting knife. It is made of steel alloys with a maximum strength threshold and other characteristics that should be higher compared to similar steel parameters that will be processed on the cutting machine.
In practice, it is known that the roller knives manufactured at the factory for cutting metal have a resource of about 30 km of steel sheets, with a reservation for the maximum thickness of the sheet, which will not exceed 0.5 mm.
Accordingly, if the thickness of the material is higher, then the durability of the tool is reduced. However, nothing prevents the tool and thereby extend the resource of its operation.
Necessary materials
A machine for cutting sheet metal, designed with their own hands, needs knives, the range of material of which is very wide, and the choice of one of them mainly depends on the type and thickness of the material that will need to be cut. If you have to work with not the most durable, thin leaf steel, such as aluminum, then the simplest bearings will be the perfect option. But for the desired functionality of the roller knife, they do not have enough sharpening, which should be carried out independently throughout the end of the future tool.
The main roller knife is installed on the mobile part of the structure with a clamping handle, when pressed on which the workpieces are closed between the two cutting surfaces. The diameter of the bearings directly affects the speed of the operation. That is, the greater the diameter of the bearing, the higher the production speed on the machine.
Making a roller knife for metal with your own hands
To simplify the work with the tool and the tradition of convenience, it would be nice to equip the leaf cutter with the guide plane.
The manufacture and installation of this part is not difficult, and in return it will greatly simplify the whole process. The output is a universal machine with roller knives, which can interact with other metalworking equipment, which is also without problems constructed in the house.
Another similar option
Can be done differently. At first, the same work is performed as in the previous version. the strip is drawn, the corner is laid and pressed. But here the groove is made a little deeper-4-5 mm. After the corner is removed, the remainder of the metal can simply be chosen, and the edge should be treated using an angular grinder with a grinding disk. However, small fits on the edge are possible here, which makes the second option more acceptable.
The groove along the guide corner is made a little deeper than in the previous version
Summing up
The fact that the corner grinder is very convenient for cutting metal is not disputed. However, it is necessary to be able to work and strictly observe all precautions and safety regulations. You need to understand that they were created precisely in order to preserve the life and health of a master working with such a dangerous tool as an angular grinding machine.
We hope that everything that we told today will be useful for those who have no experience with a corner grinder. If something remains incomprehensible, it is worthwhile to set it out in the Комментарии и мнения владельцев below the article. The editors of Housechief will be happy to answer all questions as quickly and fully as possible. You have experience of such work or you know other methods of cutting? Then we ask you to write about this in the discussions. Such information will be very useful to many. And finally, according to the already established good tradition, we suggest you watch a short but rather exciting video on today’s topic.