DIY discs for a disc saw. Drawings, photos, tips
When assembling a table for cutting with your own hands, you should follow the optimal balance between functionality, safety, time and means. This can be achieved by choosing details and materials with the desired parameters. It turns out to reduce costs by involving old details of other designs. furniture, frames of wooden houses and outbuildings.
Countertop
The main requirements for the saw table are resistance to strong load, shock and vibration. The countertop should be smooth enough for movement, not bend under weight from 50 kg. Suitable options can be:
- Metal (steel or duralumin) 3-5 mm thick. The advantages of metal countertops are high strength, almost unlimited service life, shortcomings. large weight, decent cost.
- Laminated wood-bearing plate or moisture resistant plywood with a thickness of at least 2 cm. The cost of this option will be the most profitable, but the strength is noticeably reduced.
- Textolite 15–20 mm thick. The material is more durable than the plywood, but inferior to the metal. At the cost of textolite countertops are also between metal and plywood sheets.
They are not recommended as a material for a countertop plastic, wood chipboard or OSP. The design made of this raw materials will be unstable to the vibration from the saw. You can make a table completely from natural wood. but too expensive.
Metal laminated wood-bruise
Stanin
At the base of the table for sawing boards can be wooden bars fixed under the lid to increase hardness. Elements with a cross section of at least 5 x 5 cm are placed, retreating 50–90 mm from the edge of the countertop. For the sawing table, it is recommended to choose bars of hard wood. beech, horned, oak. The advantages of a tree are low cost, simple installation with self.tapping screws. Disadvantages. lower strength and service life, high probability of fire.
The upper part of the table frame for the sawing is often made with other materials from the same sheets that were chosen for the countertop. For the legs of a wooden structure, it is recommended to use the beam, fixing it with the help of metal corners. The pros and cons of wood supports are similar to the features made of the same material of the bed.
The basis of the table for cutting and cutting the boards can be metal. Stability increases when choosing metal corners or channels with sides of 25-50 mm. To save them, they are bought at the intake of scrap metal or replaced with specialized pipes. The details of the frame are connected by welding. The use of bolt compounds is not recommended due to the possibility of promoting under the influence of vibration. The reasons for choosing a metal bed are maximum strength, reliability, simple care. Cons. high cost, the need to use a welding machine.
Metal wooden beams plywood laminated woody plate
Features of the circular saw
Knowledge of these features is extremely important, you should take into account the regimes of the functioning of the saw, know the type of load and take all possible measures to strengthen the most important nodes. Only with this approach can you achieve a long and safe operation of a home.made machine.
What are the general features of woodworking mechanisms?
High speed of the teeth of the saw. This is how the quality of sawing is ensured. But large speeds of the saw disc are caused by serious injuries, during the manufacture of the machine, very much attention should be paid to safety precautions. All devices available on industrial specimens should not be installed must be installed that some of them are unnecessary, and you can upgrade the factory samples for the better. All safety regulations are written by the blood of injured people, do not repeat tragic errors.
This refers not to withstand significant static loads, although this is very important. The table can easily perceive great efforts of this type, but at the same time vibrate from exposure to even relatively small dynamic multidirectional loads. This condition does not have a negative impact on safety precautions, but noticeably worsens the quality of the saw
Traces of teeth are noticeable on the surface of lumber, it is difficult to withstand the specified linear dimensions, etc. D.
Fire safety. Absolutely all electrical appliances, engines, starters and other special reinforcement must be mounted in strict accordance with the requirements of the PUE. You need to know that dry sawdust not only burn perfectly, but with a certain concentration in the air form an explosive mixture. By the way, burning sawdust is difficult to extinguish, they swim on water and continue to burn.
No need to make the easiest machine due to safety devices, strictly follow the recommendations of designers. Decide what you need, woodworking machine or fresh problems?
Advantages and minuses
The presence of a device helps to solve a few issues:
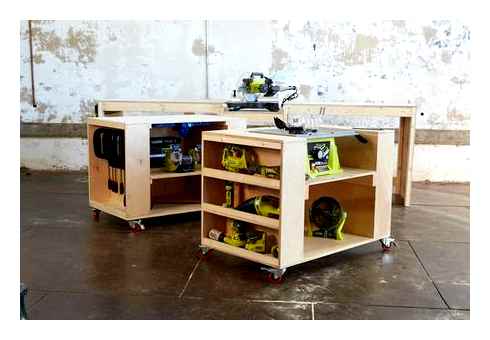
- The edges of the details become smooth without burrs;
- allows you to connect adjacent structures at an angle;
- There is no gap between them when connecting the parts.
The main advantages of working with home.made ending:
- Firstly, saving on the purchase of building material;
- Secondly-the technical characteristics of the tool created can be selected yourself: engine power, size of the detachment circle, cut depth.
- The duration of operation depends on the type of material that is used when creating equipment;
- Homemade is not equipped with security systems;
- home devices do not have a special graduation.
For reference! How to make a trim from corner grinders you can look at the YouTube channel.
Varieties of end saw
These simple devices allow you to perform even incisions at a straight and arbitrary angle. Before you make a trim with your own hands from a manual circular saw or corner grinder, you need to familiarize yourself with the types of structures.
Simple but Highly Functional WORKBENCH with Table Saw and Miter Saw Stations
Pendulum
Small size of the machine where the cutting disk is fixed on the pendulum. The blade moves back and forth, and the processed canvas can rise up and down and rotate. Thus, it is possible to adjust the cut angle.
Combined
The design of the equipment includes an additional table for sawing the material. There is an opportunity to change the angle of sawing in the process of work. Used simultaneously in the form of a end saw and circular.
For reference! Combined devices at home are rare, basically these are carpentry workshops.
With a length
Designed for a complex sawing angle of high accuracy. It is easy to use them, diagonal cutting is impeccable. A feature of the tool is a rotary module that simplifies the work.
Bosch GTS 635-216 sawing table
The equipment is intended for light, fast and accurate cuts in size: leaf plywood, wood-based stove, boards and other woodpeckers based on wood. This is a mobile circular machine that can be fixed on a workbench or special legs.
Bosch GTS 635-216 countertop is a metal. The working surface of the table is 500 × 658 (mm). There is a longitudinal and transverse stops on the countertop. The height of the machine is in the range of 553 (mm). The body of the equipment is plastic, which made it possible to noticeably alleviate the mass. The device weighs only 22 (kg).
The machine is regularly equipped with a 216 disk (mm). The maximum cut depth is 70 (mm). The main advantage of Bosch GTS 635-216 is the possibility of both direct cut and cut at an angle of 0-45 °. To set up cutting modes, practical and reliable regulators are provided, equipped with a measuring/degree scale.
The saw installation has power at 1600 (W), while the speed of the disk reaches 5500 (rpm).
In the Bosch company store, about 500 are asked for this model.
Features of the table for circular saw
Making a table for a circular saw with your own hands is very simple, especially if you have at least a small experience of a carpentry business. Experienced masters can collect it even without schemes. The design of the two main parts consists:
Additional departments in the form of boxes are not required, but if desired, you can create such projects.
one
2
Remember that the saw itself should be securely fixed under the table, and only the disk remains on the surface. The opening of the table for the circular saw should be a few centimeters more than the disk so that the sawdust can easily fly down without clogging the mechanisms.
Do.it.yourself ending table for a trumped saw should be done as strong as possible. Since the greater the power of the tool, the greater the load will fall on the surface. Be sure to consider this fact when choosing a material and a place to install it. Knowing how to make a table for a circular saw, you can save money well and delight yourself with a more convenient use of the tool.
The choice of dimensions
Choosing the size of the sawing table is worth it depending on the quadrature of the workshop. A small area of the room allows you to use a countertop 50 x 50 cm. It makes no sense to make a sawing table less. it will be difficult to use it when processing long blanks. A universal size that provides convenient sawing laminated wood-bearing plate-80 x 80 cm.
The maximum recommended dimensions of the sawing machine is 120 x 120 cm.
To comply with safety requirements, it is recommended to place the saw in the middle of the countertop at a distance of at least 25 cm from the edge. it is this indicator that leads to a minimum width of 500 mm. The location of the sawing disk also depends on how it will be used. There are three varieties of structure in total:
The depth and location of the disk installation depend on the workpieces processed on the machine. For boards and plywood, he should protrude 50–80 mm above the countertop, for logs. 110–125 mm. The height of the upper part of the frame from plywood sheets or laminated wood-based plate can be in the range of 35–40 cm. If you make a bed only from the beam, this parameter depends on the section. The remaining part of the structure is wooden legs, the size of which masters usually choose under their height. The total height of the sawing table is about 1.0–1.1 m, but can decrease to 900 mm.
Creating a drawing
The first stage of the creation of a wood processing machine is drawings of a sawing table. They can not be compiled by choosing a suitable option on thematic sites or forums. But it is better to make at least the simplest scheme on your own, given the available materials and selected sizes.
The drawing is noted all the nuances that are needed to prepare materials, indicate the places of fastening of the supports and the angles of their inclination if the tables of the table are not perpendicular to the countertop. In the figure, it is also worth noting a place for attaching the turning unit and off unit. With independent drawing up the scheme, compliance with scale and accurate proportions is not necessary. The main thing is to correctly indicate the dimensions of all future parts for the sawing machine.
Necessary materials
A homemade table can be made of wood
For such a table, wood, plywood or laminated woody plate can be used. A wood-fiber slab and wood-based slab are also suitable. Some prefer to choose steel or aluminum.
Circular machine table from a steel plate
It is not recommended to use plastic, it is completely unsuitable for a table of this purpose. If wood is selected, then after the assembly is completed, the product should be treated with a special antiseptic composition. This will provide reliable protection against humidity and help to avoid decay.
To make a saw table yourself you need to prepare materials.
- Selected raw materials for the base. The thickness should be 21 mm.
- The beam required for the frame. A fit board 3 meters long with dimensions 50 by 150 mm is suitable. You need 5 pieces.
- Woods of wood with dimensions of 10 cm. At least 12 pieces.
- The carpentry glue.
- Metal mounts in the amount of 4 pieces.
- Metal corners. 10 pcs is enough.
- Self.tapping screws.
These elements must be prepared in advance and placed near the workplace.
Necessary tools
In addition to materials, tools should be prepared.
Waterfall End Table with Hidden Spline Miter Joint // Woodworking Joinery // Modern DIY Furniture
- pencil and marker;
- Measurement tools, including meter and roulette;
- electrician;
- manual frezer;
- grinding machine;
- sandpaper (should have medium or fine granularity);
- rubbish and drill;
- Electric screwdriver.
You need to prepare everything in advance and keep at hand throughout the process.
Tool device
Crouping saws are a small size of the device, which are rigidly fixed on the workbench by means of screw fasteners. The stream of workbench has a cast design and maintains the stability of equipment when processing large blanks. As part of a stationary end of the end of the tree, you can find such mandatory elements as a handle, an electric motor, a cutting head and a massive base. If you proceed from the reviews of the owners, this tool requires certain skills for an effective solution of emerging tasks, and also needs careful maintenance.
Absolutely any saw needs preliminary setting, regardless of the company and model. This is like the first maintenance. The main thing required from the saw is the accuracy of the angle of inclination and with a turn. Any saw can be finalized, improved and raised its class. Remove all additions and extensions from the tool, for example, clutch. You will need a scalpel or a small knife with a non.bent blade. The castle is accompanied by the formation of a gloss that needs to be cut off if it interferes with the maintenance.
Lateral emphasis
In some saws, it has no right angle with the bed. The emphasis is in contact with the base at two points. The bases of these points should be vertical surfaces. If there is no right corner due to an uneven layer of paint or burrs, polish the basic surfaces. First cut it out if it is.
Make a small chamfer in places of contact with the base. So that the shavings that inevitably arise when sawing are hidden here. This is necessary so that the chips do not interfere with the formation of the desired angle of the cut.
Set the emphasis on place. The fasteners of the stop are made oblong to regulate. When installing it can be moved forward and forth and rotate.
Node of turning the turn
Two dragged two types of lim. On one line is a removable element. On the other, it is not dismantled, and the limb itself has slots for frequently used angles.
Limb with slots for quick installation of angles
The stem for fixing has conical sharpening and is not fully included in the slice.
Raise the fixation key. The rod will be freed.
Unscrew the flaps of the fixation unit. Remove them. Remove the stem. Sprinkle his pointed end so that he fits tightly into the slot.
How to fix an arbitrary angle
There are situations when you need to put an angle that differs by 1-2 degrees from a fixed value. When installing such a corner, a breakdown and fixation of the size that we do not need is. To prevent this from happening, you need to tighten the fixation handle with a key pressed.
Examination of the angle of 90 degrees in a horizontal plane
Most often, users apply the square to the disk and the base. This is the wrong way for three reasons:
- During the installation of equipment, garbage could get and equipment was installed unevenly;
- The disc itself was deformed;
- When we apply the angle to the equipment, enough light load so that the disk sways a little.
Prepare a piece of plywood, a thin rail, a 10 mm thick rail and double.sided tape.
- Take a piece of plywood and fix it on the basis of double.sided tape at three points.
- Between the plywood and the lateral emphasis, put the thin rail. She creates a distance in order to then correct the screws and move the emphasis in the right direction.
- Make a control cut. You will put an angle from him.
- Remove the rail and weaken the stop screws.
- In order to precisely manage the square relative to the cut line, use the rail with a thickness of about 10 mm.
Press it to the faner, and then press the square to it.
Setting up other corners with plywood
Cutting for cutting
Take a bar and put vertically. Make a cut. Check the combination of details.
If you need tuning, then you do not need to use a rail. There are two screws in the back of the end saw. The lower angle of 90 degrees is adjustable, the upper. 45 and other values.
Preparatory stage
During this period, you should answer for yourself the questions that were described above, and then draw a sketch of the construction of the product.
It is advisable to calculate all geometric dimensions and mounting nodes, both table elements (legs, working surface, additional elements), as well as mounting units to the base.
Performing table manufacturing
Table without additional stops
The frame can be made from a metal profile of various crossings available in stock. The geometric dimensions of the frame depend on the available area where the equipment will be mounted, the size of the end saw and the type of installation (stationary or portable).
On the frame, it is necessary to provide the place of installation of the saw, which must correspond to the available (geometric dimensions, the height of the lower mark of the possible cut, the possibility of changing the spatial location).
Regardless of the size and shape of the frame, it is necessary to provide side table extensions, which can be made of durable plastic, sheet metal or plywood. The presence of lateral extensions of the working surface will facilitate the cutting of a long blanks. If the lateral extensions are located below the level of the surface of the end saw, then it is necessary to provide the installation of special shelves by which the blanks will move.
Lateral stops will be useful, thanks to which, after they fixed, you can handle a large number of blanks by the installed size. As stops, you can use corners from different types of metal, equipped with clamping elements, through which stops are fixed on the working surface, as well as other elements (beans, bars, etc.D.) made of wood or plastic, which can be fixed on the working surface of the table.
For the convenience of performing work with a large number of blanks, it is necessary to make clamping plates. To do this, you can use a sheet metal or a metal profile, which must be equipped with devices that allow you to perform hard fixation on the desktop. It can be a bolt or other connection, while one of the plates is placed under the surface of the table (lateral expansion), and the second above the surface of the workpieces. Compression is carried out by tightening a bolt or screw connection using nuts or shanks.
- Installation of the end saw. When the work on the manufacture of the frame and additional elements are completed, it is necessary to install the frame on the prepared surface and tightly fix it there. After this, install the end saw and manufactured additional elements.
- Checking performance. After the installation of the saw and other elements that facilitate the work on this type of cutting tool, it is necessary to check its performance.
If you simply include it in an electrical network to check the saw, then to check the convenience of doing work on the manufactured table, you must do a certain work, ending the prepared blanks. In this case, it is necessary to check that:
- The geometric dimensions of the table allow you to perform all types of operations that are supposed to be performed on this equipment;
- The table and the end of the saw are rigidly fixed on the surface of the floor or other plane;
- The size of the extension corresponds to the size of the workpieces, they are easily moved and fixed;
- Setting stops and clamping plates is not difficult for any irregularities on the working surface of the table and the elements of the frame.
A support table for a end saw is a design element that allows you to work with high labor productivity, which ensures the safe implementation of operations for processing various types of materials.
Step.by.step instructions for assembling a table for a circular saw
First of all, you need to choose the size for the future design. Focus on the dimensions of wooden blanks, which are then planned to be treated with a saw.
For small details, a wide table is not required. It is also important to imagine where the design will stand.
You can use a drawing from the Internet or make a sketch on your own with sizes.
Step two. choice of material. It is allowed to use existing on the farm. If there are no stocks, then you need to raid the construction market.
Next, all the blanks are cut along the length and assembled. The algorithm of actions is as follows:
- The frame is created.
- The disk is mounted and fixed.
- The place on the countertop is pretended and marked, where it will drink under the tool.
- Work is carried out on its device.
- The working surface is installed and fixed.
With high strength and significant thickness of the material surface, it is appropriate to fasten the saw platform directly to it.
In this situation, the equipment is first mounted on the hand table, and only then the finished block is installed on the frame. However, a more reliable solution is to organize separate supporting corners and strong bars for the tool.
It is impractical to describe in more detail the process of creating a table for the circular, since the installation device can be any.
Frequent errors
So that the beginners succeed, it is useful for them to study the list of most commonly made errors compiled by experienced craftsmen:
- The choice of fragile material and low.quality fasteners, the organization of insufficient amount of transverse connections. Over time, the construction will lose stability.
- Application of the material of an inappropriate brand for a working countertop. The probability of deformation will increase.
- Fixing the saw is weak or to a weak basis. During use, the tool may fall out or change the installation angle.
- Lack of free chips emission. After a certain period of time, the space clogs, the motor begins to overheat.
- The hardness of the place to collect sawdust. This makes life difficult to the master.
- Inaccuracy or insufficient size cut under the disk in the countertop. The result is the impossibility of tilting the saw for sawing at an angle, friction of equipment on the edge.
- Inconvenience of access to the control button.
A table for a circular saw is necessary for everyone who is dealing with wood processing. You can not buy it, but make it with your own hands from improvised materials.
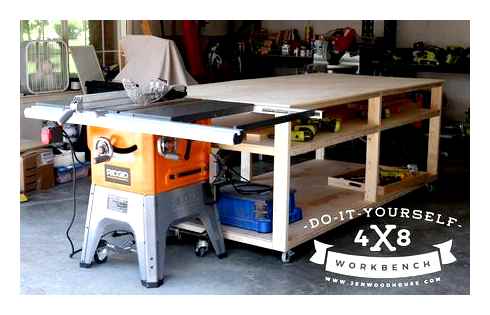
This will cost cheaper and allow you to organize the workspace as conveniently as possible.
Stages of manufacture
For example, the work was taken when the old table served as the basis for the machine. If this is not, then before the following described works, you need to make another basis. Bars of the same length for the legs are used, the design is enhanced by transverse elements. The base should be strong and stable to withstand active operation. After that, work with the countertop begins.
Stage first
In accordance with previously prepared dimensions, the working surface is cut out. By the way, you can even use an old countertop with, for example, a kitchen table. The main thing is that the material is durable and withstand all mechanical loads.
An important characteristic. the thickness of the countertop. The joiners say that it is best when the thickness is 2 cm. Such a countertop will be strong, from which material it would not be made, and leave a large working surface of the saw. Simply put, the more the disk “sticks out” from the machine, the deeper it can saw.
The edges of the boards should be finished and polished if possible. This is important not only for a beautiful appearance of the design, but also for its durability and work comfort. Yes, and no one wants a splinter.
Stage second
A hole for a circular saw is made in the countertop. Remember that it should correspond to the size of the disk. Also, on the surface of the countertop, you need to draw the installation and fastening of the saw.
Stage third
Holes in the working surface are made to fix it to the base. The countertop is turning over. To firmly connect these two parts of the machine, self.tapping screws and steel corners use. By the way, so that later the saw installation process is more convenient, the countertop can not be fixed immediately.
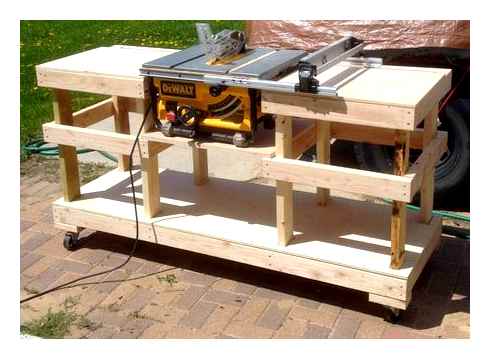
Fourth stage
The power supply and inclusion system of the device is equipped. The design provides that the saw will always be turned on, so you need clamps to fix the corresponding button. The launch and stop of the machine will be controlled by turning on and off the power supply. Therefore, you need a regular switch, cable, and a socket.
If a person who conducts work is not friends with electricity, then it is better to call a specialist.
A socket is installed inside, a power cord for a switch is displayed from it. It is the switch that will launch or stop the machine, so it should be at hand, so that in the event of an emergency, the master can quickly turn off the saw with one click by clicking. All this is connected to the nearest outlet in the working room.
Stage fifth
The frame is made for convenient work with a transverse cut. You can make such a carriage out of a thin base and two low walls. For this, wood and plywood are suitable. For the design to be mobile, guides are prepared for the table. It can be small parts of a steel pipe with a section of 2 × 1 cm. Pipe segments are mounted in the grooves that pre.carved by milling. Such a simple design will significantly increase the capabilities and comfort of the machine.
The guide carriage can be made of different materials, but there is a requirement for it. the presence of the adjustment function. The ability to configure the machine for the dimensions of the boards and the presence of emphasis for work at an angle. important characteristics. If it is difficult to do this with your own hands, then in stores there is a finished design of this purpose.

The sixth stage
The accuracy of the work is important, so the camp is necessarily equipped with a marginal ruler. With the help of a milling cutter, a small groove is made to install a ruler. If there is no such tool, then the groove can be prepared with a chisel. The surface of the countertop is carefully processed with a grinding machine and sandpaper. The line is most convenient to fix with the help of self.supporting bolts. This modification will make the cut of material with an accuracy of a millimeter.
Additional design improvements
For convenient use of the machine, the design improvements are carried out. Often install a container for collection of chips, a stream with dust remote for cleaner operation. The working surface can be made folding, which saves space, and even lifting, which will provide quick access to the saw.
Some craftsmen remove the casing from the tool, which is why the large working surface of the saw disk is available. A special bar for pushing boards is also prepared. This is important for security. In order not to lose this block, a special stand is made for it or drawer.
Installation of a circular saw in a homemade table
If the design of the circular saw does not have special holes for attaching to the table, then they must be done. It is important to take into account that even drilling additional holes is considered a modification and leads to the loss of a guarantee.
The circular in the table is attached from below. If the countertop is not yet attached to the base, then you can simply turn it over. If attached, it is better to turn the entire table, or put it on the side, it will be more convenient to work. It is necessary to fix the tool so that the hats do not protrude beyond the plane of the working surface.
To install a saw machine is not necessary to drill. Fastening can be carried out on clamping bars and screws. After installation, the countertop is turned over and fixed in the rest of the machine with screws.
To increase the maximum possible depth of work, equip a special elevator, thanks to which the saw disk rises. This is not necessary, but with the device for lifting the circular saw will be much more convenient.
The elevator is installed on the frame frame using a steel sheet. To raise the saw, the bolts are twisted. The necessary height is regulated by nuts. They will fix the device at the desired height.
Correctly conducted calculations, a competent structure of the frame and a securely fixed countertop with an installed saw will make the cut of the material quickly and efficiently. There is nothing superfollable, all the work is quite possible to do it with your own hands. Highly specialized tools are also not required, everything is either at home, or you can borrow, take it for rent.