Features of the asynchronous motor angle grinder
In almost all electrical appliances used in everyday life, an asynchronous electric motor is used. An important advantage of this type of motor is that when the load on it changes, the speed does not change. This means that if, for example, you cut a stone for a long time and without stopping a household angle grinder, there will be no noticeable external signs of engine overload. The speed of rotation of the disk will be constant, the sound is monophonic. Only the temperature will change, but this may not be noticed if the hands are wearing gloves.
With an inattentive attitude, an advantage can turn into a disadvantage. Asynchronous motors are very sensitive to overheating, a significant excess of the operating temperature entails a melting of insulation on the rotor windings. At first, the motor will work intermittently, and then. when an inter-turn short circuit occurs. the engine will stop completely. It is necessary to overheat the engine several times with an angle grinder and, most likely, the anchor will melt. In addition, contacts connecting the wires of the primary winding to the collector are soldered from high temperature, which leads to an interruption in the supply of electric current.
How to determine the malfunction of an anchor angle grinder
Signs of an anchor breakdown in an angle grinder are: increased sparking of brushes on the motor manifold, vibration of the motor at low speeds, rotation of the working shaft in different directions. If such symptoms are present, work with the tool should be stopped. this is dangerous. Suspicions are easy to verify with simple tests.
Visual inspection from the outside
Troubleshooting should begin with a visual inspection of the angle grinder:
- Carry out a general inspection of the tool.
- Pay attention to the integrity of the power cord, the presence of voltage in the outlet.
- Using a voltage indicator, make sure that current flows to the engine manifold and start button.
Inspection of the device from the inside
If everything is in order with power, but the angle grinder does not work, you will have to open the case to gain access to the motor. As a rule, disassembly is not difficult. But you need to adhere to simple rules that will avoid troubles during the reverse assembly:
Inspecting the motor is best done under bright light, so that all the small details are clearly visible. The anchor should rotate freely around its axis, properly working bearings should not make a sound during operation. There should be no traces of melted wiring at the anchor, the circuit windings must be intact, without breaks. You can smell the rotor. During interturn closure, the insulating varnish burns and emits a stable specific odor. But for such a diagnosis, some experience is needed.
Circuit Tester
If a visual examination does not give obvious results, it is recommended to continue the examination with a multimeter. Having set the mode switching toggle switch to the ohmmeter position (range 200 Ohms), it is necessary to “ring” two adjacent anchor lamellas with two probes. If the resistance on all turns is the same, it means that the windings are working. If on some pairs the tester shows a different resistance or an open circuit, there is a malfunction in this coil.
Rupture of the wiring may occur between the winding and the core. It is necessary to carefully examine the junction of the coils with the collector lamellas in the lower part of the armature, visually check the soldering of contacts.
Checking contacts with a light bulb
If there is no tester, you can get out of the situation with a simple 12 volt bulb. Power can be any, optimally 30–40 watts. The voltage from the battery 12 volts must be fed to the plug angle grinder, inserting a light bulb into the gap of one wire. With a working anchor, if you rotate the spindle by hand, the bulb should light up without changing the brightness. If the glow changes, this is a sure sign of an inter-turn short circuit.
If the light does not light, then this may indicate the following:
- Hanging of brushes in a non-working position is possible. The retaining spring worked.
- There was a break in the supply circuit.
- A short circuit or rupture has occurred in the stator winding.
There are other diagnostic methods, but they require more sophisticated equipment, which is usually not used at home. An experienced master will determine the failure with a high degree of accuracy using a “punch” or a simple transformer with a cut toroidal core and one primary winding.
In what cases can you save the anchor and restore it with your own hands
If damage to the armature is established with guaranteed accuracy, the part must be removed from the electric motor. The motor must be disassembled with special care, after removing the brushes and disconnecting the power terminals. The rotor is removed along with the thrust bearings and the cooling wheel of the motor, they form a whole with it.
If most of the wiring is damaged in the anchor and the balance is disturbed as a result of overheating, it is better to replace it entirely. An imbalance is indicated by increased vibration and an uneven hum during the operation of the mechanism.
How to rewind an anchor. step by step instructions
If the balancing of the armature is not broken, and the problem is only in damaged windings, then such an armature can be restored independently by rewinding the coils. Rewinding a rotor at home requires a lot of patience and accuracy.
The master must have skills in working with a soldering iron and devices for diagnosing electrical circuits. If you are unsure of your abilities, it is better to take the engine for repair to the workshop or replace the entire anchor yourself.
For independent rewinding of the anchor you will need:
Before rewinding, it is important to count the number of turns of wire in the winding and wind the same amount of new conductor onto the coils.
The rewinding process consists of the following steps:
- Dismantling of old windings. They must be carefully removed without damaging the metal body of the anchor. If any burrs or damage are found on the case, they must be ironed or sanded. Sometimes, to completely clean the body of toxins, masters prefer to burn it with a burner.
- Preparing the collector for connecting a new wire. There is no need to remove the collector. It is necessary to inspect the lamellas and measure the contact resistance with a megger or multimeter with respect to the housing. It should be no more than 0.25 megohms.
Replacing the anchor yourself at home
Practice shows that if it is decided to replace the anchor with an angle grinder, then it is best to change it together with the thrust bearings and the cooling wheel of the engine.
To replace you will need:
- New anchor angle grinder. Must fit your model. Interchange with other models is not allowed.
- Screwdrivers, wrenches.
- Soft brush and rags for cleaning the mechanism.
How to remove the anchor
Replacing the anchor begins with the disassembly of the angle grinder. The following steps are taken:
- The brush nodes are twisted with a screwdriver on both sides. Brushes are removed.
- 4 screws securing the gear housing are removed.
- The gearbox cover is carefully opened and removed to gain access to the inside of the gear mechanism.
- The snap ring is removed, fixing the small gear on the anchor.
- The anchor retainer is released from attachment, the anchor is removed along with the small gear and bearing.
- The gear, the bearing and the fixing disk of the anchor are removed, wiped with a rag. The bearing is removed with a special puller.
Video: replacing bearings with an angle grinder
How to anchor in place
To reinstall the new anchor, the angle grinder should take a new part, and then assemble the tool in the reverse order. The sequence of actions is as follows:
After performing these steps, the angle grinder is ready for use. Replacement of the anchor made.
Video: how to check the angle grinder
Ancient Sufi wisdom says: “The person who is able to get out of a difficult situation with dignity is smart. But wise is he who does not fall into such a situation. ” Observing the rules for operating household appliances, preventing the motor from overheating, you can avoid breakdowns and troubles in the work of an angle grinder. Keeping the instrument clean and dry will prevent its mechanisms from contaminating and oxidizing current-carrying elements. Timely maintenance of the tool is guaranteed to relieve unpleasant surprises during operation.
How to repair the punch yourself?
Many of my friends, regular users and guests of the forum, often ask a question, for example. how to fix a punch?
It seems like a simple question, but with the advent of experience, I begin to understand that the more I know about it, the more difficult it is to give a simple answer to a person who either does not understand this at all, or knows but a little.
After all, if you think about it, then a great many associated questions arise. what model of a punch, what brand, what kind of malfunctions are manifested?
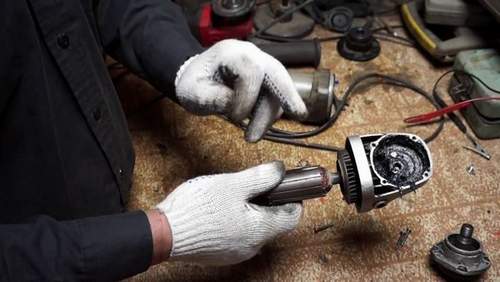
And even if a client or friend knows the answer to this question, it still does not give a 100% guarantee that he correctly identified the cause of the malfunction and made a quality repair.
Therefore, before repairing your faithful “friend”, you need to know your level of knowledge in the field of repairing power tools and whether you have had experience with such events.
When you find out the model and brand of your model of a puncher. do not be lazy and use the search on our forum to discuss whether the repair of your model is in fact because there are now a great many different models and their modifications on the market that it is no longer difficult to verify the different features of their designs.
r />
For example, for some models of Metabo rotary hammers, the mode switching mechanism is so complicated that not every experienced mechanic in the service can assemble it the first time.
And for example, a simple Makita HR2450 punch mode switch. if you do not know how to remove it, it can be damaged.
If you have collected information on your instrument and are aware of your strengths, then feel free to take up diagnostics to identify a malfunction.
To do this, you must have at hand a screwdriver with shanks suitable for screws, or bits for a cordless screwdriver, a multimeter to detect electrical malfunction of the rotor, stator and switch.
The easiest way to check the health of the entire electrical part of the punch is to plug it into the network. If the punch is turned on, it’s already good. it means the cable is working. If the switch, when you pull the trigger, adjusts the speed, it’s also wonderful, so it works properly.
Next, we look at the absence of circular sparking on the rotor manifold, if it is present, this can mean two things. either interlight breakdown on the rotor or a malfunction of one of the stator windings (sometimes when the tool is overloaded and both can burn out).
If a rotor malfunction is detected, we disassemble the punch, first we remove the handle plate and carefully remove the carbon brushes (a frequent mistake for beginners. the brushes break off when they begin to disassemble immediately with the motor unscrewed), after the carbon brushes are pulled out, you can unscrew the fixing screws of the motor case.
Then carefully remove the motor housing leaving the rotor in front of the perforator (gear). Usually, if there is a breakdown between the lamellas on the rotor manifold, it is visually visible and no multimeter is needed, but there are hidden malfunctions that can only be detected using the device.
To check the rotor for breakdown. you need to take a multimeter to set the value to 200 Ohms, and carefully check with the probes every 2 adjacent lamellas.
The difference in resistance between them is permissible only for Chinese punchers, if your puncher is of a German or Japanese brand, despite the fact that many people are now producing them in China too, but the quality still remains at the level. That resistance difference should not be at all.
Most often, when the breakdown is obvious, the multimeter, when ringing, may not show anything at all. it means precisely between these lamellas and the breakdown.
I must say right away. forget about the repair of the rotor and get a new one. Of course, many can object, they say, you can give it to rewind. but firstly, not every rewinder will agree to this, because after rewinding the rotor, it needs to be balanced correctly, and this is not given to everyone, as well as rewinding.
In my practice, the rewound rotor has never lived longer than a new one. Perhaps the wrong rewinders just came across, but why should I guess and look for the reason, if it is easier to put in a new spare part and be 100% sure of it.
And so on. if everything is ok with the rotor, then we check the stator. it’s still easier here, we look at where the ends of each winding go out and separately check them for the difference in resistance.
Video: How to Relieve Anchor From Angle Grinder
If the resistance is normal, then the stator is intact. Of course, no one excludes during the diagnosis and visual inspection. Since there are cases, for example, wear of the front rotor bearing due to which the rotor can “shoe” (this is usually called the nature of the malfunction in which the rotor starts to touch the stator housing).
Punch gearbox disassembly
We begin to disassemble the mechanical part, it is best to squeeze the (slightly) gear case into a vice. this allows you to conveniently and safely disassemble the gear, then begin to disassemble the cartridge (if it has a collapsible design), with some punchers the cartridge is simply removable on the latches. After disassembling the cartridge, remove the mode switch.
Attention: I strongly advise you to familiarize yourself with its scheme and, if possible, with the repair and disassembly of any power tool
repair manual, this will allow you to carry out repairs safely for your health and wallet.
If you have already removed the switch, carefully remove the gear housing and what do we see? Correctly the gearbox is all in grease and usually in black. In order to properly carry out the repair or diagnostics of the punch, it is advisable to wash and clean all parts
You can rinse in different ways. there are special cleaning solutions, for example, solutions for high pressure washers, there are regenerating solutions (which themselves restore their structure, but of course it doesn’t last forever), the advantages of these solutions are obvious. they have a non-toxic and pleasant smell, high washing properties and safe for human health.
However, there are also disadvantages. they are very expensive and only service centers use them. There are also old proven tools. washing with kerosene, gasoline and diesel fuel.
But they are all toxic and harmful to humans, and after them the oil film remains on the spare parts, which, for good, also needs to be washed with hot water.
The forum has separate topics on how best to wash spare parts and how, do not forget to use the search.
Well, with a sink figured out what next? And then when all the parts are dry and clean, check for gear wear, their gear teeth and splines of the couplings.
That’s it. I wish you successful and high-quality repairs, and if there are difficulties, our forum and experienced users will answer all your questions.
The device and purpose of the angle grinder
angle grinder is designed for grinding and cutting various materials.
The main elements of the angle grinder
The angle grinder consists of the following elements:
- The aluminum alloy flat gear housing dissipates heat better.
- Carbon brushes.
- Grip mount
- Electronic soft start system. Prevents jerking when turned on and reduces starting loads on the engine.
- Quick detachable guard.
- Ball bearings.
- Electric motor
- Switch angle grinder.
A wide selection of bearing products is offered by the Thermopolis company. https://termopolis.com.ua/
Main malfunctions, their causes and diagnostics
The main breakdowns and causes:
- Burns, sparks and twitches. Reasons: violation of the insulation of the armature winding, wear of the brushes, collector, clogging of the brush holders. Even after replacing the brushes, the angle grinder sparkles and twitches if the brush holders are clogged.
- Clapping sound. Brushes or interturn circuit of any of the windings.
- Crispy sound. The reason is in the bearings.
- Mechanical rumble and heavy tapping. Gearbox malfunction.
- angle grinder has stopped working, does not turn on. If the disk is manually spinning tightly or not spinning, the cause is the gearbox. If it turns easily, check the electrical circuits. If chains work, check motor and brushes.
- The spindle lock button has broken. The reason is clicking on it during rotation of the disc or jamming of the disc.
- The angle grinder works in fits and starts. Check engine for interturn short circuit.
- Vibrates. The reason for mechanics. Check bearings, rotor shaft and gearbox.
- Heats up. If it heats up in the engine area, the cause is worn out brushes or a short circuit in the turns of the windings. If the gear case is warming, then the grease has dried or the gears have worn out.
- It does not gain momentum or power drops. The reason is in the electronics or engine. Check soft starter control board and speed controller, brushes and collector.
- Smokes. The reason is overheating of the tool. Check motor windings for insulation melting.
- Humming and not spinning. Check motor bearings and gearbox.
How to disassemble and reassemble the angle grinder
To troubleshoot the angle grinder must be disassembled.
-
Remove the nut that holds the working disk.
Turn off bolts of fastening of a protective casing.
Remove the housing bolts from the angle grinder and those that secure the housing to the gearbox.
Remove the top of the rear housing. Turn off bolts of fastening of a cord. Remove the wires and button from your grooves. In some models, for example, in DWT, the rear case is not disassembled into parts, but is removed entirely.
Remove the gearbox bolts located around the casing mount.
To disconnect the anchor from the aluminum housing, unscrew the nut located in the gear housing.
Reassemble the tool in the reverse order.
The clamping nut is not untwisted
During operation, the disk can tighten so tightly with a nut that it begins to crumble. It is not possible to unscrew the nut with a wrench. And you do not need to do this, since you can break the angle grinder. First, break the disc all the way to the nut. Then find the metal plate a little thinner than the working disk. Use it to drain off the rest of the disc under the nut. It can be easily unscrewed with a key or hands. In order not to bring the tool to this problem, put the washer under the nut.
How to remove a tightened nut
The casing cannot be removed
In some grinders, for example, Bosh, the casing is not bolted, but latched. To remove it, you need to turn the cutout of the casing perpendicular to the angle grinder. To dress, turn until it clicks.
Stator check
The stator is checked with a multimeter.
- Inter-turn closure. Set the resistance mode to 200 ohms. Connect the test leads to the ends of one winding. A unity means an open, and zero means a short circuit between the turns. If it shows a resistance of more than 1.5 ohms, then check the second winding. Both windings should have approximately the same resistance.
- Breakdown on the mass or shorting of the winding with the metal housing of the stator. In the multimeter, set the maximum resistance mode. Connect one probe to the end of the winding, the other probe to the metal housing of the stator. The unit indicates the absence of breakdown.
Anchor Check
First visually inspect the collector and winding. There may be visible damage: black marks, bent turns of the winding, raised, worn or burnt collector plates. After inspection, proceed with the tester.
-
Set the resistance to 200 ohms. Connect the test leads to two adjacent collector plates. If the resistance is the same between all adjacent plates, then the winding is working. If the resistance is less than 1 ohm and very close to zero, there is a short circuit between the turns. If the resistance is above the average two or more times, then there is a break in the turns of the winding.
The determination of the breakdown to mass is done in the absence of a winding break. Put the maximum resistance on the scale of the device. Depending on the tester, it can be from 2 MΩ to 200 MΩ. Connect one probe to the shaft, and the other to each plate in turn. In the absence of faults, the resistance should be zero. Do the same with the rotor. Connect one probe to the iron body of the rotor, and move the other along the plates.
Checking the power button
Put the tester in dialing mode.
Insert one probe into the output of the button and the other into the opposite input.
Click the button. A sound signal indicates the health of this part of the button.
Do the same with the other input and output of the button.
How to ring the start button
Power cord check
Connect one probe to the plug pin, the other to the button inputs. In one of two positions there should be a sound signal. Do the same with the other pin of the plug.
Check soft start and speed control
If the power button and power cord are working but the engine does not turn on, check the softstart control board. Remove the screw that secures the control board. Remove it carefully. Call all items. If there is a speed regulator in the angle grinder, then it can be connected in series with the power button and have one board with soft start. But may have a separate fee. It is checked similarly to soft start.
Precautions before starting repairs
- Read the instructions. Read the description and assembly diagram of the angle grinder.
- Unplug the tool.
- Prepare a workplace on a table with good lighting.
- Recorded on paper or on the photo order of disassembly tool to assemble it correctly after repairs.
DIY troubleshooting
If you are unsure of your abilities, it is better to take the tool to the workshop.
Power cord and power button
Damaged cord and button must be replaced. On the button, unscrew the bolts securing the incoming and outgoing wires. Disconnect it from the chain and install a new one.
Soft start and speed control
If only the triac is out of order in the control board, then a new one must be put in its place. Pre-grease the metal part of the element with thermal grease. If other elements of the board burn out, replace it completely.
brush
Brushes must be checked periodically. When one is worn by 40%, change both. And also clean the brush holders.
- To remove the brushes, you must either remove the rear housing or remove the plugs in the housing.
- Clean brush holders of dust and carbon deposits. Wrap a cloth around the screwdriver and moisten with alcohol. Nagar is cleaned off with a file. The brush should walk easily in the brush holder, then it will be well pressed by the spring.
- Insert new brushes.
Brush holder cleaning
Stator Rewind
For high-quality winding coils, you will need an enamel wire and an electric cardboard.
Remove the winding and old insulation from the housing. Look carefully at the slots. When the coils burn, insulation is burned and a short to the case occurs. Deposits remain on it, which must be removed with a file or a diamond bur. Deposits will interfere with the new winding. She may tear.
The winding is saturated with varnish. To disconnect the wires and count them, you need to strip out the insulation. Preheat the winding with an industrial hairdryer or any burner.
Burn matches or lighters with any fire to make the enamel completely burnt out. Take a micrometer and measure the thickness. Record wire diameter and number of turns.
Take any wire and make a loop out of it so that it fits in the grooves of the stator. Under the diameter of this loop, select a cylinder for winding coils. For example, spray can. If its diameter is not enough, then wrap the can with paper.
Wrap both windings from the enamel wire. Fasten the frontal parts with glass tape or thick thread. The thread should not break and melt. At the loose ends, put on shrink cambric.
Make sleeves from the electric cardboard and insert them into the grooves. Place the windings in them.
Check the resistance in the windings of the tester. If everything is fine, continue.
So that during operation the wires do not vibrate and do not rub against each other, they must be impregnated with any oil-based varnish. Put the starter preheated in the oven vertically and squeeze the varnish onto the winding with a syringe. When the varnish starts to leak from below, turn the stator over and soak on the other side.
When the varnish is dry, proceed to connect the windings. Connect the two ends of the different windings to each other and connect to the nearest brush. Connect the other two connected ends to the start button. Connect the wire from the second brush to the button.
Rewind stator on video
Anchor Repair
If the balance is disturbed, the anchor must be replaced. The winding and collector are subject to repair. Small short circuits are eliminated. If a significant part of the winding is damaged, it can be rewound.
A not very developed collector is corrected by a groove. But if the plates are erased to a plastic base or partially burnt out, then the restoration is carried out by soldering or galvanic building.
Badly damaged collector
If the collector was completely worn out, then after soldering it will be enough for no more than a month of active use. And not completely damaged plates after such a repair can withstand several brush changes and do not evaporate. You will need to cut the copper plates in size and solder them with a lot of solder. Strain excessively with a file and polish.
With galvanic build-up, reduced copper is very solid. The life of the collector is like new.
Completely restored collector
By galvanic build-up, it is possible to restore both a completely wiped collector and partially damaged plates. The restored collector must be grooved and the plates divided with a drill or hacksaw blade.
In order to rewind the anchor correctly, you need to correctly disassemble it and remove the parameters for the template:
- Winding direction.
- How many grooves and slats.
- The number of conductors in the groove.
- The winding pitch, i.e. how many grooves between the grooves of one section. For example, if the conductors exit the first groove and enter the sixth, then step = 5.
- How many conductors are in one groove, so many coils in one section.
- Wire thickness.
For example, 80 conductors in a groove, 12 lamellas and 24 grooves. 12 sections of 2 coils. The winding passes in two circles, so we divide 80 conductors in the groove by 2, and another 2, since there are 2 coils. We get 20 turns of one coil.
Anchor winding pattern
- We solder the beginning of the wire to the lamella 1 and pass it through the first and sixth groove. We make 20 turns. The first coil of the first section is ready.
- We solder the wire on the lamellas 2 and repeat the winding through the same grooves. The second coil of the first section is ready.
- We solder the wire on the lamellas 3. Pass the coil through the second and seventh groove. We wind the first coil of the second section and solder the wire to the lamellas 4.
- The second coil of the second section is fixed on the slats 5.
- We continue this until the end of the wire reaches the lamella 1
How to remove the old and rewind a new winding:
Use a hacksaw or wire cutter to remove the frontal parts of the winding.
Carefully, without damaging the slot insulators, knock out the rods of the remaining parts of the winding with a hammer and a metal chisel.
Use a file to remove any remaining impregnation. Count the conductors in the groove and measure the diameter of the wire. Draw a diagram. Cut the insulation sleeves from the cardboard and insert them into the grooves.
After winding, weld the conclusions of the sections with the collector plates. Check the winding with a tester.
Soak the winding with epoxy.
Anchor Bearings
Bearings crumble or jam over time. They need to be changed.
- Disassemble the angle grinder, remove the anchor from the stator.
- An anchor is inserted into the gear housing by a bearing. If the housing cannot be removed, fasten the rotor in a vice and tap the gear case with a wooden block.
- Remove the gear from the armature shaft.
- There are two bearings on the armature shaft. The one next to the collector is easy to remove. Remove the second bearing with a puller. If it is not there, hang the anchor by the bearing and tap on the shaft with a piece of wood. The hammer must not be used.
- Slide the new bearing on the manifold side onto the shaft. Place the second bearing into the gear housing on the rotor side. Insert the gear inside the housing and loosen the nut so that it fits into the grooves of the gear. Insert the anchor into the gear housing. Tighten the nut.
Gearbox disassembly and repair
The gearbox must be disassembled not only for repair, but also for preventive cleaning and lubrication.
- Remove the bolts and disassemble the gear housing. You will see dirty grease that needs to be removed.
- Swing the gearbox shaft to check the bearings. He should not hang out.
- Remove the snap ring from the shaft, nut and gear.
- Hang the shaft by the housing and gently tap the shaft on the shaft to remove it.
- Remove the snap ring from the housing that holds the bearing.
- Using a tip, such as an end head, knock the bearing out of the housing.
- Replace the bearing and gear if necessary.
- To insert the bearing into the housing, select the extension according to the size and tap it gently.
- To clean the gearbox, heat the housing with a hairdryer and
old grease will spill out of it. Clean parts with a rag or toilet paper. Flush the housing and parts with kerosene.
Spindle lock button
If the button has flown out, then such an angle grinder cannot be operated.
Spindle lock button
Since the spindle can spontaneously lower to the gear and block it during operation.
Spindle Lock
The locking unit consists of a spindle with a rubber ring, a spring and a plastic button.
- To replace the button, disassemble the gearbox.
- Remove the spindle from the housing.
- Put the spring on the button on the inside.
- Insert the spindle into the gear case from the inside, and the button from the outside. Press until it clicks.
- Assemble the gearbox.
Spindle lock button replacement and gearbox repair
Care and proper operation of the angle grinder
For the angle grinder to work for a long time, follow the rules:
-
Watch integrity of isolation of a wire, plug. Do not remove protection.
Lubricate and clean the entire tool.
After turning off the angle grinder, wait until the rotation of the circle stops, then lay it on the ground. When the engine stops, the tool through the ventilation holes sucks together with the air stream particles of earth and other hard fractions that hit the motor windings. As a result, an open or short circuit occurs.
If you are actively using an angle grinder, then you are a good master. It’s not difficult for you to understand the device’s device and repair it with your own hands. First, find the fault and determine which nodes should be checked. Repair the angle grinder carefully, without haste, so that a minor breakdown does not turn into a major one.