DIY Circular saw table
For the manufacture of the table, you can take the following materials:
Choosing saws in the store, the buyer often pays attention to the depth of immersion of this device, which means the maximum thickness of the processed material. It must be assumed that the use of a manual saw will not take approximately 1 cm of sawing thickness for the purpose
If it is assumed that the products will be bulky, for example, more than 2.5 m long, then the table will have to be strengthened with additional legs.
The circular table has several features in its assembly. The workpiece for the table cover should be described by a separate item.
So, for the countertops, legs from the same plywood are made, but more thick. To fix it, they make fixers along the table or cross. This will allow the table to be more tough. The stability will be affected by the correctly selected legs length, the installation site.
The table can have different sizes, the master determines these parameters on its own. For example:
Table manufacturing technology for circular saw
From plywood 20 mm performs the workpiece of countertops on the selected sizes. Design a plywood sheet with a pencil and a carpentry ruler, saw it with an electrician and milling the edges. The resulting workpiece is clicked.Perform the marking for the circular saw on the bottom of the countertop. To do this, turn the workpiece of countertops, install a saw without a disk in the proposed place and marked the dimensions of the sole. A manual milling mill is chosen in the countertop a recess of 8-10 mm at a marked landing place.
They try on the saw, adjust it if necessary, after which the places of its fastening and the slot for the toothed disk are marked. If you plan to perform the cut of the material from different angles, consider this when marking the slot. it will have a cross section in the form of a trapezoid by the top down.
On the bottom of the countertop, using a pencil and ruler, marking for stiffeners, to which the legs will be attached later. Stiffer ribs are made of boards 50×100 mm and placed around the perimeter at a distance of 7-10 cm from the edges of the table. They put the board to the countertop and circle it on both sides, after which its central line is marked along the line, and the location of the screws is noted on it-5 cm from the edge of each rib and after 15-20 cm along its entire length. Drill holes for marking through.
Make the markings of the boards for longitudinal ribs of stiffness and saw them. Fixed to the countertop on the carpentry glue with clamps. After that, the side ribs of stiffness are marked at the place, cut and glued in a similar way.
After gluing without removing the clamp, the structure is extended by self.tapping screws along the performed holes, having previously drilled them from the outside, so that the hats of the screws are completely recessed in the countertop.
Tighten the ribs of stiffness with each other by two self.tapping screws 50 mm on each side. Remove the clamps. The finished countertop looks like this.
DIY Folding Outfeed Table for Table Saw / Mobile Workbench EP 6
The legs for the table are made of boards 50×100 mm. The height of the legs should ensure the convenience of work, on average it is 100-110 cm. The board is cut along the longitudinal axis at a small angle on one side. Try them on the countertop so that when installing they stand slightly. Attach the legs from the outside of the ribs of stiffness on the bolts. To increase stability, you can make screeds from a bar of 50×50 mm.
Install a manual circular saw in the prepared groove on the bottom of the countertop, fixing the sole on the bolts, the gear disc is inserted into the slot.
It remains to solve the issue of turning on and disconnecting the saw. If you have sufficient knowledge in electrical engineering, you can make the switch of the inclusion key and take the control buttons to the outer surface of the front rib of stiffness. If this scheme seems too complicated to you, it will be enough just to tighten the key using the wire and turn it on and turn off the saw using a network cord.
Thus, as you were able to make sure to make a table for a circular saw with your own hands is a simple task that can be possible for any summer resident.
Production of the end machine
As lateral stops, I used a beam 44 cm, t.to. The maximum depth of cut my saw is 4.3cm. For the base, I used a furniture shield. But it is better to use a sheet of plywood, t.to. it is much stronger, and it certainly does not deform over time.
I glued the beam to the base, and also fastened them with self.tapping screws. I cut the excess part of the bar. As guides, I used aluminum corners. Corner thickness 2 mm. Under the weight of the circular he bend, so I decided to strengthen it with the second corner. It turned out a stiffener’s rib with a thickness of 4 mm.
To connect 2 corners, I glued bilateral cattle, combined the corners together, and then made several through holes for the screws. Hats of the screws need to be hidden flush so that they do not interfere with the slope of the saw along the guides.
I fix the guides with self.tapping screws. For each operation, you need to check the displayed angle of 90 degrees.
First we fix one guide. Then we install the second guide, take the saw and set the distance between the guides to the width of the sole of the saw.
We fix the second guide. The saw should glide freely along the guides, but at the same time not to have a side backlash. We make the first cut along the entire length of the guide.
For the manufacture of an stop under 45 degrees, I took another aluminum corner and cut it under the desired length.
I chose a place for its location. Made a through hole at the base of the guide. On the back of the board, he appressed the furniture nut.
From a saw saw a saw I put an angle of 45 degrees. Drill another hole for fixing. (The number of angles may be arbitrary)
My bromatic milling cutter and a disk saw, the same base width. Therefore, I can use the guide with the milling.
How to make a end saw
Let’s start assembly
- We cut a rectangular sheet of plywood and make a long drink on it, along which your end will ride;
- We fasten two guides on top, for example, from an aluminum corner, on the width of the working plane of the circular itself;
- Below to the plywood sheet, you need to fasten two stands with a height equal to the depth of your saw (5.3 cm).
As a result, we get a guide on which the circular will walk. Depending on how it is fixed on the table using such a simple mechanism, we can make an accurate cut at any angle. The easiest design option is ready.
But what if we want our ending to be more functional in work and look like a factory end saw? In this case, you will have to show more ingenuity.
- Firstly, it is necessary to make the bracket and the rack on which the circular will be fixed. Wood-steam plate (27 mm)-excellent raw materials for such a mechanism. With the help of screws and aluminum corners, you will get a very decent upper part of the end. And the springs fixed on top can make work on such a saw more convenient;
- Secondly, you need to fix the tripod itself on a mobile turning step, make a pendulum saw, so we will eventually be able to change the angle of ending.
Carefully! Not only the quality of work and the functionality of the end, but also your personal safety will depend on how reliably you will securely fix them on the footboard. No wonder they say that if the carpenter is experienced, then it is necessarily without a finger
Fix the circular, as reliable as possible! Safety precautions. above all!
As for the end itself, the assembly is said about the assembly. However, if we decide to make a saw that looks like a factory one, then it will be difficult to do without a table.
Making a cutting tool with your own hands
As one of the options for independent manufacture of a cutting tool, a case may be considered when an angular grinding machine (corner grinder) is used, which has already developed the time due to it. The performance of the operating parameters of the mechanism can be taken by the characteristics of the ending with a length designed for the following parameters.
The engine speed is about 4,500, and the length of the formed cut is 300-350 mm (the second indicator is much higher than that of the middle-class branded models).
The mobile part of the future home.made device is made on the basis of the old automobile wheel with a shkvorn, on the outside of which a ear is welded on the bearing housing to fix the base with a corner grinder. The latter is fixed on the case by means of the screws of the M6 size.
To protect against shavings in the user’s face, the resulting design is closed with a protective box on top. The length of the broach is made of old shock absorbers from the truck. First, oil is spilled out of them, and then ventilation holes are drilled in the housings (later they are closed with a special mesh that protects the mechanism from dust and chips).
In order to avoid a sharp jerk, well felt when the angular grinder is turned on, the manufactured tool is equipped with a special module that reduces speed during starting.
In the final part of the review, it is necessary to once again recall the safety of working with a tree endings, which belongs to high.speed mechanisms with a cutting disk. All this forces us to take special protection measures when treating it, consisting in the use of glasses and thick canvas mittens.
What should be a table for a saw
The base of the table on which the circular saw will be installed can be metal or wooden. Plastic for these purposes is not suitable. In the countertop, a hole is made under the disk. It should be made in it for rides support. They are designed to shift sawing material.
The table for the circular should meet the following requirements, to be:
Otherwise, during operation it will not be possible to avoid injuries.
Desktop device
Before starting cutting and assembling the table, calculate its dimensions and make a drawing. The hole in the countertop is cut under the saw, which is available. On the countertop, the plate must be installed so that it does not pull the table in any direction. The countertop put one that corresponds to the flow of sawing. In a spacious workshop for the circular, you can put a full workbench, in a small enough and folding with a removable saw.
Before the design is finally collected, all its wooden elements are recommended to be treated with an antiseptic agent. This will help protect them from decay and moisture.
Design requirements
Should not stagger both the design itself and its individual elements. Legs for it are required. It must be borne in mind that it is almost impossible to achieve stability if solid and thin plywood sheets are taken as a support. The disk in the design must be fixed reliably.
Selection of the necessary material and table manufacturing technology
Before attaching the circular to the table, it must be done correctly. They prepare with their own hands for the manufacture and installation of the table:
- Laminated woody boat or thick plywood;
- a beam for the frame of the table (you can take 5 trimmed 3 m of boards 50×150 mm);
- 12 wooden doughs 10 mm;
- 10 metal corners;
- 4 metal mounts for the tsar and legs;
- self.tapping screws;
- The carpentry glue.
- meter, roulette, marker;
- manual milling mill and an electrician;
- drill and electric screwdriver;
- grinding machine and rubbish;
- finely and medium-grained sandpaper.
The creation of the right drawing will prevent errors at the stage of assembly of the table. The drawing must take into account the fact that the bed should withstand all loads. The table needs to be specified. It is not bad if it is functional, to serve not only the working surface, but also the place where you can store materials and tools.
Take the basis, for its legs use bars of the same length. The design is enhanced by transverse elements. After receiving a stable and strong foundation, they begin work with the countertop.
At the first stage, on the basis of size, a working surface is cut out. You can take a strong countertop, previously previously in use. Its optimal thickness is 2 cm. The edges of the board are desirable to finish and polish. This will give the design a pretty appearance, it will be comfortable to work on it, splinters will not fall into your hands. This will simple and will last much longer.
At the second stage, the holes for the circular are drilled, they are made in accordance with the size of the disk. On the surface of the countertops draw a place. where they will install and attach a saw.
At the third stage, holes are made in the working surface in order to fix it to the base. The countertop is turned over and marking on the inside of the circular sole is applied on the inside. Cleeps make recesses. The saw is installed in a homemade table, fixed and checked for strength.
At the fourth stage, they move on to arranging a power supply system. The saw should be in the on state. To fix the corresponding button, you will need clamps. The machine will be launched and stopped under the control and off of electric power supply.
You will need ordinary products:
Inside put a socket from which the wire is removed. Since the switch will be launched and stopped, it is installed at hand. This is necessary in case of emergency. Connect to the outlet that is nearby.
At the fifth stage, they begin to make a frame so that it is convenient to perform a transverse cut. For a carriage, you need a thin base and 2 low walls, you can take a plywood and a tree. To make the design moving, guides are prepared for the table. small pieces of steel pipe with a cross section of 2 per 1 cm. The grooves are cut with a milling mill into which these segments of the pipes are mounted. The guide carriage must have a functions of adjustment so that the machine can be configured for the values of the board. There must be an emphasis at an angle at an angle. Those who cannot independently make this design can purchase ready.made in the store.
At the final stage, the machine is equipped with a marginal ruler, which will allow you to very accurately saw the material. To install it with a milling or chisel, a small groove is made. The surface of the countertop is well treated with a grinding machine and sandpaper. The ruler is better screwed with self.tapping screws.
Lastly, the legs are attached. Their height and dimensions depend on the master, it is important to securely fix them on bolts and screws. You need to put the legs a little display, the strength is controlled using stiffener ribs.
For the convenience of using the machine, many improve the design. So that there is less dust in the process of the saw, set a rack with dustwall, and for collecting shavings. a container.
Some make the working surface of the lifting, so you can get to the saw faster, or in order to save space. folding. A special bar is prepared for pushing the boards. This makes the work safe.
Fixing a hand saw
Before fixing the circular on the inside of the structure, it is necessary to study the options for fastening. There are several ways to adapt it, using bars with self.tapping screws or m4 bolts. In the first case, no additional holes need to be drilled. The second method is reliable and fast.
Any circular saw, including the Interskol, Makita model, requires careful handling. In order not to get an injury during operation, you need to follow how it is worth the saw table. Before each turning on the circular, check the reliability of fastening. When cutting the material, it is forbidden to hold it with your hands, you can injure your fingers. If the saw stumbles on a knot or irregularity in wood, there is a danger that the tree will bounced into the face. It is necessary to work in protective glasses so as not to damage the eyes.
The choice of dimensions
Choosing the size of the sawing table is worth it depending on the quadrature of the workshop. A small area of the room allows you to use a countertop 50 x 50 cm. It makes no sense to make a sawing table less. it will be difficult to use it when processing long blanks. A universal size that provides convenient sawing laminated wood-bearing plate-80 x 80 cm.
To comply with safety requirements, it is recommended to place the saw in the middle of the countertop at a distance of at least 25 cm from the edge. it is this indicator that leads to a minimum width of 500 mm. The location of the sawing disk also depends on how it will be used. There are three varieties of structure in total:
The depth and location of the disk installation depend on the workpieces processed on the machine. For boards and plywood, he should protrude 50–80 mm above the countertop, for logs. 110–125 mm. The height of the upper part of the frame from plywood sheets or laminated wood-based plate can be in the range of 35–40 cm. If you make a bed only from the beam, this parameter depends on the section. The remaining part of the structure is wooden legs, the size of which masters usually choose under their height. The total height of the sawing table is about 1.0–1.1 m, but can decrease to 900 mm.
Security requirements
One of the frequently found causes of injuries when using a circular saw is the clutter of the workplace
In addition, it is important to observe the stability, strength of absolutely all components of the system, and when disassembled. use measures to eliminate difficulties. Before connecting the saw, you must make sure that it is well recorded. With need. tighten the screws/bolts. It is strictly forbidden to hold the material close to the cut site! This is dangerous to bouncing knots, shavings in the eyes or on open parts of the body
You certainly need to put on glasses before work and clothes with sleeves.
Self.manufacturing a table for a saw is not such a difficult task as it might seem. If there is good material at hand, its characteristics are selected correctly, and the power of the device ranges from 500 to 1000 W, the above instruction will be the basis of the work.
It is not necessary to lose sight of the fact that at any stage of the table production, the accuracy of their own operations should be monitored. In a different way, when deviations appear in size or deformation of the legs when screeding ribs, it will be very difficult to resume stability. Nevertheless, the production of the table for the circular with your own hands is an absolutely real task for several hours.
Preparatory stage
During this period, you should answer for yourself the questions that were described above, and then draw a sketch of the construction of the product.
It is advisable to calculate all geometric dimensions and mounting nodes, both table elements (legs, working surface, additional elements), as well as mounting units to the base.
Performing table manufacturing
Table without additional stops
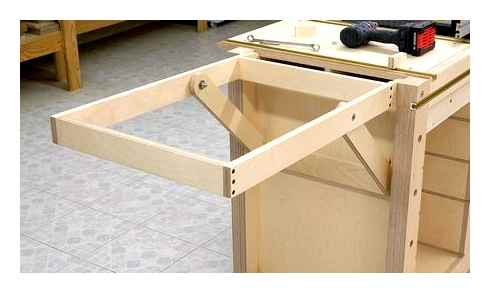
The frame can be made from a metal profile of various crossings available in stock. The geometric dimensions of the frame depend on the available area where the equipment will be mounted, the size of the end saw and the type of installation (stationary or portable).
On the frame, it is necessary to provide the place of installation of the saw, which must correspond to the available (geometric dimensions, the height of the lower mark of the possible cut, the possibility of changing the spatial location).
Regardless of the size and shape of the frame, it is necessary to provide side table extensions, which can be made of durable plastic, sheet metal or plywood. The presence of lateral extensions of the working surface will facilitate the cutting of a long blanks. If the lateral extensions are located below the level of the surface of the end saw, then it is necessary to provide the installation of special shelves by which the blanks will move.
Lateral stops will be useful, thanks to which, after they fixed, you can handle a large number of blanks by the installed size. As stops, you can use corners from different types of metal, equipped with clamping elements, through which stops are fixed on the working surface, as well as other elements (beans, bars, etc.D.) made of wood or plastic, which can be fixed on the working surface of the table.
For the convenience of performing work with a large number of blanks, it is necessary to make clamping plates. To do this, you can use a sheet metal or a metal profile, which must be equipped with devices that allow you to perform hard fixation on the desktop. It can be a bolt or other connection, while one of the plates is placed under the surface of the table (lateral expansion), and the second above the surface of the workpieces. Compression is carried out by tightening a bolt or screw connection using nuts or shanks.
- Installation of the end saw. When the work on the manufacture of the frame and additional elements are completed, it is necessary to install the frame on the prepared surface and tightly fix it there. After this, install the end saw and manufactured additional elements.
- Checking performance. After the installation of the saw and other elements that facilitate the work on this type of cutting tool, it is necessary to check its performance.
The Ultimate Hybrid Roubo Workbench
If you simply include it in an electrical network to check the saw, then to check the convenience of doing work on the manufactured table, you must do a certain work, ending the prepared blanks. In this case, it is necessary to check that:
- The geometric dimensions of the table allow you to perform all types of operations that are supposed to be performed on this equipment;
- The table and the end of the saw are rigidly fixed on the surface of the floor or other plane;
- The size of the extension corresponds to the size of the workpieces, they are easily moved and fixed;
- Setting stops and clamping plates is not difficult for any irregularities on the working surface of the table and the elements of the frame.
A support table for a end saw is a design element that allows you to work with high labor productivity, which ensures the safe implementation of operations for processing various types of materials.
DIY cut on wood
If the owner for home use needs a high.performance tool for opening and ending the boards and it is necessary to save, then you can consider the possibility of making it with your own hands. This is worthwhile first of all to think for those masters who have considerable experience in this matter and good training. First of all, you need to prepare the necessary tool for work:
- a set of files;
- welding machine;
- corner;
- steel sheet;
- an angular grinder engine with a capacity of at least 2.2 kW, operating at a speed of 2800 revolutions per minute.
To create a cutting machine, a number of stages must be performed:
The workflow begins with the manufacture of the bed. It cannot be done without it, since the end machine is a very bulky tool. As the basis for the bed, you can use a metal corner and racks from an iron bed. From a steel sheet, you need to make a working base. Using a file, you need to process its edges. For a future saw you will need a pendulum stand, for the manufacture of which a channel is used. The finished rack must be installed on a steel sheet
over, it is important to choose the right height, which should be 800 mm. The electric motor is installed on a special stand, which will move using hinges. In conclusion, it remains only to fix the box to the home.made cutting saw, which will protect the master from chips.
As the main working unit of the cutting machine is a sawing disk, which should have a diameter of 42 cm. According to users of home.made cutting saws, this is a great opportunity to save on the purchase of a corporate instrument, which often costs more than a do.it.yourself device.
TRASTER for the end of the end
Hello, dear readers and homemade!
In this article, David, the author of YouTube Channel “Make Someting” starts another optimization of the workspace in his workshop and wants to share the results with his readers.
This time he intends to get rid of uncomfortable stops on the table near the end saw. Even before, this emphasis was made by him along with the workplace. But over time, the emphasis was somewhat led, and this affected the quality of work. And then the author comes a wonderful idea: regular emphasis is not needed, a T-shaped profile, and a restrictive system will be required.
Materials leaf plywood from hazel. wooden beam. T. figurative profile. impregnation for wood, varnish. PVA glue. lamb screw.
Author’s tools drilling machine. circular saw. end saw. electric screwdriver.
Production process. So, first of all, the author dismantles the guide and removes the countertop.
On a circular saw, he cuts a new new blank from sheet plywood in size slightly.
Guide width ¾ inch.
He will make a groove in the countertop in two doses. In one pass, he will remove half the thickness of the groove, for the second. the rest of the material.
In the second passage, it is necessary that the milling cutter protrudes slightly above the profile, so that the track itself lay slightly below the surface of the countertop.
Here, on the front of the countertop, the edge will fall. It is easily glued with an iron.
The countertop returns to its former place and is opened by three layers of varnish. This is plywood plywood. It’s time to insert a T-shaped guide.
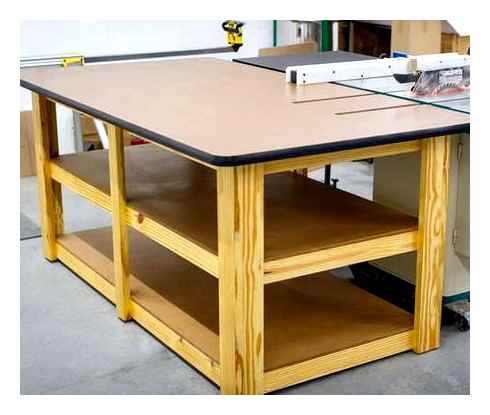
On the previous version of the table, the countertop did not protrude so much beyond its edges. It turned out a fairly wide plumb line so that the countertop practically rested on the end machine. Some restrictions arose. In particular, when turning a saw of 45 degrees, its distant edge began to rest against the countertop.
David just makes a small neckline and the problem is solved. Now the saw takes a full 50 degrees. Further, the author begins the manufacture of restrictive blocks. For them, hazel wood is used. A deep groove is made in the middle of each block.
Such guides of the bars are inserted into the slots, which should “sit” into the groove of the T-shaped path, like wheels in a rut. Such a device of restrictive blocks will allow them to be stable at right angles to the saw disc. These small planks are glued inside the grooves.
Next, David dries in each block a hole for clamping screws.
So, the bolt head is inserted into the rut, a wooden block is planted on it, which is pressed to the path using such a lamb handle.
At the end, the author on the sides of restrictive blocks removes small chamfers at an angle of 45 degrees.
Surfaces are polished with sandpaper, and blocks are covered with several layers of varnish.
Take a look at how it works. Everything is fixed conveniently and reliably!
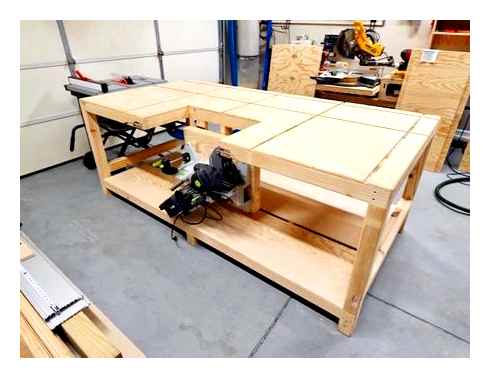
Since there is no stop, a lot of place is released. So, here, along the wall at the edge of the table, the master intends to make several lockers with boxes, where all kinds of tools and hardware will be stored.
I thank the author for the simple but useful improvement of the workshop for the workshop!
Good mood, good luck, and interesting ideas!
This post may contain affiliate links. This means that I earn a small commission for links used without any additional costs for you. See additional information in my confidentiality policy.

Assembly of the product
The assembly of the entire product is recommended to start by studying the drawings and all the parts necessary for assembling. It is also necessary to check the presence of a locksmith tool, without which it will be impossible to assemble the table
take into account the order of assembly of each of the nodes. The description of these nodes is given below.
We begin to make a table for a end saw from the assembly of the base or platform, on which the tool itself will be installed directly. The dimensions of this plate are largely dependent on the size of the end saw itself. over, if we want to make a universal table, so that it is possible to install other compatible tools, for example, such as a fucking machine, then the size is taken by the maximum size of the tool.
It is better to use 19 mm plywood as a material, in the absence of one, you can use a wood-steering plate or wood-fiber slab of a suitable size, but plywood is more reliable.
Installation of lateral extensions. Quite often, details of much longer length are used than a saw for a saw and for the processing of such parts, removable lateral extensions are installed. over, you can use those as on the right and left of the bed. Extensions are usually made of the same material as the bed itself. That is, 19 mm plywood will be quite enough. Upper shelves: an important table of the table. In order for the detail to be freely attached to the expansion, as well as for a more comfortable attachment of the expansion itself to the bed, it is necessary to make the upper shelves. They are attached with screws both the bed and expansion. Shelves are also usually made of 19 mm plywood
An important feature of the shelf is the presence of a spont along the entire length of the part, a width of 19 mm and a depth of 3 mm. His appointment will be explained later. The use of clamping plates
Clamping plates allow you to most accurately and reliably level the bed and expansion in width. To do this, it is best to use clamps that are pulled together by extensions and the basis of the table. After such an expansion fixation, you can fix it to the base of the table. Joint work of machine tools. When working together, several machines, as mentioned earlier, it is necessary to align their planes. If, for example, you want to use a fucking machine together with the end saw, then it must be installed so that the working planes of both machines coincide. So it will be necessary to leve the heights of both machines. It is they who are inserted into the shpuntes made in the shelves installed on the extensions. Mobile stops are also important. Mobile stops are designed to fix parts using guide rails made of solid wood bars. The quality of the end of the parts also largely depends on the quality of their manufacture. How else can you use extensions? Expansion allow you to fix parts of a fairly large length. In order to use them correctly, you need to reconfigure the table for such a detail. Of course, this will take a certain time, but then it will pay off in the manufacture of a large number of long measures.
So, we will summarize: you can make a table for the end stove even in a home workshop. At the same time, the result of the manufacture of parts on this table will be much better than on an ordinary workbench.
- Dimensional dimensions, mm: width. 1222 (3073 with fully extended extensions); depth. 508; Height. 165.
- Weight about 26 kg.
- Necessary materials: one plywood sheet 19 x 1220 x 2440 mm; one maple board 19x140x2440 mm; Four galvanized pipes 3/4 inch 1085 mm each.
- Fast assembly using screws and glue.
Why do you need a end workbench?
I made such a table to myself to cut the boards smoothly and purely. I initially chose a saw and looked at the stationary disk units. The depth drank to 80 mm and the angle of inclination more than 45 degrees captivated me. Of course, there are easier models that are limited to 40 mm cut into the depths and turning no more than 45 degrees. Gradation of is great: from unrealistically expensive to cheap. However, there is another type of circulars who know how to end. This is manual disk saws with a rectangular base. Only for them you need lateral emphasis. A metal paw is already sold in the kit. But its functionality is limited by small sizes. Therefore, for a separate saw, its external lateral emphasis is invented, according to which the base of the hand saw slides slides. The advantage of a layout on the face is a clean and even saw at almost any angle. The versatility is that the circular can work not only on a workbench, but also on weight when sawing shields. There is a restriction in the depths of the sawdown, which depends on the specific model. I have it 70 mm.
- Small half a meter. Benches for crafts end with them. The lateral emphasis, which is often combined with a stall for a manual saw, is suitable for small circulars.
- The average table size starts from half a meter in length and from one and a half width. It is equipped with a wooden emphasis for a medium.sized manual disk saw.
- Large workbags are designed for ending furniture shields. The length and width starts from two meters. Such tables are equipped with metal stops on bearings.And then the flight of imagination begins. After all, if everything is clear with the dimensions of the countertops, then the devices of the stop are different:
- Simple wooden of four elements: two legs, platform, side ledge.
- Metal from cooked corners.
- On bearings, the number of which from four or more.
- On rod guides.
My design for ending
First of all, I figured out the project in my mind. I wanted him to be very simple to implement. It’s good that I just bought a disk saw. This is Parma 200d. Although it can be equipped with a disc 210 mm. What did I do later. But I’ll be back to the project. Four legs are interconnected by the lower and upper bandage from the sides, and the countertop from above. After the ending device is mounted. That’s the whole project. I used little roulette, but often used a square, a pencil, a manual saw.one. I sawed four legs with a hand.saw at a right angle. An important point. He picked up a height for himself, namely, to the width of the palm above the waist.2. Drawn a rectangle on the countertop (on the lower plane), within which the legs are placed in the corners. The indentation is necessarily needed so as not to be stuck when working with your feet.3. I calculated the size of the binding, applying the appropriate blanks.four. With a strapping did not begin to wise. It turned out four long boards and four short boards. After sawing the elements, I started assembly.5. Using the square and two clamps, mounted the lower and upper binding on one side.
On the ground he leveled a place under the legs, putting two wide boards under them.eight. Then connected the two sides with the side short boards.
On the bottom of the countertop, the landmarks were preserved, according to which it leveled and fastened with the base.ten. Then I mounted a shelling device, having previously glued a window block on the wall from the box, having drank two racks.I wanted the saw disk to delve into the countertop 3 mm no more. Since the depth drank my circular of 70 mm, experimentally determined that it was necessary to put a couple of pieces of wood.fiber slab. The height of the lateral stop was 67 mm.