When to buy a dryer for your compressor?
The dryer is a part of the first necessity for compressors, which are part of the complex mechanism of pneumatic tools. It is extremely important that such devices are supplied with perfectly clean air, free of dust and fine particles.
Large devices have a display and mode control unit
This design removes excess moisture particles which condense as a result of water vapor condensation. Liquid droplets appear on the receiver as well as inside the air system. This phenomenon occurs when the air is compressed too intensively. In addition, compressed air can also have oil particles. They appear as a result of using reciprocating compressors that use a grease-like consistency for lubrication.
Products with built-in dehumidifiers must not be used in the vicinity of heating appliances
Without the installation of a dehumidification mechanism with the air system, some problems may arise. Therefore, such mechanisms are installed for the following purposes:
- To prevent a drop in pressure in the system;
- prevention of the appearance of rust;
- removal of harmful microorganisms;
- elimination of failure of pneumatic substations.
Besides this, regular cleaning of heating systems in boiler-houses is performed with the help of dehumidifiers.
In a cold desiccant dryer all condensation is removed by freezing
Reasons for condensation in the compressor
The degree of humidity in atmospheric air increases as its temperature rises. For example, at a temperature of 10°C, at 0 bar atmospheric pressure, 1m3 contains 9,356g of moisture, at 20°C (77°F). 1g3 of moisture. 17,148 г.
The table shows the maximum air humidity at 0 bar, depending on the air temperature.
When air is compressed in a compressor, its temperature rises to about 180 °C. The lowering of the temperature in the compressed air system, the beginning of condensation in the compressed air chambers. Mixed with foreign impurities (compressor lubricant) air forms:
- Aggressive emulsions are mixtures of water and oil which cannot be separated by gravity;
- Dispersed mixtures. an aerosol mixture of water condensate and oil.
The condensation process begins when the concentration of moisture with foreign impurities (unable to compress like air) exceeds the dew point. The amount of moisture will precipitate more when the temperature of the incoming gas is high. Further movement along the line cools the mixture, provoking condensation.
Moisture entering a pneumatic system causes internal components to corrode, rendering equipment unusable. In winter, in conditions of low temperatures, moisture freezes, destroying valves, seals and other internal parts, units and assemblies. Air dryers used for compressed air preparation are a prerequisite for preserving the integrity of pneumatic systems.
Dehumidifiers separate air and moisture before the mixture enters the operating equipment. Dehumidifiers come in several types:
Condensation in the dehumidifier precipitates when the air cools to a value below the dew-point.
Dew point of compressed air
Moisture is one of the decisive parameters when choosing compressor equipment. Excessive atmospheric moisture can lead to process failures, corrosion, breakdowns. manufacturer specifies its maximum values in the passport of such machines.
Humidity is a value of the volume of water vapor in the gas. Air humidity is characterized by the following parameters:
- Absolute humidity (g/m3 ). Indicates the amount of moisture in a unit volume of air;
- Relative humidity (%). ratio of actual humidity to its maximum value (value of saturation of gas with moisture vapor). Indicates the amount of moisture missing for condensation. Dependent on temperature, pressure;
- The dew point is the temperature required for condensation to begin. Shows the actual amount of moisture in the air at a certain temperature.
The amount of moisture in the air at a constant temperature is constant. For this reason the actual dew point of compressed compressed air in a compressed air system is constant. the most convenient, practically important parameter. e.g. the moisture content in 1 m³ of air at t = 20 °C is approximately 17.15 g.
In pneumatic systems, a dew point of 3 is most commonly used.20.40.70 °C.
Dew point (under pressure) at the compressor
A distinction is made between two different characteristics of air humidity:
- Atmospheric dew point, ° CtrA. denoted by PD. This is the minimum temperature of chilled atmospheric air without condensation;
- Dew-point of pressurized air, °C rd is referred to as PDP. This is the minimum temperature at which compressed air can cool down without condensation. The value of its temperature decreases as the pressure decreases.
The compressed air dew point indicates the condensate threshold, which is undesirable for the equipment. This is the value used to monitor pneumatic systems.
The difference between these two values and the dependence of the dew point of compressed air on temperature can be seen in the example. A cube containing 1m3 of air at t = 20°C. Relative humidity 20%. Moisture amount in this case. 3 g. The maximum value of moisture in this volume can be as much as 15 g.
- The pressure in the cube does not change. 1 bar. The air is cooled. At temperature t =.3.2°C, 3g of water condenses out of it, t.к. the ability to hold moisture decreases as it cools (tabular value of moisture content at.3 g/m 3 )3.2° Ctr is the value of the atmospheric dew point, t.к. the process took place under atmospheric conditions;
- Volume of the cube decreases by a factor of 3 when the pressure increases to 3 bar. the mass of water vapor remains unchanged. 3 g (no moisture was let in or let out). Absolute humidity has reached the value 9g/m 3 = 3g/(1/3 m 3 ). The temperature does not change (20°C). the maximum amount of moisture is about 15 g/m3. Relative humidity of such air is 60% (9/15).
Consequently, from the initial cube volume, the air has increased relative humidity by a factor of 3.
Further cooling of this closed volume would result in a pressure dew point of no longer.3.2°C, and at 12°Ctd. Thus, the dew point temperature of compressed air increases with increasing pressure. The air at the compressor outlet needs to be cooled much less to saturate it. condensation.
Why do you need a dryer in a compressor?
Nowadays compressor equipment is in ubiquitous use: in household appliances, automobiles, industrial equipment, etc.д. But a compressor does not mean the single cylinder of compressed air that most people imagine. A compressor is a combination of devices.
How to choose the right compressed air dryer.
A compressed air dryer is equipment that removes condensate (moisture) from the pneumatic line, thus avoiding rust, corrosion and extending the service life of pneumatic tools. It does so by maintaining low humidity in the air, either by cooling or through adsorption. Dehumidifiers are differentiated according to their operating principle:
- Refrigeration dryer. It works according to the refrigerator principle by cooling the air to a dew point temperature (about 3C). It is an economical option that does not require a high investment of money and saves on maintenance of this equipment.
- Desiccant dryer. Has an adsorbent that absorbs water vapor in the compressed air, then the moisture is removed by subsequent purging or heating. Achievable dew point:.40C or.70C depending on the adsorbent used.
- A membrane dryer has a membrane in its housing that retains moisture. Membranes can be in the form of thin tubes or fibres through which compressed air flows and the moisture is separated. As a rule, a membrane dryer can reduce pressure dew point temperatures to a stable level and achieve values between refrigeration dryers (3C) and adsorption dryers (-2070C). A diaphragm compressed air dryer has no parts and materials that need to be replaced. The temperature to which the compressed air needs to be cooled before it begins to condense and the inlet air pressure.
Selection of a membrane dryer is definitely best left to an expert knowledgeable in compressed air drying technology. However, if such expert is unavailable, it is necessary to understand the following procedure when choosing a dryer.
So, the first thing to do is to determine the basic parameters of a dehumidifier.
The main parameters for selecting a dehumidifier are:
- the capacity of the existing compressor;
- Inlet air pressure;
- ambient temperature;
- Exhaust air temperature (piston compressors usually have 40 or 45C);
- Dew point at a given pressure. Dew point temperature to which compressed air must be cooled before it begins to condense. In order to choose the optimal dryer model, it is necessary to divide the required capacity by correction factors (operating pressure, ambient temperature, inlet air temperature, dew point). These coefficients are usually found in the manufacturer’s correction tables. Let’s take Remeza RFD series (refrigeration type) dryers as an example.
Let’s assume that we need to choose a dryer for our compressor where we know dryer’s rated efficiency (according to the technical datasheet) which is why we need to calculate its maximal efficiency.
Remeza RFD series dehumidifiers have the following correction factors:
Correction factor to correct capacity based on inlet pressure (bar g ) 0.87.)
Correction factor to correct capacity based on inlet pressure (in bar g.) | ||||||||||||
Bar (gauge.) | 3 | 4 | 5 | 6 | 7 | 8 | 9 | 10 | 11 | 12 | 13 | 14 |
Factor | 0,79 | 0,87 | 0,92 | 0,96 | 1,00 | 1,03 | 1,07 | 1,10 | 1,13 | 1,16 | 1,18 | 1,21 |
How Desiccant Dehumidifiers Work and their Benefits compared to Compressor Dehumidifiers
Correction factor correcting capacity by inlet flow temperature (C)
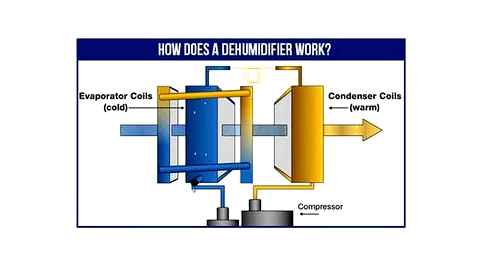
Correction factor correcting capacity by inlet flow temperature (C) | ||||||||||||
C | 35 | 40 | 45 | 50 | 55 | |||||||
Coefficient | 1,00 | 0,84 | 0,71 | 0,63 | 0,55 |
Correction factor correcting performance for ambient temperature (C)
Correction factor correcting performance for ambient temperature (C) | ||||||||||||
C | 25 | 30 | 35 | 40 | 45 | |||||||
Coefficient | 1,00 | 1,00 | 1,00 | 1,00 | 1,00 |
In order to determine the actual capacity of the dehumidifier, the following formula must be used:
An RFD81 dryer is rated at 1330 l/min (design capacity). The maximum capacity (air flow rate) must be determined under the following operating conditions:
- Air outlet pressure = 8 bar
- Ambient temp. Medium = 40 C
- Rate. 1.00 Ambient air temperature at inlet = 45 C
- Dew point at this pressure = 3°C
For each operating parameter there is a corresponding numerical coefficient, by multiplying by which the nominal design capacity, we get the following value:
In the calculation we obtain: 1150,7 l/min.
This is value of maximum productivity (air consumption) that a dehumidifier is able to provide under the above working conditions.
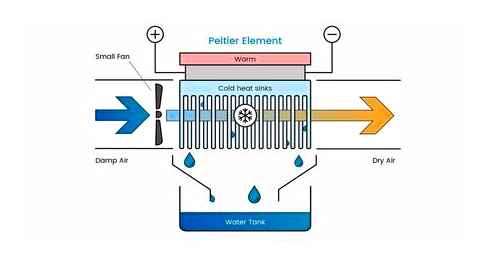
In the next step, we need to determine the dryer model for specific operating conditions. To do this we use the following formula:
- Required capacity = 1100 l/min.
- Air outlet pressure = 8 bar
- Ambient temp. medium = 40 C
- Rate. Inlet air temperature = 45 C
- Dew point at this pressure = 3 C
In order to choose the right dehumidifier model, you need to divide the necessary productivity by the correction factors corresponding to the specified parameters:
In our calculation we obtain: 1,271 l/min.
Thus, taking into consideration specific operation conditions we will be fully satisfied with RFD81 model whose nominal (according to the passport) air capacity is 1330 l/min.
In conclusion it is necessary to note that while selecting dehumidifier models of other producers one should take into account the tables with correction factors of these producers. As they may differ from the values given in this publication.
Purpose
Used to remove moisture from the compressed air flow to the compressor. Applications:
- mechanical engineering;
- medicine;
- pharmaceuticals;
- food production;
- metallurgical industry;
- Painting, sand blasting;
- forming stage of production;
- Power supply for pneumatic appliances.
Devices used to dry the air flow:
- Different types of dehumidifying equipment;
- end chillers;
- separators;
- receivers;
- filters dryers;
- preparation units for purification.
Wiring diagrams for this equipment:
- centralized (one unit connected to several compressors. Economical option, disadvantage: in case of breakdown, all compressors are deprived of the dried air stream);
- Decentralized (each compressor has its own type of device-dryer, which meets individual requirements. expensive option).
Compressor dryers what they are and why they are needed
Compressor equipment is widely used in many applications. It is used in industry, science and medicine. Compressors may be of different designs, but they are all needed to produce compressed air.
A device called a compressor dehumidifier allows you to get rid of excess moisture in compressed air. As a result, compressor life is increased and there are no water particles in the discharged air.
Types of dehumidifiers
There are several types of dehumidifiers that are used for domestic and industrial purposes. Before you buy, you need to define your objectives and compare them with the technical specifications to choose the best type of dehumidifier. Among the large and varied selection you can find:
The features of the latter type of device is the effective purification of water, solid elements and oil. They are installed on oil compressors, which can intensively process parts by means of a lubricant. Large production facilities with high throughputs often use modular filter systems as well.
The water separator is a functional and important component, but it does not function as an independent operating filter.
The modular system is controlled by a controller that issues various commands not only to the filter, but also to other components in the unit.
Selection criteria
Depending on the application, the cleaning requirements also change. If a surface needs to be painted with an air gun, but attention must be paid to the small filter capacity. Preferably a fine filtration.
During the production process, there may be minimal demands on the quality of the filtration. But in this case, special attention is paid to the volume of output. Experts recommend to look at the list of foreign particles which are collected by the filter. Moisture and oil separator for a compressor, which processes particles of water and oil from the air flow is the best solution.
If the operation requires a filter to collect excess moisture, dehumidifiers can also be purchased. But they do not guarantee high quality getting rid of different fractions, particles and foreign bodies.
Types of air purification systems
The following types of filters are used to clean the air flow to the compressor:
Each type of compressed air purification devices from moisture has a set of its own advantages and disadvantages. To choose the best device it is desirable to have an idea about their work schemes. At the same time there are cleaning systems that can be used for both domestic and industrial purposes.
Those masters who do not have enough time to assemble with their own hands, prefer to buy an air dryer for compressors in specialized companies.
Negative factors of moisture in the pneumatic system.
When planning a drying system for your production you may use the following standards: International Standard DIN ISO 8573-1 specifies 6 classes of air cleanliness and maximum permissible levels of various impurities, including humidity, corresponding to each class.
Maximum residual oil, mg/m3
Maximum residual particulate matter
Maximum residual moisture
There is a similar Russian GOST 17433-80. When selecting the right equipment, the permissible levels of air impurities and moisture in the respective equipment must be observed.
Alien impurities, mg/m GOST 17433-80 (ST ST SEV 1704-79) Industrial cleanliness. Compressed air. classes of contamination (with Amendment N 1), not more than
the temperature of the air is 293,15 K (20 C) and the pressure is 1013,25 hPa (760 mm Hg).st.).
The size of the solids is determined by the largest measured value.