Welding and soldering band saws: how to do it right with your own hands?
Saws are commonly used in the woodworking industry, and their main feature is their continuous cutting surface. It’s a ring of band with metal teeth.
Welding band saws is at the heart of their construction, because they are made by joining a previously prepared band into a ring. This process is also used in their repair. This article will talk about the main features of welding such devices.
General information
At first glance, welding and soldering band saws for wood or metal does not seem like such a difficult task. Simple and uncomplicated operation. This is indeed true, but there are nuances. You have to take into account that band saws are under a lot of stress during operation. These loads constantly stretch and bend the saw. And if the saw successfully copes, the welded joint may not be able to withstand these loads. And it’s just a question of the quality of the work. In order for the seam to withstand all loads, it needs to be as strong as the saw itself.
How to achieve a quality joint? Of course, using a special welding machine. To achieve a strong, unbreakable seam, you can use the technology of contact butt welding. But at the same time to use a special machine for band saw welding. Let’s talk more about this.
Band Saw with my own hands
Homemade band saw, made with their own hands: a detailed description of making a homemade with photos and video.
Hello all! Here you need a band saw for a home workshop, decided to make their own hands.
In the presence of the electric motor for 300 watts, I decided to use it for his homemade.
We will also use the tape. 1830 x 16 mm. Let’s make the drive wheels from plywood.
These are the blanks for the drive wheels.
I welded a frame from a corner, installed the motor, drive wheels, made the belt drive.
To keep the saw steady while sawing I put thrust bearings on it. The assembly consists of three bearings and two angles. I made the holes oval to regulate the gap between them and the band. Two such assemblies are made, the second one is placed under the table.
Pull out bar, consisting of two welded angles and inserted profile tube. It is fixed by bolt through the welded nut. The boom housing is bolted to the horizontal bracket and is movable for adjustment.
From a profile pipe made the frame of the table, on the frame will be bolted sheet wood chipboard.
Installed the belt guard on the opposite side from the cut, and a box on the upper wheel.
The result is this homemade band saw for the home workshop. Saws very well and quickly, I am fully satisfied with the home-made device.
Saw blade features
The mechanical saw can be used to make the blade, in almost any condition. Even if it has deteriorated and rusted, it will still be suitable for homemade. Advantages of the product is enough:
- The knife will be made for yourself, so it will be unique and will fit well in your hand;
- a wide choice of material, both in length and in width of the shank;
- It does not need to be hardened;
- Several knives are realistic to make from one blade;
- such blade will be in the price category of 100 and above, better than the “chinese thing” for 30-40.
This is really. Spending not very much time, depends on experience, you literally for pennies get the product with good cutting properties. Don’t overheat it while you’re making it, and you’ll have a great knife.
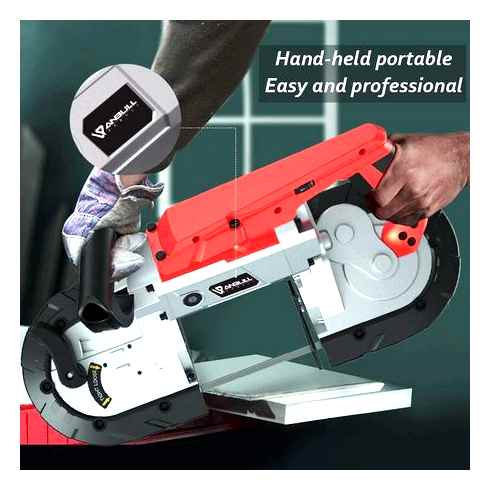
necessary tools and materials
Since there is no need to forge and harden the future blade, all tools can be found in the garage, which at least a little bit, but equipped with. We will need:
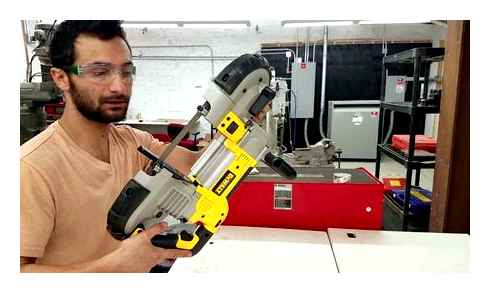
- markers: black and silver;
- Ruler, a piece of paper and a caliper;
- angle grinder (angle grinder);
- files with different grains;
- as well as sandpaper and masking tape;
- epoxy glue;
- a sharpening and drilling machine;
- a container of water for cooling;
- a hammer, a core and a vise.
In this kit, everything is great, for one simple reason. any item can be replaced with its like. A drill press is cool, of course, but an electric drill will suffice, too. And so with any of the tools on the list. You will need materials for making the handle, but about this a little further.
Absolutely any tool must be able to choose, to know the basic aspects in the choice, to have at least some idea of working with tools.
Even at home, you can look at photos of different metal hacksaws and see which one is needed for your needs.
Tools and materials needed
Since forging and hardening the future blade is not necessary, all the tools can be found in the garage, which at least a little, but equipped. We will need:
- Markers: black and silver;
- A ruler, a piece of paper and a caliper;
- angle grinder (angle grinder);
- files with different grains;
- as well as sandpaper and masking tape;
- epoxy glue;
- a sharpening and drilling machine;
- A container of water, for cooling;
- a hammer, a punch, and a vise.
In this kit, everything is great, for one simple reason. any item can be replaced with a similar. A drill press is cool, but an electric drill is enough. And so with any of the tools on the list. You will need materials for making the handle, but more about that later.
Absolutely any tool must be able to choose, to know the main aspects in the choice, to have at least some idea of how to work with the tool.
Even while at home, you can take a look at the photos of different hacksaws for metal and understand which one is required exactly for your needs.
How to make a knife from a mechsaw with your own hands
Mechsaw thickness is usually 2-2.5 mm, if you do not find another option. This is quite enough for all knife tasks. They are light in the hand, hold a long sharpening time and will be completely legal. Do not miss the length. And as for the other qualities, the knife will not fall under the article on edged weapons.
Making the knife
This process can be conditionally divided into several stages. For a detailed and clear description, we will do so:
- Of course the first thing. the layout-drawing. If you do not have enough experience, do not disregard this point, it is really important. Measure the “saw” workpiece itself, the layout should not protrude over the edges, and do not forget about the shank and handle. All these points should be taken into account from the beginning.
- Draw the sketch on the piece of saw with a black marker. We clamp it in a vice and cut off a piece of required length with an angle grinder. At the same stage cut the shank, so you will not have to return to the vice and “angle grinder” anymore. After roughing, “remove” all burrs with a file.
- Particular attention is paid to the future descents. This process is the most important and it must be taken seriously. We take almost a “blade” and paint it with a black marker, then for marking we use a caliper. Measure the chamfer in accordance with the model. Then carefully and, most importantly, symmetrically draw a strip along the blade, using a caliper. The scratched stripe should be marked on the black paint. Do the same on the other side. Be sure to trace the marking with a silver marker, preferably with aluminum powder.
- To draw the chamfer it is better to use a special device, for details see the article: “How to draw the chamfer on the knife”. This will be much faster and most importantly. more accurate. And now about the marker with aluminum dust, when you work on the grinder, the workpiece will be warm. A simple one will trivially “burn out”, but the one described above, on the contrary, will solidify and will not fall off. Thanks to such a small trick, the chamfer will be perfect. You don’t need very fine grit size on the grinder, the one P80 and P120 is enough. You may get it to perfection later, but this is a rough cut.
- Begin to make the grooves from the handle, and after you have finished one side, you do the same on the other one. After making sure everything is OK, we can go over it with a felt wheel with paste. Then you should wrap the blade several times with painter’s tape. it is both protection from cut and preparation for work with the handle.
- The handle will be made of wood with symmetric pads. Drill holes in the shank. We mark the bar and divide it exactly in two parts. According to the holes on the blade, we drill them on the plates. Then we need to saw along the handle, according to the shank. After measuring and testing, let’s start with the shape of the handle, here you can follow your taste only. Read more in the article: “How to make a handle for a knife”.
- When the parts are ready, they can be riveted together. Knife almost done, now only need to work the handle in hot wax. If you do not have one, natural oils, latex-based compounds, silicone or special wood impregnation can be used.
Types of band saws
Bandsaw machines can be of the following types:
- Cantilever machines. Their design includes raised and lowered saw frame (console), as well as the base frame. Designed for cutting small parts.
- Column type machines. Can be one-column (single-column) or two-column (double-column). In the first one, the frame moves on one column, and medium-sized workpieces are usually cut at different angles. The second variant has a frame that moves on two columns, which allows to work with difficult materials.
- Gantry-type machines. The models differ in the presence of a static working table, along which the saw frame moves. Intended for cutting hard-to-machine large-size workpieces.
- Vertical frame saws. Their saw frame is vertical and stationary. A distinction is made between manual machines, where the part is manually fixed on the table, and models with a sliding saw frame. The second variant is used for cutting large boards.
- Horizontal bandsaws.In their design, the saw frame is in a horizontal position. Can produce not only straight but also diagonal cuts. Designed for cutting large-sized workpieces.
Also, depending on the level of automation, a distinction is made between manual, semi-automatic and automatic.
Instructions for band saws
There are certain things to keep in mind when working on band saws:
- Before the performance of operations the operator sets the parameters on the machine by the angle of inclination, depth and length of cut, place of the operation, speed of movement and blade tension.
- For each type of material to be machined a specific blade is selected, which differs both in design of cutting elements (teeth) and material of their manufacture.
- Large-size bandsaws are placed on the floor on a solid support, while small-size models can be installed on a table, workbench or on a special stand.
- Blades that periodically need to be replaced are sold coiled. When installed on the machine, the band of the right size is soldered into a ring and the welded seam on it is ground.
- It is worth taking into account that you can cut faster with a thin blade, but a thicker blade is less likely to tear.
- All work on the band saw systems must be carried out according to strict safety regulations and the operator must be familiar with the process.
Bandsaw Operating Instructions
When working on band saws certain things must be kept in mind:
- Before each operation the operator sets on the machine parameters for slant angle, depth and length of cut, place of operation, band speed and tension of the blade.
- For each type of material to be processed a specific blade is selected, which differs both in design of cutting elements (teeth) and in material of their manufacture.
- Large machines are placed on the floor on a solid support, while small models can be installed on a table, workbench or on a special stand.
- Tape webs that periodically need to be replaced are sold coiled. When installed on the machine, the belt is welded into a ring and the weld seam is ground.
- It’s worth considering that you can saw faster with a thinner blade, but a thicker blade is less likely to tear.
- All works on band saw equipment must be executed in strict compliance with safety regulations, and the operator must be well versed in the technology of the production process.
Degrees of automation
Manual metal band saws are similar to cantilever band saws in design and operating mechanism. The band saw blade in this class of bandsaws is moved by the physical effort of the operator or by the weight of the frame itself. Their advantages:
- Reasonably low cost of the machine itself and its operation and maintenance.
- In most cases cutting can be done at an angle of up to sixty degrees.
- The manual way of lowering the saw frame causes vibration of the saw during operation, which reduces the service life of the machine.
- In most cases there is no visual control of the degree of tension of the saw itself and the mechanisms responsible for cleaning the working platform.
- When working manually, it is necessary to periodically adjust the saw blade drive pulleys.
Most often these manual devices for cutting metal on band saws are used by small industrial industries.
Semi-automatic bandsaws for metal, in which mechanisms are actuated by a hydraulic drive. From manual operation the operator has only to feed the workpiece.
Working with a workpiece in a semi-automatic machine is done in this way:
- After starting the band saw, the workpiece is held in place automatically.
- A specific cutting speed and pressure is ensured by a hydraulic cylinder.
- Lifting of saw blade after achievement of the bottom cutting point is automatic.
Automatic machines are used especially in large companies for cutting large numbers of workpieces. The main advantage of this device is that no physical effort is required. the operator only has to put the workpiece in a vice and set the required parameters for machining.
If the need arises, these band saws can easily be converted to manual operation.
Design and assembly of the band saw
The unit for sawing various materials can be made by yourself, the band saws work perfectly in the workshops. With your own hands you can assemble the saw with the least effort and provide for all the subtleties of work.
Band saw type woodcutting machines have a working table at the base, with working and additional elements on it, a circular motion feeds the cutting blade, supported by two wheels. Sufficient space is required for the construction and installation of a complete unit, because the equipment, together with the feed line, has large dimensions.
You can make with your own hands a portable table setting for manual sawing, but in the small space of the workshop you can not dissect the logs into boards.
Design of the frame
Hard wood is chosen for the base to avoid vibration. The surface of the work table can be made of thick plywood, and the side ribs can be edged with slats or metal. The supporting bar is made in the form of a beam. A schematic drawing is made beforehand, in which the dimensions of the parts depend on the horizontal dimensions and height of the hall. Specified in advance the height of the frame, the diameter of the pulleys and the length of the rods. It is possible to perform an accurate detail drawing, which is more convenient for assembly.
The height of the work table is designed to be a comfortable height, with space for the drive pulley and bottom pulley, the swarf waste and the motor itself. The table can be any shape, but often the bed is made in the form of a pedestal with closed sides, at the same time serving for the accumulation of chips. Easy opening for easy cleaning.
the worktop is placed directly on the frame. Sometimes the height of the lower bed is not sufficient, in which case a solid extension is added to raise the worktop surface to the required height.
Setting the boom and pulleys
The support rod is made of a bar profile with a cross section of not less than 8 × 8 centimeters. To him on his side, taken as a conventional back surface, attach two supports, which will be located pulleys (wheels). The supports are made of strong material, laminated plywood with a solid core is acceptable. Choose the distance between the wheels so that the log to be sawed passed through with a reserve on the sides.
The diameter of the pulleys is chosen arbitrarily, an increase in the index leads to better performance. There is an unspoken rule for selection, according to which the ratio of the cutting blade to the diameter of the pulley is 1/1000. For example, for a 4 mm wide band, the diameter of the wheel must be 400 mm.
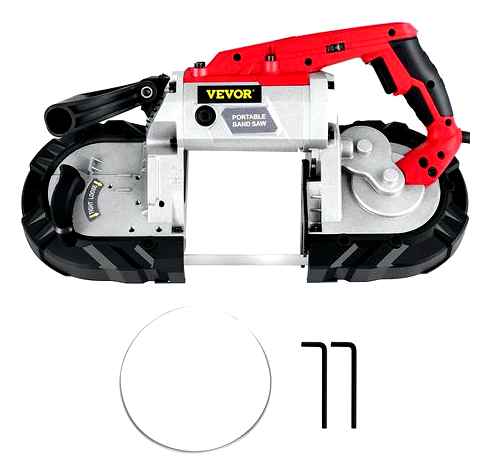
Diameter of the belt drive tension wheel is chosen according to the length of the cutting belt, the diameter of the main pulleys and the number of engine revolutions.
The pulleys are made with a slightly convex belt edge, about 5-10˚, which helps prevent the belt from running to the side and falling off. A shallow groove is provided on the drive pulley to locate the belt there. Usually bicycle inner tubes are used for sheathing the pulley, the rubber of which prevents the belt from coming off.
Locate the upper pulley on the block moving horizontally to select the belt tension. This requires a lifting mechanism, a simple version of which is a bar connected by a spring to the lever and located under the block. The lever is fastened with several screws at different levels, and a spring provides the necessary pressure.
The lower pulley is made up of two wheels (drive and idler) arranged on an axle. It is important to balance the top and bottom pulley in the plane, to minimize the occurrence of “eighths”. The top pulley is conveniently mounted with self-centering bearings, firmly attached to the wheels. After completing this assembly step, test run the machine for a short period of time.
Installation of blade guides
To evenly saw the material and to prevent the band from being pressed through, guides are mounted on a narrow bar along the blunt end of the saw. A common variant of this device consists of three bearings on a bar, one of which is used to support the flat side of the blade, and the other two to support it from the sides. Sometimes wooden stoppers are used instead of bearings on the sides.
Align the rails at the reference point so that there is no vertical deflection at the opposite end, for convenience, the position of the beam is marked with the blade laid out in the tension.
Cutting band jointing process
Soldering in the workshop takes place as follows:
- the places at the joint of the web at both ends are ground, and a brass strip is placed between the surfaces;
- To make the strip, cut off a piece of brass (0,3-0,4 mm) according to the width of the saw blade, moisten and sprinkle with borax powder from both sides;
- pincer jaws are heated in an accessible way (gas burner or horn) to a bright red color, applied to the soldering point and pressed down;
- the strip is heated by the red-hot jaws, the brass melts and spreads, and the borax works as a flux that prevents the oxidation of the solder when heated;
- do not remove the pliers until the joint is completely cooled and the solder hardens, after removing them, moisten the soldering place with a wet sponge to harden it;
- inspect the joint, its hardness should correspond to the web;
- if the place of the joint is hard, the procedure of heating with tongs is repeated until the straw color of the solder, gradually cooled;
- soft solder requires another red-hot heating with pincers and sharper cooling;
- to prevent the pincer jaws from soldering to the saw blade in the process, a solution of chalk with liquid glass is applied to their contact surfaces;
- to install and tension on the lower and upper pulley uses a crank, check the correct location on the discs and rollers stop rotation, adjust the correctness of the passage;
- switch on the machine for a short time and make further adjustments, if necessary.
Band saw brazing
In the absence of a welding machine, the band of the saw blade is soldered. To do this, degrease it, heat the ends of the strip with a gas torch and do the following operations. apply flux and melt it with the same torch, connecting by diffusion with a piece of brass:
- We put a piece of brass on the end of the blade, melt it in the torch flame. when melted, the saw steel diffuses with the brass melt at the atomic level. We use borax or special flux PV209X as flux.
- Construct a special device, similar to the mobile and fixed clamps of the machine for welding saws.
- Secure the ends and apply flux to both ends.
- Align the ends of the band in the overlap by 2 teeth.
- Put a piece of brass between the blades and heat this place with a torch.
- As the melt develops, we join the strips together.
- Wait for the belt to cool down completely by itself.
- Grind joints to the point of “enough. it’s already flat”.
The melting point of brass is about 900 degrees. The halves are heated to this temperature. You can use silver solder with a melting point over 900 degrees instead of brass.
Fusion soldering is easier, but it is harder to machine the soldering point to the proper thickness. This method is only suitable if no special welding equipment can be used.
Quality control
Band saw welding with your own hands is finished. But in the absence of experience, you are sure to have visible defects. So carry out a visual quality check. Carefully inspect the weld to make sure there are no imperfections.The most common defects are displacement of edges, ejection of molten metal on the blade and no welding. Edges shift due to insufficient amperage. Reversal of molten metal if the current is too high. And non-punches are formed due to low pressure or low current.
Regardless of the type of welding saws is made by the same method.
How to make a bicycle
An old bicycle, which is no longer needed for direct use, will be perfect for making a band saw for wood yourself:
- The first step is to make a frame with your own hands. It can be constructed from inch pine, from layers of boards with overlapping, from strong sheets of plywood. The frame is traditionally made in the shape of the letter C, in the lower part two supports are mounted, connected with the base, and on top. the landing place for the guide mechanism with the wheel. You can make the frame not only from wood, but also from steel
- Next, a movable block of wheel fixation is assembled and installed in the upper part, which will move vertically. He will be responsible for tensioning the band saw blade. The block is a rectangular frame with a shaft holder for the upper moving wheel. The upper pulley should move in the vertical plane
- The next step is to install the pulleys on the structure. According to the classic model they are made by yourself, but if you use an old bicycle you can take prefabricated wheels and put them on. They are mounted on the shaft at the top and bottom and secured. Then the drive belt should be wrapped around the upper pulley and balanced. To do this, mount the bearings for the saw blade, secure the wheel so that it rotates with the lowering, and make small indentations in the bottom at the rear. Chambers are put on the pulleys, which will protect the construction from slipping of the cutting belt. A bicycle wheel is a prefabricated band saw pulley with a recess around the circumference
- Next it only remains to mount the wheels to the saw frame. Put a washer on the shaft and fasten it with a bolt. Then we do the same for the lower wheel. Align the complete unit with the ruler and put it into test operation, at first with minimum load. Pulleys must be placed in the same plane, otherwise the belt can not move evenly
If you have your own hands on the metal or wood ready, it will not work as smoothly as a purchased one, but it will be able to cut.