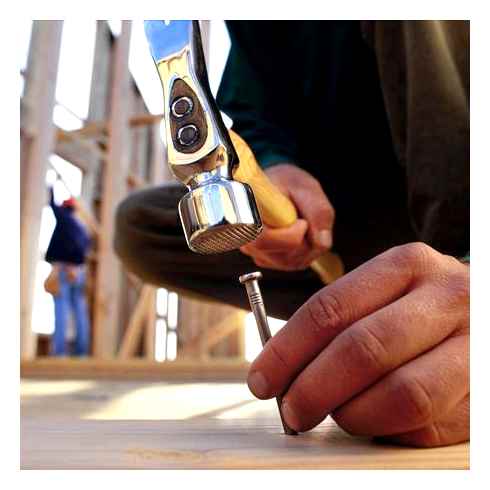
How to make a handle for a hammer. How to make a handle for a hammer with their own hands
How to attach a hammer?- Not everyone today knows how to do it properly. I confess that I myself have used whatever hammers I could get my hands on before. I didn’t have time to do everything properly, and I didn’t need a hammer that often. And now, in retirement, I have a lot of free time, I do some repairing all the time, that’s why I try to keep my tools in order. There are hammers on the market that have a handle made of metal or some synthetic materials and there is no need to put it on. But traditional hammers with wooden handles are still very popular. It’s not just that they are much cheaper. Wood. the material is light, and for a hammer, it is very important that the handle is light, but the “head” of the tool is heavy. Then the force of the blow will be much greater. Besides, every person has his or her own anthropometric peculiarities. Industrial hammers are for the average person and may be too big for a small person, but for a giant they are not. small. With selfmade wooden handle you can “adjust” the hammer to your hand: the thickness of the handle will be such that it is convenient to hold, and its length corresponds to the length of the master hand. A real craftsman’s tool is always in order. This rule is especially important when you have to work with this tool frequently. You can still hammer a couple of nails a year with a bad hammer, whose handle is all dried out and loose. But if a hammer is one of your most essential tools, it must be in perfect condition. With this simple tool, you can not only damage your finger if you miss the nail head or the butt of the chisel, but also cause serious injury to both the mechanic and those around him if his striking part suddenly “slips” off the handle. And it is not uncommon for a hammer to be on the wrong handle. I’ve looked through quite a few pictures of a hammer on the Internet, and I can’t find any where it looks like it’s properly tipped. (You can see very clearly in the photo what happens if the hammer is not placed correctly).
So here we are going to tell you how to put the hammer on the handle correctly. First of all, you have to keep in mind that not all wood is suitable for a hammer handle. What kind of wood is needed for the handle of the hammer?? Do not use wood that splits easily, such as spruce, pine, aspen, alder or similar. But an ordinary birch, not straight but twisted will do for this purpose. (By the way, according to GOST 231077 “Steel hammers for metalworkers”). It is allowed to make hammers handles from hornbeam, maple, mountain ash, dogwood, ash, oak, beech and birch of the 1st grade). So you can take not very thick birch branch (two or three times thicker than the handle itself) and from it cut blanks for handle of hammer. If the branch is taken from a “live” tree, the piece should be well dried. It is better to dry in the natural way, having put a few pieces at once somewhere in the shadow but in a well-ventilated place. In the countryside, it can be an ordinary pile of firewood, together with which the blanks for the handles will dry perfectly for about a month (in summer). In city conditions it is possible to put blanks for handles on the balcony. Do not dry the wood with any heating devices (for example, on the heating radiator), otherwise it may crack in the process. A great handle for a hammer can be made from a broken wooden hockey stick, which uses very strong and hard wood.Why is it so important that the wood, of which it is planned to make the handle of the hammer, should be dry?? It is very simple: when any wood dries, it decreases its size (water evaporates and naturally, the volume of the body decreases). But a hammer handle that has not dried out well enough will inevitably dry out over time and no matter what wedges you hammer into it, the head of the hammer will dangle on the handle and may eventually come off of it. What should be the shape of the handle of the hammer? The already mentioned GOST stipulates three different designs of the hammer handle (cf.It is not a problem to make other ergonomically correct handle shapes (see drawing), but it is stipulated there that it is allowed to make other ergonomically correct handle shapes. So, if you decided to make the handle yourself, you can take these options as a basis, or make according to your own design. The main thing is to make sure the handle is comfortable and does not slip out of your hand when hitting with the hammer.
When making the handle you should keep in mind that the blank for it should be at least 5 cm longer than necessary. It should taper smoothly toward the end where the hammer head sits.How to slide the hammer head onto the handle correctly? The hammer head hole on both “inputs” is slightly larger than in the middle. So, the size of the handle blank at the thinnest end should correspond to the size of the hole in the middle of the hammer head. Be sure to check how well the hole for the handle is made in the striker of the hammer. Take note of the
Home workshop
Nothing can be done at home with bare hands. In the blog it is told about what a domestic handyman should have, how to equip his workplace, and also tips on using various tools are given.
How to put a hammer on?– Not everybody knows how to do it right now. I’ll confess that I used to use whatever hammers I could get my hands on. There just wasn’t enough time to do everything properly, and the hammer wasn’t needed very often. But now, when I retire, I have a lot of free time, I do some repairing all the time, that’s why I try to keep my tools in order. There are hammers on sale, the handle of which is made of metal or some synthetic material, and there is no need to put it on. But traditional hammers with wooden handles are still very popular. It’s not just that they’re much cheaper. Wood. The material is light, and for a hammer it’s very important that the handle is light but the “head” of the tool is heavy. Then the impact force will be much greater. Besides, every person has his or her own anthropometric peculiarities. The industrial hammers are made for an average person and may be too big for a small person, but for a giant they are not. small. Using self-made wooden handle you can “adjust” the hammer to your hand: the thickness of the handle will be such that it is convenient to hold, and its length corresponds to the length of the master hand. A real craftsman’s tool is always in order. This rule is especially important when you have to work with this tool often. To hammer a couple of nails a year is also possible with a bad hammer, with a handle dried out and hanging around. But if a hammer is one of your most important tools, it must be in perfect condition. This simple tool can damage not only a finger in case of missing a nail head or chisel buttstock, but also cause serious injury to both the mason and those around him, if the striking part of the hammer “slips” off the handle. And it doesn’t happen so seldom if the hammer is not put on it correctly. I’ve looked through quite a few pictures of the hammer on the Internet, and I haven’t found one that shows that it is mounted properly.
(You can see on the photo what happens if the hammer is not placed on the handle correctly).
So here we will tell you how to put the hammer on the handle correctly. First of all you should keep in mind that not every wood is suitable for a handle of hammer. What kind of wood is necessary for a hammer handle?. Tree species with easily prickly wood such as spruce, pine, aspen, alder and the like should be definitely excluded from the list of those suitable for a hammer handle. But an ordinary birch tree, not straight but twisted, is quite suitable for this purpose. (By the way, according to GOST 231077 “Steel hammers for metalworkers”). It is allowed to make hammers handles from hornbeam, maple, mountain ash, dogwood, ash, oak, beech and birch of the 1st quality). That’s why you may take not so thick birch branch (two or three times thicker than the handle itself) and cut a blanks for hammer handle from it. If the branch is taken from a “living” tree, the piece should be well dried. It is best to dry in a natural way, putting several pieces at once somewhere in the shade, but in a well-ventilated place. In the countryside it can be a usual pile of firewood, together with which the blanks for the handles will perfectly dry in about a month (in summer). In urban conditions it is possible to put the blanks for the handles on the balcony. Do not dry the wood with any kind of heating device (for example, on a radiator), otherwise it may crack. An excellent handle for a hammer can be made from a broken wooden hockey stick, which uses very strong and hard wood. Why it is so important that the wood from which the hammer handle is to be made be dry? – It’s very simple: when drying any wood decreases in size (water evaporates and quite naturally, the body volume decreases). So a handle of a hammer which is not well dried will inevitably dry out in time and no matter what wedges you hammer into it the head of the hammer will dangle on the handle and in time it can come off. What shape a hammer handle should be?. mentioned above GOST standard stipulates three different designs of hammer handles (see “Gosstandart”).It is possible to produce other ergonomically correct handle shapes (see drawing), but it is also stipulated that it is possible to produce other ergonomic handle shapes. So, if you decided to make your own handle, you can take these options as a basis, or make your own design. The main thing is that the handle must be convenient and must not slip out of your hand when hitting with a hammer.
when making the handle it is necessary to take into account that the blanks for it should be longer than necessary, at least by 5 centimeters. It should taper gently toward the end where the hammer head fits. How to slide the head of the hammer properly onto the handle?. The hole in the head of the hammer on both “entrances” is slightly larger than in the middle. So the size of the handle blank at the thinnest end should correspond to the size of the hole in the middle of the hammer head. Be sure to check how well the hole for the handle is made in the hammerhead itself. Pay attention to
The process of adding a handle for the hammer
Do not forget that in order to attach the handle you need to use something heavy. For example, if you have an old pipe with no signs of rust on it. It can be simply hammered into the hole in the metal striker of the hammer. It’s also possible to use a welder and weld a pipe. it might be a hassle, but the handle will last forever. It is also possible to work the stick with a sharp knife and simply hammer it into the striker. All of these examples of replacing a broken hammer shaft show that it is easy to do quickly. But it doesn’t last very long!
There is also another way, which is to use a 250 ml bottle of soda, which, according to folk craftsmen on the Internet, you can also insert in place of the broken shaft of the hammer. If there was air in the bottle, this could be guaranteed even if the neck of the bottle went into the hammer. But with a cap the bottle is definitely not going to fit in the metal side of the hammer.
One can only wonder how craftsmen managed to make a shaft for a hammer from an ordinary bottle. And don’t forget the shaft also serves as a balance when you are using the hammer and an empty bottle certainly can’t be a balance. If you could seal the end of the bottle with something, you could fill it with, say, sand before inserting it in the hammer striker.
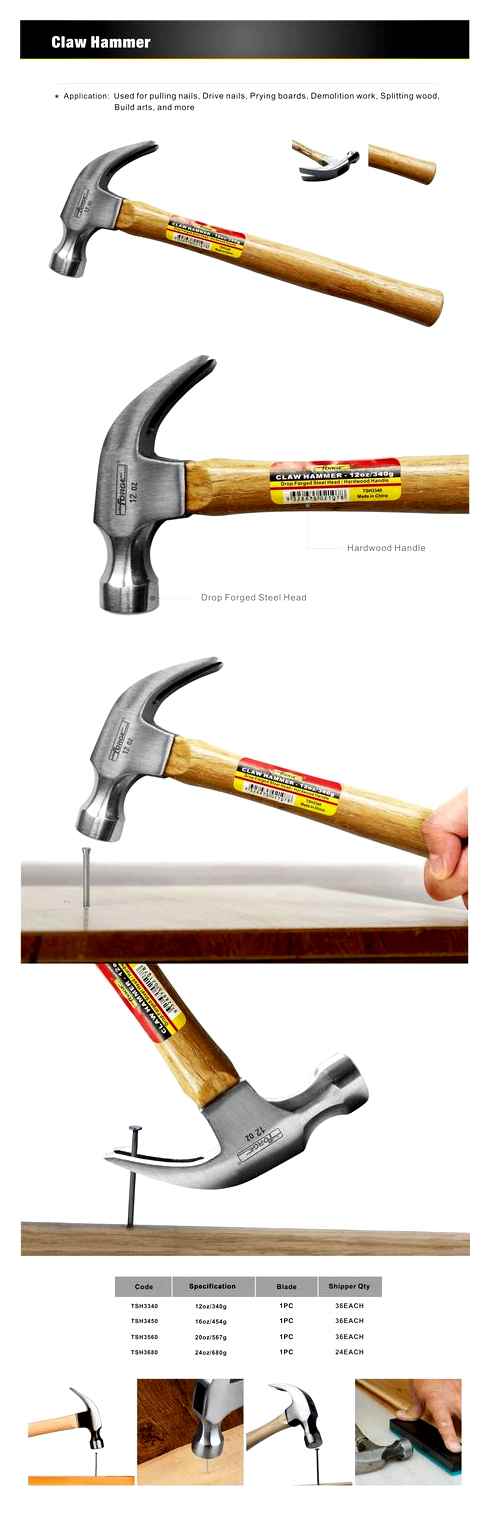
A hammer may seem a simple enough tool, but in fact there are no details. everything is necessary, and even the shaft-holder of the hammer has to be well thought out. If the hammer breaks, you should not be afraid to experiment, especially if you want to have the tool at the same moment when it was broken.
There are a few ways to quickly replace the shaft, but the improvised shaft will not serve for a long time. But if a substitute for the shaft of the hammer will be used, in this case it is better to try the repaired hammer on something several times before starting to use it actively in work.
When making holders, it is important to consider the fact that the size of the workpiece should be longer than you want to get in the end. The maximum reserve is about 5 cm. In general, the handle should be tapered to the end that faces the striking part of the tool.
The process of putting the handle on the hammer
Often the size of the hammer head hole at the top and bottom inlets is slightly wider than in the middle. Thus the dimensions of the handle blank in the thin end part should correspond to the dimensions of the holes in the middle of the striker part of the tool. It is mandatory to check if the handle hole is properly made on the striker with the tool. You can see how this is done in the photo.
Here you can see the striker of an old hammer, which needs preliminary machining. Without these operations it would be impossible to fit the handle. Paying attention to the picture we can see that the striker moulding was made rather badly, there are big metal depressions and roughness, every entrance to the holes on the both sides is different for 6-8 mm than in the striker centre.
To correct all defects and irregularities, the inside and outside of the hammer head must be filed. Then insert the thin end of the handle into the bottom hole of the hammer to get the dimensions right. The tip of the handle should be flush with the opposite side of the striker. If the thickness of the handle is greater than the corresponding holes, you need to sandpaper it so that the element is inserted into the hole of the hammer with a certain tension.
Due to the fact that at the end of the handle we achieve a hollow cone, it will be more tightly pulled on the head of the hammer when it is deeper. It is worth noting that during this process, it is important to keep in mind that the firing pin on the handle should be at right angles without any misalignment.
To hammer the handle into the hole of the striker you need to hit it with back side against the anvil, workbench table etc. in vertical position.
Due to its weight, the striker part of the hammer will slowly be placed on the expanding cone of the handle by its weight. At the same time it is categorically not recommended to hammer on the back side of the handle with hammers or hard objects, because it will lead to its split. This method should only be used when attaching a non-metallic striker (wood or plastic) such as a mallet.
After the head of the hammer is firmly seated, and no more movement of the handle in the striking part can be observed, it is necessary to saw off the protruding part with a hacksaw blade, giving half a centimeter above the striking head beforehand. This is why it is necessary to use a longer billet.
How to Make a Sledgehammer
Before we proceed to the description of operations, it should be noted that the process of making a sledgehammer striker involves forging, which requires special tools, equipment and experience. If you do not have an anvil and a high-temperature oven, this manual will be for you only theoretical. You can look for the beater on ad sites or markets. In any case, its cost will be less than that of a finished sledgehammer. Well, for those who are not by hearsay familiar with the forging business, with the features of the product.
For the production of the striking element of the sledgehammer you can use carbon structural steel of 50, 45, 55, 50G, 50G2 grades. This metal is used in the production of truck axles, so if you don’t have the right material, you can look for it at your local auto shop. The work requires a rectangular piece weighing 3 kg, from which a parallelepiped must be forged.
The next step is to make a place for fixing the handle. For this purpose, on one of the sides, in the center, we punch a through hole with diameter from 25 to 30 mm. The sides of the workpiece are thus deformed. After releasing the hole, you need to hammer the side faces so that the object takes the form of an even parallelepiped again, and the round hole becomes an oval.
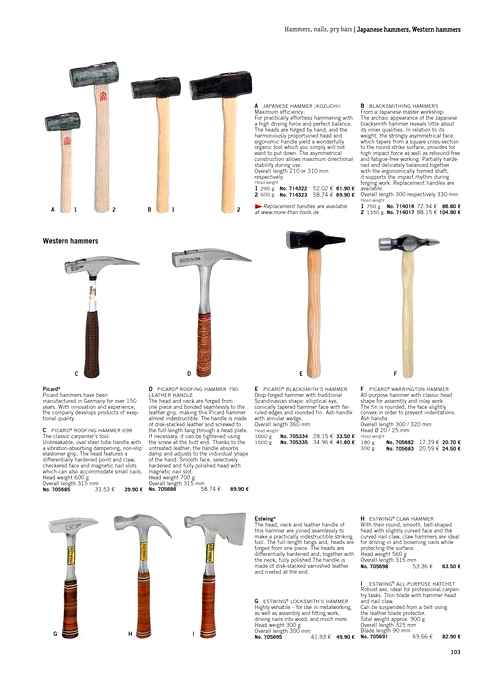
To make the attachment point as secure as possible it is necessary to form a cone shaped hole, tapering from the side edges to the center (the striker section resembles an hourglass). This operation requires a special cone-shaped steel gauge rod to be forged. Section of the gauge should be oval and its length should be 180-200 mm. The lower part of the cross-section, should be a couple of millimeters narrower than the hole made in the striker, and the upper part slightly larger than the handle you are going to install. After forging, the Caliber must be hardened and polished.
To properly calibrate the hole, hammer the steel rod to a depth just below the center of the punch. When deepening the gauge, the sides will be deformed. They must be straightened by removing the Caliber and forging the ends of the workpiece. Then hammer the caliber into the hole once again, and without taking it out, hammer the sides and set the ends. When the workpiece is shaped like a regular parallelepiped, repeat the calibration process on the other side of the hole.
When the bead is properly shaped and securely fastened, you can move on to the hardening stage. To make the steel really hard you need to heat it up to 850 degrees Celsius until it has turned a bright red color. When the necessary temperature is reached, immerse it in cold water until it cools down.
Now that the steel is hardened, it needs to be made malleable, so that it does not crack when you work on it. For this we heat the product to 250-300 degrees and slowly let it cool. After cooling, sand the metal surface and read how to put a sledgehammer on a wooden handle.
Handle for a sledgehammer with their own hands
Very easy to make wooden handle for a sledgehammer, is considered the least inertia and durable if you choose the right material. The most suitable species of wood for the handles, are birch, elm, mountain ash, maple or ash. It is desirable that the source material was split, not sawn, and had no knots. You can also take an ordinary bar, but the strength will be lower. The length of the handle depends on your requirements, but on average, for a striker weighing 3-4 kg, 600-800 mm is enough.
The first and the most important step in the process of creating a handle for a sledgehammer with your own hands will be deburring the workpiece with a plane, axe or other suitable tool. The handle thickness should gradually grow from the beginning (the place of grip) to the end (the place of striker fastening), which size should be slightly larger than the size of the hole in the striker. To be as strong as possible, the handle should have a stiffener, so it should be oval rather than round.
When the wooden workpiece will have the necessary size and shape, you can move on to the final stage of work. Below, we will tell you how to attach the striker and how to wedge the sledgehammer, firmly fixing the position of the elements.
How to Make a Sledgehammer
Before proceeding to the description of the actions, it should be noted that the process of making a sledgehammer striker involves forging, which requires special tools, equipment and experience. If you do not have an anvil and a high-temperature oven, this guide will be for you only theoretical. The beater can be found on ad sites or in markets. In any case its cost will be less than the cost of a ready made sledgehammer. Well, for those who are not hearsay familiar with the forging business, with the peculiarities of the product.
Carbon steel of 50, 45, 55, 50G, 50G2 grades is used for hammer striker element production. This metal is used in the manufacture of truck axles, so if you do not have suitable material, you can look for it in the nearest garage. To work you need a rectangular piece weighing 3 kilograms, from which a parallelepiped should be forged.
The next step is to make the place for fastening the handle. To do this, on one side, in the center, we punch a through hole with a diameter of 25 to 30 mm. The sides of the workpiece are deformed. After releasing the hole, it is necessary to hammer the side faces so that the object takes again the form of an even parallelepiped and the round hole becomes oval.
To make the place of fastening the most reliable, it is necessary to give it a cone shape tapering from the side edges to the center (in the striker section it resembles an hourglass). For this operation it is necessary to forge a special cone-shaped steel gauge rod. The cross-section of the gauge should be oval, and the length, is 180-200 mm. The lower part of the section should be a couple of millimeters narrower than the hole made in the striker, and the upper part should be slightly larger than the handle you are going to install. After forging, you need to harden and grind the caliber.
For correct calibration of the hole, it is necessary to hammer the steel rod to a depth just below the center of the punch. When deepening the gauge, the side edges will become deformed. They need to be straightened by removing the gauge and forging the ends of the billet. Then hammer the bit into the hole once more, and without taking it out, hammer the sides and set the ends. When the billet is shaped like a regular parallelepiped, repeat the calibration process on the other side of the hole.
When the flank is properly shaped and securely fastened, you can proceed to the hardening stage. To make the steel really hard you need to heat it up to 850 degrees Celsius until it is a bright red color. On achievement of necessary temperature, we immerse in cold water until cooling.
Now that the steel is hardened, it is necessary to give it plasticity, so that it does not split when working. To do this, heat the product to 250-300 degrees and let it cool slowly. After cooling down, we grind the metal surface and read how to put the sledgehammer on the wooden handle.

Handle for a sledgehammer with his hands
Very easy to make wooden handle for a sledgehammer, is considered the least inertia and durable if you choose the right material. The most suitable wood for the handles, are birch, elm, mountain ash, maple or ash. It is desirable that the source material is split, not sawn, and has no knots. You can also take an ordinary bar, but the strength will be lower. The length of the handle depends on your requirements, but on the average, for a striker with the weight of 3-4 kg, 600-800 mm is enough.
The first and the most important step to make a handle for a sledgehammer with your own hands is to file the blanks with a plane, axe, or other suitable tool. The thickness of handle should smoothly increase from the beginning (place of grip) to the end (place of attachment of the striker), which size should slightly exceed the size of the hole in the striker to be put on. To be as strong as possible, the handle should have a stiffening rib so it should be oval rather than round.
When the wooden block has the necessary size and shape, you may pass on to the final stage of the work. Below, we will tell you how to attach the hammer and how to wedge the hammer, firmly fixing the position of the elements.
kak_eto_sdelano
I came across an old Soviet hammer without a handle, which has long lain idle in my workshop.
I have made such grips for my hammers a few times before, which became gifts for friends.
The Internet is full of pictures of the anatomical structure of the bones. We choose a more informative and simple drawing, estimate the size of the hammer and the approximate size of the bones and cut rebar.
In my work I took a 12mm round armature for the handle and 10mm for the fingers of the hand.
Of the tools I needed only:-angular grinder,-welder.
I used a semi-automatic machine, but there are good enough and inverter for RDS, which may well be in your garage!The workflow is pretty uncomplicated, so instead of tons of text, I’ll just walk through the chapters and note the process on the photo.All of the extra metal on the bones, I did deburring wheel angle grinder.
The handle for the hammer was made from 2 pieces of rebar. In the photo you can see that I marked the length of the handle section on which in the future will be welded to the bones planting a seat for the hammer itself.
The relief of the handle I made with a welder and a little tapping on an anvil, it turned out a forged handle for a hammer in the garage.
And now when all parts separately are ready: hammer, fingers, and handle; we proceed to assembling and welding.
After the hammer was ready, I decided to oxidize and rust it a bit to give it some atmosphere.I heated up the hammer with a burner and doused it with water from the sprayer, which darkened the hammer and made it look more interesting.
If you have a production or a service you want to tell our readers about, write to Aslan (shauey@yandex.ru) and we will make the best report, which will see not only the readers of the community, but also the site How it’s done
Let me remind you that you can now read the posts on Telegram
and as usual on Instagram. Click on the links, subscribe and comment, if you have any questions about the case, I always answer.
Click on the button to subscribe to “How it’s made.”!
A hammer with a forged handle and its making
You can’t surprise anyone with a hammer these days. There’s an abundance of them out there. The handles can be made from various materials. Who likes what, so for the welder more suitable handle from a metal pipe, welded to a hammer. For the carpenter requires a hammer made of wood so as not to damage the handles of chisels, but for the builders a hammer with a plastic handle is suitable.
However, the wooden handle is more attractive. The naturalness and durability of wood, has always been valued by good craftsmen. But there is one thing, with intensive use of a hammer, the handle in the hammer is constantly loose, that is why professionals, tinsmiths and other craftsmen, make the handle forged with iron.
Such a hammer lasts much longer and it is not afraid of misses when the blow is not on the hammer but on the handle, in which case the wooden handle is broken. In addition, the attachment area of the iron hammer increases many times and it serves for a long time. So how is such a hammer made??
To make a hammer with a forged handle you need two metal plates (approx. 120 x 40 mm, depending on the thickness of the handle of the hammer) and a handle of the hammer. The plates can be stainless steel or just iron, from about 0.8 mm thick.
Using two blanks of iron, about 120 mm long, we bend two troughs in a vice, using a metal rod of similar thickness to the handle of the hammer. Align the blanks directly to the handle of the hammer. Check if the handle with the backings will fit in the hole of the hammer, the metal plates should stick out from the hole of the hammer at the end about 5-6 mm. Subsequently, they are unbent, flared, and they hold the hammer to the handle.
Place the hammer on, adjusting the plates, if they are resting against each other, trim the edges of the plates. After the hammer is set, we drill a through hole on the handle, 10 mm from the edge of the plates, and insert the rivet. And on the end of the hammer, as mentioned before, we rivet the ends of the metal plates. In the end of the wooden handle you can also install a wedge.