Disassembly of the percussion barrel assembly
- Disassembly of the Bosch perforator barrel assembly begins from the side of the cavity, took out the cylinder poz.26 from it with the hammer poz.27;
- The firing pin assembly must be removed from the cavity;
- From the side of the chuck shaft Remove the retaining ring, pos. 85, the steel ring, pos. 38, and one more retaining ring, pos. 85;
- Remove the spur gears pos. 22.
Removing the mode switch
Put the puncher on its side, Remove the mode switch pos. 832.
First turn the switch to the Drilling, press the screwdriver all the way into the end face of the switch button (it is red) and turn the switch counterclockwise by an angle of 70º.
Rock the switch handle, pull the switch handle out of the case.
Instructions for disassembling the Bosch rotary hammer
The principle of operation of the Bosch 2-26 rotary hammer does not differ from well-known brands of rotary hammers. The rotating rotor transmits torque to the intermediate shaft of the mechanical unit of the rock drill, while transmitting the translational motion through the rolling bearing to the hammer hammer mechanism and the impact impulse. Rotational moment with translational shock impulses is transmitted to the working tool. This principle is implemented in all rotary hammers.
But in various firms that produce perforators, there are design features.
Bosch rotary hammers are considered the best in the power tool segment. But nothing everlasting comments.
If your Bosch 2-20, 2-24, 2-26 rotary hammer has stopped working, then you can restore it yourself. You need to have basic locksmith skills and a little understanding of electrical engineering. And another important detail, the design of Bosch rotary hammers is so simple that it does NOT cause difficulties during repair.
When repairing power tools, including repairing Bosch rotary hammers, strictly follow the safety precautions when working with electrical appliances.
To facilitate the repair of the Bosch rotary hammer, its disassembly and assembly Study the tool assembly diagram:
Drill diagram Bosch 2-26
Any disassembly of the bosch 2-26 perforator begins after inspection, test switching and identifying the causes of the device malfunction.
Disassembly of the Bosch rotary hammer 2-26
Dismantling the hammer assembly
I put the Bosch 2-26 perforator vertically on the handle, Unscrew the four screws pos. 90 holding the cover of the mechanical assembly.
Press on the end of the percussion shaft and remove the cover. Black plastic cover.
Now you need to remove the barrel and poz.821 intermediate shaft poz.826. They are NOT secured by anything.
Then, using a screwdriver, you need to remove the bracket pos. 48 of the rolling bearing pos. 830. By the way, in a simple way it is called drunk bearing. Sequentially removed: sleeve pos. 26 and drunk bearing.
Got to the drunken bearing
Drill Bosch hammer, but do not hammer
If the hammer drill has stopped hammering, but at the same time allows the drill, the most likely prerequisite may be destruction drunk bearing. This malfunction is not common and it is not easy to find it.
To fix it, you do not need to go to the Repair Shop. Any person who is more or less versed in mechanics will eliminate such a malfunction.
New drunk bearing
First you need to disassemble the Bosch rotary hammer to the intermediate shaft. Disassembly procedure is as above.
By removing the intermediate shaft, you will get to drunk bearing. Broken cage, scattered balls, cage pieces indicate the destruction of a rolling bearing.
We take out the bearing, remove dirt, all parts of the destroyed mechanism.
Buy new drunk bearing, and, having lubricated all the parts with new grease, replace and assemble, in the reverse order of the steps for disassembly.
Dismantling the intermediate shaft
The intermediate shaft is disassembled by removing the shaft pos. 24 and pulling it out of the housing, pos. 77 drunk bearing.
Bearings are removed with pullers or manually using a tool.
How to choose a puncher for personal use?
Choose the right drilling tool. Means to facilitate the repair work at home for a long time. How to successfully choose a puncher so as not to overpay for the brand and get high-quality equipment?
Several decades ago, I used only powerful electric drills, equipped with drills for metal and concrete. A truly branded, specialized tool was sold only abroad, you could not just go to a construction supermarket and choose a suitable device.
Punch device and characteristics
All punchers are divided into three types in terms of functionality:
- Single-mode. Impact drilling function only. Most often, such perforators are NOT used in everyday life, but are used as professional additional equipment for narrow purposes.
- Dual-mode. Hammer drilling plus classic drilling or chiseling only.
- Three-mode. The tool is equipped with all the functions specified in paragraphs 1 and 2.
The choice of a hammer drill is based primarily on the characteristics of power and impact force. The higher these figures, the better the hammer to fit.
Types of working chuck for rock drill:
- Usual;
- Keyless.
Which drill chuck to choose? For household or household chores, the keyless quick-release model is best suited. Changing the nozzle in this version is convenient, easy and quick.
Rock drills classification by weight:
- Lungs. Up to 4 kilograms. Power is no more than 700 watts. Have only SDS-plus cartridge for no more than 26 mm.
- Average. 4 to 8 kilograms. Power from 700 to 1500 watts. Depending on the equipment, both SDS-plus and SDS-max are equipped.
- Heavy. than 8 kilograms. Power is over 1500 watts. Equipped only with SDS-max chuck up to Ø 60 mm.
What is the difference between a drill and a hammer drill and vice versa
The hammer drill is characterized by a longitudinal axial movement of the working part, similar to an impact drill. Therefore, hammer drills are confused with a heavy drill. In words, the difference is practically comments, but the hammer drill operates on the basis of pneumatics, and any impact (heavy) drill works thanks to mechanics.
Hence the difference in surface speed. Pneumatic drilling of holes in concrete, brick and stone walls reduces the physical stress on the user. For any impact drill, similar work is associated with great fatigue, and the mode hammer drilling wears out the internal parts of the drill very quickly.
We come to the conclusion that the hammer drill should be larger and more massive than a drill with an impact function.
Impact energy and frequency
For a hammer drill, the impact function, measured in joules, is very important. Here the impact energy depends on the performance of the device, as well as the diameter of the hole being machined. For daily work with a hammer drill, this is one of the most important indicators.
It is essential that the impact drill is maximum very quickly deplete its resource, and with a hammer drill they perform this work for a long time without wear, especially with a single-mode model.
It turns out that energy and frequency determine the level of performance. When choosing a perforator yourself, you need to estimate the amount of work on chiselling, then, according to the specified characteristics of the impact frequency, calculate the approximate productivity.
How to choose a hammer drill for home
It is best to start the selection, starting from weight and power. Super-productive home model is definitely not needed.
Suitable criteria for home conditions and the following brands:
- Power from 600 to 900 watts.
- Shock 1.2 to 2.2 J.
- Three-mode medium punch. Drilling, hammer drilling, non-rotating impact.
- The rotation speed is necessarily regulated.
- Anti-jamming clutch.
- Keyless chuck.
- Replacement branded cartridge included.
According to these characteristics, three leading brands are distinguished:
- Makita. Sufficiently lightweight drills and hammer drills, with a warranty of several years. Proven as tools for household daily work, easy repairs. Average market price available, easy to operate. How to choose a hammer drill for home is this brand? Users refer to the Makita RK 2450 model. The required (useful) power is 700 watts, a shock of 3 joules, revolutions up to 4.5 thousand.
- Bosch. German quality and assembly. Pioneers in professional power tools and household equipment. Any models have been tested by time, weather conditions. Rotary hammers Equipped with the function of precise adjustment of the nozzle speed (drill, drill). When purchasing equipment from this manufacturer, pay attention to the color of the case. Blue classifies precisely the professional purpose. The most popular model. BOSCH GBH 2-24 DF. 790 watts, 2.7 joule impact, complete with SDS-plus replacement chuck and classic keyless chuck.
- Hitachi. The best tool in our market from Japan. Priced in the same category as the Makita, but some power tools, including rotary hammers, are lighter in weight. Are you wondering which hammer drill to choose from this manufacturer? Note the Hitachi DH 22 PG, 620 watts, 1.4 joules of impact and only 1.9 kilograms.
It is not necessary to trust a consultant in the selection of a perforator, or any other technique. Maximum. This is to listen to recommendations. You need to choose and buy a model that best suits your personal requirements.
What parts and how to lubricate?
To begin with, it is worthwhile to understand that one lubricant, no matter how versatile it is, cannot be indiscriminately Process all the parts. One type of lubricant is only suitable for the gearbox, the other. For drills and brown. Each unit, such as the PBH 2100 RE or GBH 2-24 DRE, is supplied with an instruction manual that describes the lubrication frequency of the parts.
Before starting the lubrication procedure, the power tool must be cleaned and blown out, and then wiped dry.
What and how to process:
- Reducer. To the question: what is it worth to lubricate the gearbox of a household or professional puncher, the answer is as follows. Composition in the form of liquid oil. The substance is simply poured in certain quantities into a specially designated place in the shell of the device. Oil fills the gearbox housing, and during operation, all its parts are covered with a uniform layer of grease. If there is no special hole in the power tool and you need to disassemble it in order to lubricate the gearbox, it is better to contact a specialist.
- Storms. It must be Lubricated before each installation in the cartridge. How to Lubricate the Storms of a Rock Drill? All grooves of the nozzle are processed with a small amount of the agent. The instructions for the apparatus usually indicate the type and amount of a lubricant that can be used to handle storms.
- Cartridge. The ponytails of the replacement drill bits also need to be machined each time before installation. The amount of the drug should be strictly the same as indicated in the instructions, no more and no less. How and with what to lubricate a hammer drill chuck (a special attachment that is used to securely hold a drill), for example, HR2470 or any other? You just need to apply drilling lubricant to the brown tail and then insert it into the socket of the chuck. And after removing the nozzle, it must be cleaned of dust and recycled oil.
And how to lubricate the piston of a perforator? Each manufacturer has its own piston lubricant. It is best to use the original.
Components that DO NOT require sliding during operation (transfer clutch, core, firing pin, cylinder) do not need to be lubricated.
How and what to lubricate the hammer drill: lubricants for 6 brands
The puncher is useful if you need to make a hole in the wall, grind Kolley under the wires and for other construction issues. The tool will serve its owner faithfully, if you do not forget to take care of it.
Elements such as storms, reducer, cartridge need periodic processing with special equipment. How and with what to lubricate various types of rock drills? Here. Answers and nuances of processing electric devices produced by 6 well-known brands.
Design features
Such power tools are barrel and straight, mechanical and pneumatic, and depending on the size. Light, medium and heavy.
- Core;
- Storms;
- Striker;
- Piston;
- Cylinder;
- Electromagnetic coil.
There are differences in details depending on the type of fixture. And that’s not all the details from the list. So how does a device useful in construction work. Perforator? The units, in addition to the above parts, are equipped with:
In addition, such instruments have a variety of indicators and speed controls. Having dealt with the nuances of the device of this construction tool, it’s time to move on to lubricate its SEPARATE elements.
What kind of lubricant is best for which rock drills?
The best way. Use only branded lubricants. So that the craftsmen do NOT rack their brains, what is the best and best way to lubricate the punch, the manufacturers of THESE devices made sure that their assortment included special means for this.
How else can you lubricate individual elements of the BOSCH rotary hammer (Bosch)?
The brand manufactures over 300 types of various tools, including punchers. And to all these devices. and thousands of accessories.
To care for destructive the company produces the following tools:
The assortment of the Japanese brand includes:
The Japanese corporation also took care of its customers and provided a wide choice of how to lubricate the Makita rotary hammer.
SPARKY Multipurpose grease can be used, eg 042005-4A. Alternatively, use SPARKY Part-Specific Lubricants. Reducers (042024-0А) or brown (181573-3).
A set with many Energomash models is already supplied with grease for gearboxes and tails. If there is none or the product has run out, use multipurpose grease 042005-4A.
Basically, all manufacturers of rock drills equip their products with branded lubricants, complete with the delivery of equipment. You can use both universal options and substances for gearboxes or borax. Many masters prefer to use ordinary lithol instead of original means, which is fundamentally wrong, because K. It is not resistant to moisture. This can lead to the formation of corrosion on the internal components of the device. Therefore, it is worth using branded lubricants, clean and handle the power tool as necessary, and then it will 100% serve for more than one year.
Instruments
For professionals in their field, replacing or repairing a punch chuck is NOT difficult. However, what to do for those who are NOT involved in construction and repair at a professional level? Since any man in his life at least once held a drill in his hands, he should be informed in the process of removing, as well as replacing her cartridge. At the same time, the reasons can be very different, starting with the slow operation of the gear rim and ending with a major breakdown. How to change a chuck for a hammer drill? Let’s consider the replacement in more detail.
:. How to remove a cartridge from a punch
The first step is to determine which cartridge is used directly in your rotary hammer. They are cam, SDS collet and quick-clamping. The latter, in turn, are one- and two-sleeve. In the chuck, the drill is fixed with a key, which cannot be said about SDS collet and keyless chuck. In order to replace the drill into an SDS collet chuck, you just need to turn it.
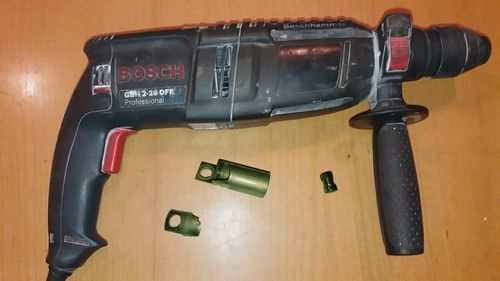
Replacing a chuck with a hammer drill begins with studying the mountings. It can be held by a screw rod or a spindle. In most cases, removing the cartridge is NOT difficult. However, sometimes there is also a stronger fixation, which will require patience and additional tools. In a simplified version, the firmly fixed chuck is removed with a hammer, wrench and screwdriver. The withdrawal process is as follows:
How to disassemble a punch chuck
When disassembling the cartridge, it is necessary to take into account the manufacturer, because the disassembly of the punch cartridge will differ significantly. To date, the list of the most popular includes:
Consider the disassembly using the example of a cartridge for a Bosch hammer drill:
1. The plastic part moves aside, the rubber seal is removed.
2. Wielding a screwdriver, carefully remove the fixing ring.
3. Further Fixing washer.
4. With the puck we will see the second ring. It should be returned and removed, also prying with a screwdriver.
5. On the plastic part we see the SDS clamp, which consists of a spring, a ball and a washer. The ball is removed first, then. Washer and spring.
The cartridge is disassembled for various purposes: repair, replacement of SEPARATE parts, cleaning, lubrication, etc. The chuck for a Makita hammer drill worthy of manufacturers is disassembled in about the same way, with the exception of single nuances, which are taken into account, based on the design of the chuck.
After disassembling and producing everything that was planned for working with the details of the cartridge, a natural question arises: how to assemble the cartridge of the hammer drill? Just Use the disassembly instructions, starting with the last step and ending first (do everything exactly the opposite).
Punch chuck device
Almost any construction tool is versatile, and hammer drills are no exception. There are many different attachments, adapters, cartridges for them. The basis for any kind of work is the cartridge. The hammer drill adapter is used to mount a drill that has been removed from a conventional drill. Nozzles and drills have a huge variety and are selected in accordance with the tasks set.
Always keep a replacement punch chuck at home, as one can fail at any time. It is also worth noting that it is preferable to use different cartridges for each type of work. The main types of cartridges are:
Amateurs often wonder why so many types of cartridges are needed. Recall that there are rock drills with higher and lower power. If the tool is powerful, then you need to think about securely attaching the drill and nozzles. A cartridge such as SDS-max is designed for deep landing, which means that the probability that the drill will fly off during operation is minimized. It is the same with less powerful perforators, which are designed for jewelry work. In this case, more emphasis is placed not on fixation, but on accuracy.
In order to know how to repair a hammer drill cartridge, you need to study its device. But how does the punch cartridge work??
At one time, the drill was fastened by means of movable cams, but progress does not stand still. In SDS, the drills are locked by 2 guide wedges and 2 locking balls. SDS-plus and SDS-max differ only in the number of guide wedges (1 more in the latter). Thus, the mount comes out very reliable and fast.
The fixing of the nozzle itself has also been simplified: you just need to insert the selected nozzle into the socket of the cartridge, slightly press and wait for a click. Thus, the nozzle is well fixed. Removing the drill Also not particularly difficult: pressing the movable cover. And the storms extracted.
Additionally, a hammer drill may include:
How to replace the punch chuck
We have already written above that the cartridge will not fit any drill. We also reviewed the process of removing and even disassembling the cartridge. To install a new cartridge, follow these steps:
disadvantages
The main disadvantage of the Bosch tool. This is a pretty high price.
Rotary hammers from Bosch are divided into types:
- Household models (Engines 410-720 watts). In such units there are three standard modes, their weight is small (no more than six kilograms).
Letter R defines the model as a unit for domestic use. Usually such a tool is marked with a green color scheme. The disadvantage of such machines is not the best cooling and increased efficiency.
Such models have much more advantages than disadvantages, among which it is worth mentioning:
- Average price;
- Low weight;
- Compact dimensions;
- Good performance;
- Reliability in work.
- The second large class of instruments from Bosch. These are professional rotary hammers with a power of 810 watts and more, their weight ranges from 6 to 12.5 kilograms.
The advantages of this model. This is effective cooling of the unit, minimal vibration, and reliable operation. If we talk about the shortcomings, then we should mention the large size of such devices and the high price.
- Cordless rotary hammers from Bosch can operate from a 220 volt network. There are also devices that operate in a wireless mode from a battery. Lithium and cadmium multi-charge power supplies are used. Such punches are badly needed in locations where there is no mains power. Professional cordless rotary hammers can work up to 6-8 hours.
- All units with a vacuum cleaner from Bosch equipped with a useful device. Dust collector. Such a device significantly extends the life of the unit. The manufacturer also includes a vacuum cleaner, which operates from an autonomous power source.
- Drill perforator. Has the following technical characteristics:
- Power. Up to 1.6 kW;
- Rotation. No more than 3980 revolutions;
- Number of hits. About 50 per minute.
- The Bosch pneumatic hammer drill is equipped with a 750 watt motor and a speed of 855 rpm. Drill holes can be made in medium-density concrete (up to 25 mm thick), dense wood, steel (15 mm). Weight. About three kg.
Specifications
Perforator Bosch. This is a tool which is especially popular among professional builders. Seriously, these units have to be repaired infrequently, but, like any equipment, perforators from Bosch need preventive maintenance over time.
Aggregates from Bosch are divided into two large classes:
- Perforators in which the engine is horizontal (the layout of the barrel and anchors are parallel)
- Perforators where the engine is vertical. In this case, all working nodes are located at a certain angle.
The hammer drill has mechanical and electrical units. The second block consists of the following nodes:
- Engine;
- Engine control device;
- Button and switch block;
- Replaceable cord;
- Noise reduction block.
The mechanical assembly is assembled from the following elements:
- Gearbox (mounted directly on the engine shaft)
- Shock impulse mechanism;
- Chuck, brushes, anchor;
- Clutch that provides traction.
Also, along with the perforator itself, various removable removable elements are included in the set:
- Drill;
- Boers;
- Crowns;
Benefits
Rotary hammer performance Bosch characterized by three criteria.
- Spindle speed (650 to 2200 rpm).
- The impact power is directly related to the characteristics of the engine, the weight of the striker, the distance of its working stroke. This is one of the main indicators of the quality of the tool. It varies from 1.5 J to 14 J. The most expensive models can cost 50 thousand rubles.
- The impact frequency is characterized by the number of mechanical impulses per unit of time (one minute). In models from Bosch the indicator can range from 1000 to 5600 beats per minute.
In models from Bosch all three parameters are organically combined, which makes it possible to call rotary hammers from this manufacturer the best in the world.
Rotary hammer models from Bosch can perform the following functions:
- Rotation;
- Hit;
- Spin and kick at the same time.
How to choose?
In order to choose the right hammer drill for your home, it is worth considering several fundamental factors. For household work, units are suitable, the power of which does NOT exceed six hundred watts.
In the work of any punch, the layout of the engine is important. If the motor is located in a horizontal plane, then such a device is applicable for small narrow holes. The engine in such models is arranged along the shock axis, which does not allow it to cool quickly.
The vertical engine layout increases the power of the rock drill without the need to constantly cool the engine. Such devices are in demand among professional builders, the performance of such perforators is high.
When choosing, you should look at the marking. If the inscription SDS is present, then this tool can work on concrete. When choosing a punch, you should read the instructions, consult with the seller, who can give valuable practical advice.
Also on rotary hammers Bosch there are such letters: PBH or GBH.
- G means the unit is suitable for professional use;
- R. This is the letter with which household appliances are marked.
The numbers show how much the hammer drill weighs (example: 3-30, 2-42). Letters in words:
- D. Used for chiselling;
- F. Use with mixed cartridge;
- R. There is a reverse.
Perforators Bosch: description, types and repair
- Specifications
- Benefits
- disadvantages
- Kinds
- How to choose?
- How to disassemble and repair?
A hammer drill is a tool that undergoes heavy mechanical stress. For the normal operation of the unit, routine inspections and repairs should be carried out. If you do not take into account such rules, then after a short time the device will become unusable.
Bosch. It is one of the world leaders in the production of power tools, including rotary hammers. Maintenance of such equipment requires the participation of certified service centers. Minor problems can be repaired by yourself.
How to disassemble and repair?
The appearance of malfunctions in the hammer drill is characterized by sound signals:
- A grinding sound appears;
- Weird Noise Background;
- The engine starts to work;
- Power is lost;
- There is a smell of burnt wiring;
- High vibration appears.
Most often found in the hammer drill Bosch such breakdowns:
- Failure of switches;
- Wear of the rubber sleeve between the striker and the striker;
- Termination of the operation of the mechanism itself providing the blow;
- Malfunction of gears or their wear;
- Clamping unit defective. He ceases to hold on to storms;
- Lost electrical connection.
Also, defects in the wiring provoke the appearance of a spark and overheating of the unit.
Electrical faults are as follows:
- The engine does not work;
- Broken contacts;
- Burnout winding.
To fix mechanical and electrical faults with your own hands, you need to disassemble the hammer drill. All such devices are made according to the same principle. Repairing a Bosch hammer drill is not much different from disassembling a similar unit in any other hammer drills.
The beginning of dismantling begins with the cartridge: the rubberized boot should be removed, then. The fixing ring, only after that the plastic boot is removed. Then you need to find the ball (located under the washer), carefully remove it. The cause of malfunctions often lies precisely in the wear of THESE parts.
The punch body is dismantled. For this, the switch is removed, which controls the operating modes. The switch is placed in position Hit (There is a hammer symbol on the body). If there is no such designation, then a switch is placed in the designation Impact drilling. After that, a small button is pressed, which is located on the switch itself. It should be pushed back down slightly with the hammer symbol, and a click should occur. After that, the switch is lifted with a screwdriver, pulls towards itself.
In SEPARATE models, the switch is attached to the housing with screws, so it will be enough to simply unscrew them.
If you think that the problem lies precisely in the electrical unit, then the following steps should be taken:
- The screws are unscrewed, the back cover is removed;
- The fasteners are removed, which fixes the network cable;
- The button is dismounted Start;
- All fasteners that hold the stator and armature wires are dismantled;
- The brushes are taken out;
- The electrical and mechanical unit is disconnected. To do this, it is enough to Unscrew a few bolts;
- The rotor is removed, the bearings are inspected;
- The air intake is removed;
- The stator is removed.
A slightly different design is present in rock drills in which the electric drive is arranged vertically. In this case, first dismantle the handle, then use a screwdriver to remove the bolts connecting the housing to the motor.
The presence of a spark indicates that it is necessary to replace the bearings; there may also be defects in the insulation of the rotor and stator. This option is also possible: the collector plates burned out. Damage to the stator also generates copious sparks, and only under one electrode.
It is impossible to do without a tester, you should ring both the rotor and the stator. It will be necessary to measure all parameters step by step, especially carefully. Resistance level on the windings (resistance must be constant). If it is established that all problems are in the rotor and stator, then the unit should be taken to a service center. Such a malfunction can only be eliminated by an experienced specialist.
The easiest repair. This is a replacement for brushes. You just need to open the lid. Brushes are located in special grooves-holders.
Brushes are differentiated into several types.
- Brushes made from graphite. Such brushes are reliable and can work for a long time without interference. Of the shortcomings, it can be noted that their wear is uneven, which negatively affects the collector.
- Carbon-carbon brushes are more durable, replacement is required if 30% of the material has worn off. Even if one brush is normal, and the other is completely worn out, then both need to be replaced.
After completing the work, all units should be cleaned from graphite chips, in this case, alcohol or vodka should be used. Then the electrodes are fitted to the collector. In this case, sandpaper with a minimum grain is used, which is applied to the collector and the electrode is lapped with small rotational vibrations.
When the electrode area is slightly rounded, it will be considered a full contact. Such contact will ensure good adhesion to the surface of the collector plates.
The impact mechanism depends on what type of hammer drill is being repaired. Barrel units have a vertical layout of the engine, the impact block is present on the basis of the crank mechanism (KShM). The connecting rod mechanism contains only one bearing. It is mounted on the very cams of the wheel with an eccentric.
There are also designs where the bearing is attached directly to the base of the connecting rod. When carrying out repairs, as a rule, the connecting rod and eccentric are changed.
Pistol rock drills have a different design: the piston does not move with a connecting rod, but as a result of a dynamic oscillating bearing. Such a bearing is subjected to the greatest stress and wear frequently. The bearing will need to be replaced. Removing the bearing is easy with a screwdriver. It will be enough to hook the bracket and pull it out.
During the work, you should stock up on rags, as well as alcohol. It will be necessary to flush the gearbox.
Other mechanical problems can manifest themselves in the failure of the mode switch. In this case, it should be cleaned. If after that it still does not function like that, then it must be replaced. If gears with an oblique tooth fail, then the hammer stops hammer, also these assemblies must be replaced.
There are 2 reasons for gear breakage: the clutch is broken or the gear is out of order. Replacement of THESE items will be required.
If storms fly out of the cartridge, then there are several reasons:
- Deformation of the ball elements has occurred;
- Has aged safety ring;
- The spring that fixes the.
With such malfunctions, you will have to disassemble the cartridge and look at all the details.
If a storm gets stuck, it indicates that the lubricant on the liner is dry or insufficient. To eliminate such a malfunction, it will be necessary to drip oil into the nest.
Storms also get stuck for a reason hardening accumulated dust. In this case, a little machine oil should also be added.
If a standard drill was used with the hammer drills, then it will need to be processed with special WD-40 solutions. Then wait a few minutes, then. Gently loosen the drill in different directions.
For how to fix a Bosch hammer drill, see the following.
We disassemble the punch step by step. Quick search for breakage
Just imagine that your tool suddenly stops working or you urgently need to replace any faulty part. The easiest way. Take the hammer drill to a service center for repair, but it takes time, which means it can stop your work for a while. But if you know how the device is disassembled, it will be much easier for you to carry out the rest of the work. In addition, this will lead to significant cost savings, because there will be no need to spend money on paying for the services of repair centers.
Instructions for parsing the tool:
- We start work, starting from the upper unit: first, the rubber tip is removed, then. Washer, spring, ball ends.
- After you have removed the ball, unscrew the screws that hold the body, remove the handle cover, if available, and lastly disconnect the stator wires.
- Removing the brush holder.
- Next stage. Separation of the gearbox and housing to form a gap. It is through him that we will extract the switch.
- After that, the punch body is placed vertically, with the help of a vice, it is fixed, and all its parts are carefully removed from the device.
Whatever breakdown awaits you, clean the case. Sometimes it is dirt and dust that prevent the device from working normally.
Required tools and materials
Anyone who has ever had to work with a hammer drill knows how difficult its operating conditions are. That is why do-it-yourself punch repair. Such a popular request on the Internet. And today we will tell you absolutely everything about the repair of this tool.
Do-it-yourself punch repair. How to quickly eliminate a breakdown? What you need to know about hammer drill repair?
Undoubtedly, the owners of such expensive equipment want their devices to be of high quality, to do their job 100%. First of all, correct use of the tool will save you from serious damage, which we will talk about a little later. And, of course, the device was repaired on time. At the same time, any small failure should already become a cause for concern and preparation for repair.
So, such beacons I can be:
- Unstable work of the punch in the working mode;
- The appearance of strange sounds when turning on the punch;
- The smell of burning;
- The punch does NOT hammer, although there are obvious reasons for this.
As soon as something like this happened to your equipment, then it’s time to repair. Like any similar work, it requires care, understanding the cause of the breakdown and knowledge of how to cope with it. And your very first step in renovation. Analysis of the instrument into its components. In many, even this stage is difficult, and then you need to know everything to the nuances. How, what and why!
Punch repair yourself step by step
To repair a device such as a hammer drill, you should be as prepared as possible, which will allow you to reduce financial and labor costs to a minimum. It is not bad if you are more or less familiar with the construction of a punch, you know what parts and assemblies it consists of, which will allow you to quickly replace a broken part. Most often, the repair of a puncher is reduced to a banal replacement flew elements, which include:
- Anchor;
- Brushes;
- Gears;
- Starters;
- Bearings;
- Network cables;
- Switches.
It is worth noting that it is easiest to repair light-class tools, given that such a hammer drill is perfect for carrying out construction work at home. But breakdowns of more serious equipment are much more difficult, and only professional craftsmen can handle them. In any case, whichever class of tool interests you, find a model with a vacuum cleaner. This device will save you time on cleaning and also make your work safer as it reduces dust.
One more problem. In the breakdown of the windings, rewinding of the armature and starter, which also occur due to dust. Repair consists in thorough cleaning and replacement of those parts that cannot be repaired. However prevention. reliable method. To do this, you need to clean the device every two weeks, soak it with varnish or grease. By the way, the choice of lubricant must be carefully considered. So, there are several rules. First. It is better to purchase a solution from the same manufacturer (Bosch, Makita, Enkor), As the perforator itself, in this case, in its composition, oil or varnish will be ideal. If you have such a composition at hand, a diesel engine oil is perfect for you.
The second most common cause of breakage is brush wear, no matter how much your tool costs. Even the most expensive models are prone to this problem. It is very easy to replace them: we disassemble the perforator according to the above described scheme, we find worn brushes and put new ones in their place. You just need to correctly determine which of them is best to use: coal, graphite or carbon-graphite. So, graphite ones have a long service life, however, due to the hardness of the material, the collector may suffer. Carbon elements have a short life, but they have high-quality contact with other parts of the hammer drill. The optimal and inexpensive is the purchase of the third option.
There are problems with the mechanical elements of the device. Each model is equipped with switching modes, and they often fail, especially in cheap devices. The operating algorithm is the same. We disassemble the punch, find the broken parts, replace them. The main thing. Purchase items that fit this model. A similar problem often haunts cartridges that are most stressed. First of all, protecting them from dust and dirt, rinse the grease elements. But if the cartridge is still broken, we will have no choice but to change it.
Now you know how to fix a hammer drill and see that most of the breakdowns come down to simple cleaning or replacing defective parts. But if you disassembled the tool, and there are obvious reasons for comments, it is better to take the device to a service center. Specialists will quickly find the cause and eliminate it.