Mini drill for circuit boards with our own hands
A compact home-built mini drill can be used for drilling circuit boards if you suddenly decided to assemble some appliances with your own hands. In addition, it is useful in the ordinary household purposes, if there is a need to drill a small hole in a wooden board or plastic.
Work with such a tool for much more convenient than a large drill or electric screwdriver, as the mini version is much lighter and smaller, allowing you to do small jobs quickly and more qualitatively. Below we will tell you how to make a mini drill from a motor with your own hands, providing photo instructions and clear video examples
The second life of an old tape recorder
As you understand, the first version of the homemade mini drill will be made from a CD recorder forgotten by time. All you need from the former sales hit. a motor that will rotate the chuck with the tool. Since the device is powered by 6 volts, you will need to find an appropriate power supply or a few extra batteries. You can use a USB adapter, but the power will be somewhat reduced in this case. In addition, you need to buy a collet yourself (sold in any radio store or on the market, on the Internet at AliExpress, the price is small) and find a suitable housing for self-made, although it is not necessary, you can hold the tool directly to the motor.
So, in order to make your own mini drill from a motor at home, you need to do the following steps:
- Solder two flexible wires to the contacts of the device as shown in the photo.
- Insert the drill bit in the collet.
- 3. Place the ready nozzle on the motor shaft and fix the chuck with screws. Please note that the hole in the collet has to fit perfectly to the diameter of the shaft which is usually 1.5 or 2.3mm. Otherwise you will find it difficult to remove the vibration when running a homemade small drill. If the hole in the collet chuck turned out to be larger than the motor shaft, you can try to wrap several layers of scotch tape, thick paper, polyethylene or other material. This will compensate the gap and reduce the vibration.
- All 4 bolts on the nozzle carefully tighten, then connect the wires to the power supply and test the ready homemade device. For ease of use, it is desirable to add a button or switch in the power supply gap.
Here is the entire technology of assembling the device with their own hands. As you can see, it is not at all difficult to make a mic drill from a motor, even for a novice electrician. The only disadvantage of such a device is the small strength of a thin drill. If you drill holes not at a right angle it will break right away so be careful and buy some extra drill bits for practice.
A very important point that you should know about. to make the drill rotate in the other direction, just swap the wires! An interesting video instruction on how to make a simple drill, you can see below:
Materials
What materials are needed to create a mini drill with their own hands? To make your own hands a mini drill, first pick up the two most important parts: a motor from some old electric device and a collet chuck.
Stroborezter with their own hands. what is it, step by step instructions
Mechanical clamping device can be purchased almost at the radio market. There is also an electric motor. As a last resort, these parts can be ordered in an online store.
Important! Buy a chuck online advantageous because it comes with a set of different accessories for the mini drill. Assembling a homemade device, you do not need to pick up on the diameter of the shaft drills, grinding and sawing disks.
As for the body, there are many opportunities to make it from any auxiliary materials. It is necessary to have heat shrinkable film for reliable insulation of current-carrying parts.
Rectifier with voltage regulator is needed for the tool to use mains power. You also need a microswitch, a power cord, a soldering iron. Availability of a thermal adhesive gun is mandatory. For rigid fixation of parts it is used instead composite compound. cold welding.
Economical version without enclosure
The most budget model of mini drill is a regular electric motor, to which the power unit is connected through wiring without a housing. For 12-volt motor you need a power block, consisting of a 30-watt transformer and a rectifier bridge, for example, on a diode 1N1007.
Inclusion of a simple capacitor, up to 25 V with a capacitive characteristic of 1000 microfarads in the circuit will allow to protect the motor from the pulsating oscillations of the winding in the process of rectifying the voltage.
The chain works reliably, but as the load increases, for example, when drilling in thick material, the voltage will drop, leading to a stop rotation. You can stabilize the voltage by adding a KR142EN8B or L7812CV regulator to the circuit
Once the drive unit is ready, you make or buy a chuck. for home drilling of miniature holes, even a rod from a pen, in which the glue is fixed drill. Also the chuck can be replaced with the previously suggested collet or screw clamp.
Mechanical
For this mini drill you need any mechanism with gears from horizontal to vertical plane. The best version, from those available in everyday life, is a fly-away spool from a fishing rod.
This option is especially good because the entire mechanism already performs rotational motion, it has a handle, so you will need to make minimal effort in the manufacture of a mini drill.
But, to get a suitable chuck, still have to. As in the previous version, for it you can take a part from an old unwanted electric screwdriver, a collet or a sleeve. The collets are best selected after taking the coil apart when you can measure the diameter of the shaft.
The process of making a hand drill can be divided into these steps
- Unscrew the nut and remove the cassette Reece. 13: unscrew the nut
- Measure the length of the shaft and the depth of the future chuck. if these parameters are commensurate, you can attach them to each other; Fig. 14: measure the length of the shaft
- Use the collet or bushing bolt to secure the chuck to the shaft; Fig. 15: Collet for the shaft
- If the handle of the spool is too large and you are catching the work surface with your hand while drilling, it should be shortened so that it does not get in the way;
To shorten the arm, saw off part of the arm and re-fix the handle of the mini drill with the pin. Handheld mini drill is ready for use, but it should be noted that you should not put too much pressure on the drill bit because it will easily break or deform.
Full analog of the factory-made “dremel
First thing you need to construct a mini drill is a miniature 5 to 12 volt electric motor. You can find them in children’s toys and decorative toys, old cassette players, printers or portable fans. In many stores they are sold in the electronics and modeling section, including online stores.
An example of a drill
The original case is also self-made so that the motor fits snugly inside, but leaves a gap or open part where it heats up.
The body of mini drill can be any plastic tube.
You can find models that use a tube of sealant, a syringe, a plastic tube of toothpaste or candy for kids.
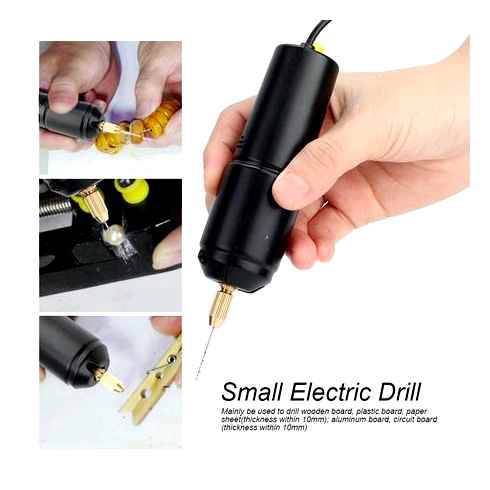
Also a piece of plastic pipe sawed to the right length will do, but in this case, the open ends will need to be plugged with some movable “plug”, such as acrylic or cut out of plastic.
The chuck or clamp of the mini drill can be made by yourself, for example, from a normal connection terminal, or you can buy it at the market or in a store. For a collet, you can go to engraver shops, as well as in the departments for modeling or the section of components for household power tools.
The resulting tool is a universal option; depending on the type of repair, various attachments are fixed with such a clamping chuck: drills, cutters, discs with a cutting edge or screwdriver heads.
Hand drill with their own hands: instructions for making
Everyone who makes electronic crafts or does fine arts and crafts work needs a small electric drill. Such a machine is ideal for small jobs on wood, plastic and metal, drilling circuit boards.
To assemble a hand drill at home can be made of a chuck, a soap bubble jar, a motor for chuck rotation, a battery.
The motor can be taken from a hair dryer or an angle grinder. The electric motor from a video recorder, the motor from an old cassette recorder will also be suitable for making an article.
To make an electric mini drill you need:
- Connect the chuck with the motor. The best way to do this is with cold welding. But you need to work quickly and carefully: welding quickly hardens and becomes as strong as iron. Redo the connection, if unsuccessful, will not work.
- Place the chuck in the jar. For better fixation, the cartridge should be treated with hot melt glue.
- Make a hole in the second base for the switch. It is better if the switch is small, key-operated.
To make a drill with your own hands, you should study the theory and watch an instructional video
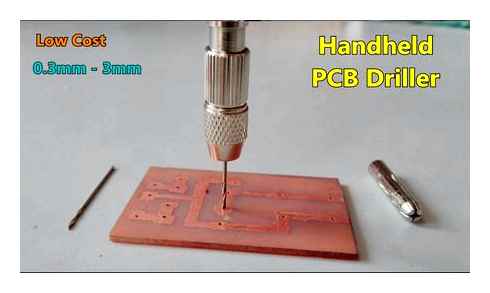
The handheld mic drill is ready! All that remains is to solder the wires from the motor and power to the switch, observing the polarity. A 9-12v battery is enough to power the mini drill. Optional reversing can be done on a six pin switch.
Economical alternative without housing
Moving on to building a mini drill with minimum costs. We don’t buy anything except the motor itself (though you can find it for free in old appliances). Most compact motors are designed for 12 volts DC. This is what we build the power supply for.
As there will be no additional options (speed regulator, voltage regulator), the power supply is stabilized by a constant load. A typical 12 volt micromotor operates with a current not exceeding 2 amps. A simple calculation shows that the output power should be 24 watts. Add 25% rectification losses and you have a 30 watt transformer.
To get 12 volts under load, it is necessary to remove 16 volts from the secondary winding. You can make such a transformer in an hour, from any unnecessary power supply. Then you have rectifier bridge on any diodes: for example 1N1007.
Our motor does not need the pulsations of rectified voltage, so at the output we connect the electrolytic capacitor for 25 volts, the capacity of about 1000 uF. It will smooth out the output current. This tandem works very well in spite of its simplicity, with only one disadvantage: with increasing load the voltage drops. That is, when it rotates evenly, the power supply unit outputs 12 volts. And if you are drilling “heavy” material. you need to monitor the speed, not letting it drop. Otherwise the shaft will just stop.
You can make the circuit a bit more complicated by adding a suitable voltage regulator. For example a KR142EN8B or L7812CV.
In this case there is no voltage drop with the drill bit load.
Next, you need to make a fairly accurate design element. a drill chuck. You don’t want to spend money on a collet clamp. any bushing will do. It all depends on the application of the mini drill:
- If you are only going to drill on PCBs, you don’t need to change the drill. So we mount it permanently. The adapter sleeve can be made from anything: A tube from a telescopic antenna, a needle from a medical syringe, a rod from a gel-type fountain pen.
Given the miniaturization of the design, no clamps are needed. Everything can be secured with glue or tape.
- If you want a multi-purpose drill, which includes a drill bit change or other attachments, a universal collet chuck is the better choice.
- You can use a standard jaw chuck by mounting it on the shaft with an adapter sleeve.
The design of the body depends on your imagination. Most craftsmen leave the “bare” utilitarian design: the supply voltage is safe, the size of the motor allows you to hold it in your hands without the housing.
If you want basic aesthetics. there are a lot of options: and they are all conditionally free.
Manual materials for a mini drill with your own hands
There are many alternatives for using your ingenuity to make a mini drill with your own hands. The bases for the creation of such tools can be:
- The drive from a DVD;
- A motor from an old electric razor;
- An electric toothbrush;
- The handle of a glue gun with a suitable motor;
- An out-of-work electric screwdriver;
- Washing machine motor;
- Old hair dryer;
- Plastic tubing.
All these seemingly unnecessary little things can serve you well and become the main detail for creating the necessary tool.
Important! When working with a homemade mini drill, try to keep the drill perpendicular to the work surface. This will keep the drill from breaking and prolong the life of your appliance.
Homemade drilling machine from a Chinese DC motor and “sticks
When making double-sided miniature printed circuit boards at home, it is difficult to do without a high-precision drilling machine. It is especially difficult if you have to drill large quantities of holes with a drill bit about 0.5 mm, so as to keep the alignment of the upper and lower layers of the board.
I did not want to bother much with making a machine, and I did not know if the result would be anything good, so I decided to improvise and did not really bother with its appearance. In the end I got a pretty simple design, suitable for quick replication in almost any condition.
Materials and parts for making
The column
The most important part of such a machine. is the column, it must ensure high-precision movement of the drill without backlash strictly vertically up and down.
Once I found a video on the Internet about the construction of a small CNC machine, well, the role of guides in it was adapted to the design of the gas dampers of the trunk lid of the car. I liked this idea very much, and thanks to it was built this miniature drilling machine.
Warning! The gas stops are under pressure! So they need to be opened with extreme caution.
With time the gas limit switches lose a part of pressure and thus their serviceability and they are sent to scrap, so it is not difficult to find them, for example at some “salvage yard”.
Stops are high-precision hardened rod and body in which it slides. That’s exactly what you need!
In addition to the gas, there is some oil inside the gas dome.
The superfluous parts of the body and rods were sawed off with an angle grinder. I was lucky, in my case everything went without problems, there was almost no pressure in the stops I got.
The final size of workpieces for the columns is: 85 mm part of the guide body and 210 mm approximate length of the rod.
Left the stop valves unchanged, added a few drops of oil to them, and this ensured a smooth downward movement of the console and a slower return upward due to the damping valve.
Column
In this case it is a part that combines the mountings of the miniature motor with a collet chuck and the columns’ mountings.
For simplicity, it was decided to make the construction from a piece of plywood. The motor and the columns guides are fixed by wide brackets, cut out of soft steel profile, without any special fuss. This profile is used in the construction of wall partitions.
The total width of the console was 220 mm, and between the axes of the columns 170 mm.
Vertical stroke of the console was 34 mm.
The motor
Miniature Chinese 12 volt DC motor, ordered from Aliexpress. It was supplied with a chuck and 6 changeable collets of different diameters.
Size of the motor housing: Length approx. 39 mm, diameter 28.6 mm.
The motor is designed to work with 12V DC and consumes 500mA. It follows that the rated power of the motor is 6W.
Stand
This is the rigid base of the machine and the support for the columns, the table for placing the work piece to be drilled and the housing in which the electronic controls of the machine are located.
The frame consists of 4 pieces of wood particle board and a piece of wooden rail, which serves as a support for the console lowering handle.
Frame area size including side panels. 235 x 210 mm.
The only difficulty in fabrication is to drill as accurately as possible two holes in each of the upper and lower panels of the frame, into which the column guide rods will be inserted. The holes should ensure that the column rods are strictly parallel to each other, otherwise the movement of the console on them will lead to jamming. It is also necessary to ensure a strict verticality of movement of the console and therefore the drill.
On the underside of the top panel is mounted engine speed regulator. Button to turn on the motor and the backlight.
The speed regulator board is fixed on the panel with small screws through 3 mm nylon spacers.
Also on this panel are the brackets securing the column stems.
To the bottom of the frame are attached the rubber feet from some old appliances.
Speed regulator, backlight, wiring diagram and power supply
The circuit is very simple and works with 12 volt DC. The motor consumes 0.5A, which means you need a power supply of about 10W for the whole circuit including the backlight.
The speed regulator was ordered from Aliexpress, read more about it in a separate short review.
The on/off button turns off the whole circuit. motor and backlight.
The backlight is made of 4 SMD LEDs and 4 10 kOhm resistors with 1/4 watt power dissipation, mounted on the wall.
The diagram shows a range of suitable resistors from 500 Ohm to 10 kOhm. If you use a 500 Ohm or 1 kOhm resistor, the brightness is not much different, but the 500 ohm resistor is warmer and therefore needs a high power dissipation resistor, like 0.5. 1 W. And the resistors are 1. 10 kOhm can be used 0.25 W.
My choice of 10 kOhm resistors, they let the LEDs shine at about half their power, nothing gets warm and I thought it would be more convenient. The board will not glare in bright light.
With these SMD LEDs the middle contact area is designed to dissipate heat and is a common contact with the nearest to it outermost pin. The resistor lead is soldered to these two pins for reliable hinged mounting.
Arm lift and lowering handle, return springs
The handle is made from a squeegee handle from a construction hair dryer kit.
In the first version of the assembly the handle was mounted on a hinge, but it caused some cramping when lowering the console. Then I added a small jumper to the hinge, which adds freedom of movement of the handle, which ensures the smoothness of the console.
MINI MACHINE FOR DRILLING BOARDS
The need to drill some small holes on the circuit board has recently arisen again. Since there is no suitable drill, I decided to build one that would meet the needs of an amateur radio operator. Since I don’t like to pay for what I can get for free, I built this little machine from what I had on hand. The items to assemble such a drill can be found in almost every stash (or whatever the word stash is declined?) of the radio engineer. For the needs of this project I used:
- 2 old printers (2 guide rods, 1 roller, 1 DC motor),
- old hard drive,
- A powerful 21V power supply,
- 2 old collet chucks,
- Heatsink, some screws, plastic tubing, 2 springs and wire.
And of course various tools: vice, grinder (maybe a file), hand drill, screwdriver.
By the way, it is possible to adapt a hand drill here. Assuming that its weight is about 2-3 kg, you will need to reinforce the construction with guide rods in line with the drill (as shown in the figure).
The base was pre-made, as were the threaded rods that served as guides. I suggest that instead of such a frame a small piece of board Fiberboard 15 x 20 cm (for example, a piece of wooden window sill or some other board). Instead of the strips used here, it is better to take inkjet printers, on which moves the carriage with the heads (they are perfectly smooth and simple, have well-matched guide bushings).
The drill drills freely in PCB, plastic, wood, and aluminum. Later I added 2 more 10 mm LEDs to illuminate both sides of the drilling point, and a metal plate as a washer from the drilled object.
So, with minimal effort, I got a fully functional drill bit for circuit boards. The drill is very stable and drilling precisely because of the shortened drill grip. run-out is out of the question. The only problem is to sharpen the screws that tighten the spindle. Have already filed them down a bit, but it would still be useful. A collection of other designs of drilling machines for boards see on the forum.
Forum for the discussion of the material MINI DRILLING MACHINE
About the use of wireless power technology of various devices.
Review of chinese device for water electrolysis. photos, video, description of operation.
Several working schemes of electromagnetic Gauss Gun. Part One of the Compendium.
Basic information about planar fuses, including their specifications and applications.
Assembly of a homemade device
As practice shows, it is convenient to assemble a homemade machine tool for drilling holes in circuit boards in a certain sequence. Act in accordance with the following algorithm.
- The bed is assembled, and the legs are attached to its underside, if they are provided in the design.
- To the assembled frame the sliding bar and the frame holder, on which the drilling head will be mounted, are fastened.
- The frame of the holder is connected to the shock absorber, which is also fixed to the base of the equipment.
- The control knob for controlling the movement of the drilling head is installed, connected to the shock absorber or the frame holder.
- The electric motor is mounted, its position is carefully adjusted.
- To the shaft of the drive motor, the collet or the universal chuck from the drill is fastened through adapters.
- Assembly of the power supply unit connected to the electric motor by means of electric cables.
- The drill is inserted into the chuck and securely clamped in it.
- The assembled homemade machine tool is tested by trying to drill a hole in a dielectric sheet.
So that your homemade drilling mini-machine can always be disassembled and reworked, it is best to use bolts and nuts to connect its structural elements.
If you want to make your own hands a mini-equipment to obtain the holes in circuit boards you can always use the drawings and tips of those who are already the owner of such a machine and actively works on it in his home workshop.
The design
At first glance, the scheme seems complicated, but this is not so. In fact, the mini machine does not differ much from the classic one, it is smaller in size with some nuances in the layout design scheme.
As this equipment has no large size, it should be considered as a table. Homemade version of the equipment is usually slightly larger than the purchased, due to the fact that when assembling with their own hands is not always possible to optimize the design by picking up small-sized components. But in this case, and homemade machine will have a small overall dimensions and weigh no more than 5 kg.