The chainsaw ignition coil construction
A chainsaw, like any device powered by an internal combustion engine, has an ignition system. It is responsible for ignition of the fuel-air mixture in the engine cylinder. This occurs through the delivery of an electrical discharge, which pierces the space between the electrodes of the spark plug.
It is clear that without ignition no engine will start and will not run. That’s not all there is to it: the chainsaw‘s performance depends on how accurately the ignition is set. In other words. in time or not in time the fuel ignites. That’s why a chainsaw with a knocked down setting needs to be repaired. To fix the problem you can entrust an experienced mechanic, but you can repair the chainsaw ignition with your own hands.
Some Chinese chain saws come with low-quality spark plugs. it might make sense to have a few spark plugs in the kit.In our review we will acquaint you with the structure and the principle of operation of the ignition system, its main malfunctions and ways to fix them.
What is the ignition coil and how to check its functionality
Any ignition coil sooner or later comes into disrepair, so in order to avoid problems in the operation of the car it is better to conduct periodic diagnostics of this element.
In addition to an ohmmeter, you can check the operation of the coil with a multimeter. Below is the sequence of checking this element. After measuring the resistance, you need to compare the reading of the meter with the value specified in the instruction manual of the machine.
Causes of ignition coil failure Helping to choose popular compact SUVs: choose the best SUV for Russia. Find out what is the reason and what to do if the car clutch is stuck. Sometimes ignition coils fail because of a faulty ignition cable.
Gasoline saw ignition repair
Having considered the main types of faults and explained how to check the magneto chainsaw in different ways, you can move on to the main thing. the repair of individual nodes of the ignition system. The following instructions are presented in order of increasing difficulty of repair, but if you already know the cause, you can go straight to the breakdown of the elimination of your particular problem.
Repairing the spark plug
Even a minimal deviation from the fuel mixture requirements or improper adjustment of the carburetor, can be a significant cause of the loss of spark. In the course of operation of the tool, the contacts of the spark plug gradually form soot, an excessive amount of which completely obscures the metal, putting a cross on further work. Detecting such a malfunction is simple. just unscrew the spark plug from its seat.
The best way to clean spark plugs is based on the use of chemicals. For this purpose, a penny dimexide (available at the drugstore) or Cillit BANG (at the grocery store) will do. products). Simply place the candle in an ordinary beaker and fill so that the contaminated contacts are completely in the solution. After 30-60 minutes of marinating, scrub the contacts with an ordinary toothbrush. The use of metal brushes or sandpaper is very likely to scratch the contacts and the ceramic insulator. The scratches, in future use, will more easily settle on the soot, resulting in faster fouling.
The coarse method of cleaning is recommended for extremely heavy carbon deposits, where chemicals alone will not do the job.Except for an excessive layer of contamination, an increased gap between the contacts may prevent spark formation. Strong vibration combined with heat, deforms the side electrode fixing arc, reducing or conversely increasing the distance to the central electrode. Optimal gap for chainsaw spark plugs is 0.5. 0.7 mm. You can adjust the position with a pair of pliers, and use an ordinary plastic card as a template.
Adjusting the clearance between the coil and the flywheel
the constant vibrations of a running engine, have a negative effect on the fixing elements, gradually disturbing the fixation of the related components. One of the first to break the adjustment of the chainsaw ignition, which requires the most accurate position in relation to the handwheel. On average, the distance between the ignition coil and the flywheel should be from 0.2 to 0.4 mm. The exact values for adjustment are usually specified in the technical documentation of the specific saw model, but if such data are not available, it is better to make a gap of 0.3 mm.
You will need a screwdriver with a basic set of interchangeable bits, an improvised spacer (paper or a section from a regular plastic bottle) and blue thread locker (ideally) for adjusting.
First of all we will remove the left side part of the body of the saw that hides all the necessary elements.
We find and loosen screws that fix ignition coil. To be on the safe side, it would be better to unscrew them completely and put a threadlocker on the threads to prevent unscrewing in the future.
Put the spacer between the flywheel and the module. You can use any means at hand: a sheet of notebook (1 ≈ 0), a screwdriver, a screwdriver, and a band saw.05 mm), cardboard from a cigarette packet, a piece of plastic bottle.
Turn the flywheel with the magnets against the coil contacts, between which the spacer is already located. The spacer should be magnetized.Tighten the fixing screws with a little more than average force (without fanaticism).
Remove the spacer and check the rotation of the flywheel. The stroke should be free, without any hint of contact with the coil.
The adjustment process is complete and now you know how to set the ignition on a chainsaw, using a screwdriver and spacer tools at hand. If the coil is good, the spark will definitely appear. Otherwise, you will need to resort to the following instructions.
Replacement of the armature coil wire
When the electrical impulse is lost before it reaches the spark plug. the fault lies in the transmission unit. It is quite possible to repair damaged insulation of a high-voltage wire, but not all places (especially in bends) are realistic to build up without breaking the principle of laying. For situations when repair is unacceptable, the best solution would be to replace the damaged armature wire with a new one.
Chainsaw ignition coil replacement
When all the potential problems have been checked and there is a 100% certainty that the module is broken, then you have to resort to the last resort, but quite relevant option. the replacement of the element. First of all, you need to buy a completely identical part, based on the model of the chainsaw or the serial number of the old coil (if the first option does not fit). There are no one-size-fits-all modules and the choice should be made with the utmost attention to detail. Be sure to take your old spool with you when you go to the store and, if you order online, check the photo and ask the operator if it will fit your chain saw.
Ignition Coil Testing with ohm meter for small engines. Briggs-Tecumseh. How To ~ UPDATED
Features of modern electronic ignition systems
Today’s ignition systems have changed and have features that change the pulse depending on the speed of the saw. Such a “curve” is programmed into the “chip” and helps the saw produce more power, thus the altered pulse gives more time to burn the fuel, thereby getting more energy put into the fuel. In addition to more power, some ignition systems make the initial start of the saw easier.
While ignition systems are making more and more powerful, the components themselves are getting smaller and more robust. These days, failure of a chainsaw ignition coil. a great rarity.
Ignition systems have come a long way in the last ten years, but engineers say new technology will spur even greater improvements in the coming years.
I hope this information will help you troubleshoot your saw’s ignition system. If you were not able to fix the failure, we are always happy to see you in our workshop. We offer only quality chainsaw repair. Phone number of our workshop 8 (499) 390-93-49
Recommendations for checking
Many novice car enthusiasts are interested to know how to remove the ignition coil, because it is necessary to carry out the procedure with the disassembled device. It is also worth knowing about the main types of problems that arise during the operation of this module.
Basic malfunctions
In older machines, it is quite easy to find the device, because it was installed in the field of visibility of the motorist. If you start your search with the center conductor of the ignition distributor, there is no problem. You can also quickly find the individual coil, most often located above the spark plugs.
However, in some models, there may be difficulties with their removal, as first you need to dismantle some of the elements of the power plant structure. Thus, first of all, you need to determine the location of the desired element, and then understand how to check the ignition coil with a tester.
Among the main signs of malfunction of this module should be noted:
- there is no spark and the engine cannot start.
- The power plant is tripping during operation and it is especially noticeable in high humidity.
- During computer diagnostics, ignition skips in some cylinders were detected.
- Decreases in traction are observed when pressing the gas pedal pedal.
- The powertrain has difficulty starting “at idle” and especially in cold ambient temperatures.
- Serious overheating of the device is observed.
- The conductors to the device have changed color.
Often the owners of vehicles are partly to blame for the problems with this element themselves. Wishing to save money, many people decide to use unusual spare parts. If we talk about the most common malfunctions, we can note:
- Battery polarity reversal.
- Frequent overheating of the coil.
- Shorted electrical wiring.
- Mechanical damage to the device.
- Sharp temperature fluctuations.
Carrying out diagnostics
It is necessary to get acquainted with the information about how to test the ignition coil multimeter, because this information will be useful to all owners of mechanisms, equipped with gasoline power units. This measuring device allows you to monitor the voltage and resistance. It is necessary to set the switch of measuring device in position “200 Ohm” and, putting the feelers to contacts “K”, measure the resistance value of the first coil winding.
It should be in the range of 0.2-3 Ohm. In the next step the multimeter switch should be set to “20 kOhm” mode and the resistance between the central contact of the high-voltage conductor and the “K” terminal should be checked. The device in such a situation should show a resistance of 2-4 kOhm.
Tandem coils are often difficult to diagnose as the primary winding is connected to the connector. To test it, you can use a multimeter only if the user is familiar with the circuit of the coil. Diagnostics of the secondary winding is performed between the two high-voltage conductors.
Without a certain set of knowledge in the field of radio electronics, it will be quite difficult to determine the fault of individual coils, as it is necessary to assemble the circuit diagram. However, there is one way that always works. If the power plant is tripping, you should start disconnecting the coil terminals in sequence while the engine is running.
If after that the engine began to double, then there is no spark in this cylinder. To solve this problem, you can also carry out computer diagnostics. But even if the number of the cylinder without spark is indicated during the test, it does not allow you to unequivocally say that the coil is faulty. Knowing how to check the resistance of the ignition coil with a multimeter, you can quickly determine the source of the problem and replace the failed element. Many motorists change the branded coils on foreign cars for devices from VAZ, as they cost much cheaper.
Recommendations for the test
Many beginners car enthusiasts want to know how to remove the ignition coil, because it is necessary to carry out the procedure with the disassembled device. It is also worth knowing about the main types of problems that arise during the operation of this module.
Main faults
In older cars, it is quite easy to find the device, because it is installed in the field of vision of the motorist. If you start the search with the center conductor of the ignition distributor, there is no problem. You can also quickly find and individual coils, most often located above the spark plugs.
However, in some models it can be difficult to remove them, because first you have to dismantle some parts of the powertrain structure. So, first of all, you need to determine the location of the desired element, and then understand how to check the ignition coil with a tester.
Among the main signs of failure of this module should be noted:
- No spark and the engine cannot start.
- The powertrain has a tendency to stall during operation, which is especially noticeable in high humidity.
- During computer diagnostics ignition skips in some cylinders were detected.
- Declines in traction when pressing the accelerator pedal are observed.
- the power unit is difficult to start “at idle” and first of all, when the air temperature is low.
- Serious overheating of the device is observed.
- The conductors that come into contact with the device have changed color.
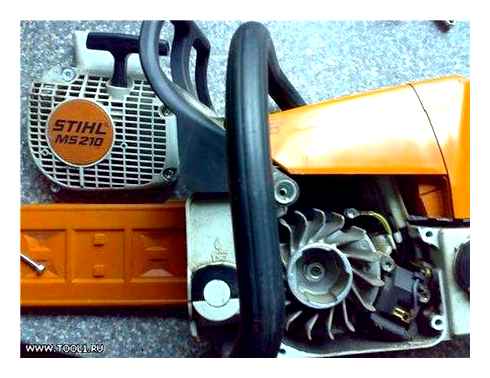
Often the owners of vehicles are partly to blame for the problems with this element themselves. Wishing to save money, many decide to use non-standard parts. If we talk about the most common malfunctions, we can note:
- Re-polarization of the battery.
- Frequent overheating of the coil.
- Shorted electrical wiring.
- Mechanical damage to the device.
- Sharp temperature fluctuations.
Carrying out diagnostics
It is also necessary to read the information about how to ring the ignition coil with a multimeter, because this information will be useful to all owners of mechanisms equipped with gasoline power units. This measuring device allows you to monitor the voltage and resistance. Set the switch of the measuring device to “200 Ohm” and, applying the feeler gauge to the contacts “” and “K”, measure the resistance value of the first coil winding.
In this case, it should be in the range of 0.2-3 ohms. In the next step the multimeter switch should be set to “20 kOhm” mode and the resistance between the central contact of the high-voltage conductor and the “K” terminal should be checked. The device in this situation should show a resistance of 2-4 kOhm.
The most frequent difficulties arise in diagnostics of twin coils, because the primary winding in them is connected to the connector. To check it, use a multimeter only if the user is familiar with the coil circuitry. Diagnosis of the secondary winding is carried out between the two high-voltage conductors.
Without a certain set of knowledge in the field of radio electronics, it will be quite difficult to determine the fault of individual coils, as you need to assemble the circuit diagram. However, there is one method that always works. If the propulsion system is tripping, you should start disconnecting the coil terminals in sequence while the engine is running.
If after that the engine started doubling, then there is no spark in that cylinder. To solve this problem, it is also possible to do a computer diagnostics. But even if the test shows a cylinder number without sparking, it is not certain that the coil is at fault. Knowing how to check the resistance of the ignition coil with a multimeter, you can quickly determine the source of the problem and replace the failed element. Many motorists replace the branded coils on foreign cars with devices from VAZ, since they cost much cheaper.
Ignition advance angle
The mechanical device and the factory setting of the magneto ensure the coincidence of the discharge time of the candle with the optimal position of the moving piston. For four-stroke gasoline engines, the spark should happen before the piston reaches the top dead center. this is because the process of complete combustion of the air-fuel mixture takes a certain amount of time. The speed of movement of engine parts is comparable to the speed of ignition of fuel, so the piston from the moment the spark flashes to the moment the burning gases create an extremely high pressure has time to travel a certain distance.
There is an ignition advance angle for each engine. it is equal to the crank angle, expressed in degrees, from the moment of breakdown in the inter-electrode space of the spark plug to the moment when the piston is at the top dead center. It depends on many parameters, including engine design and fuel mixture properties.
In practice, when an engine is mass-produced in the factory, no individual ignition adjustment is made for each product, but appropriate marks are placed on the rotating parts, which must be aligned during installation.
When the ignition timing needs to be adjusted? There are basic symptoms of a system malfunction:
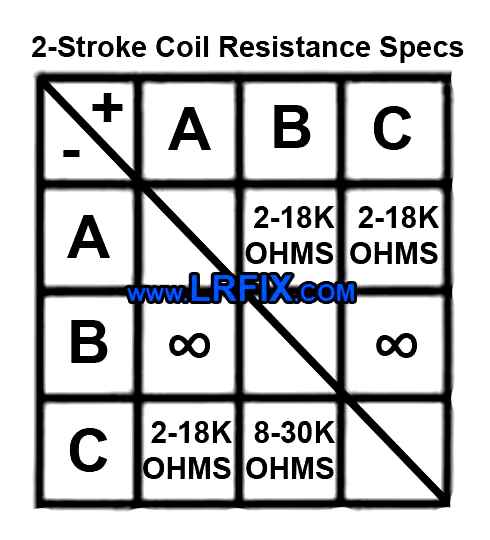
In these cases you should not rush to a service center. Try and adjust the ignition yourself first.
How to readjust?
Of course, the chainsaw is under a lot of pressure when it comes to its engine. Its most vulnerable part is the ignition coil. Small problems can be solved by yourself, for example, to adjust the ignition.
- you want to extend the life of the saw. for preventive purposes;
- the chainsaw does not start, the problem is detected in the size of the gap (for each model, the manufacturers have written their own size of the gap, the average figures are considered to be the parameter from 0.2 to 0.4 mm);
- The engine is faltering;
- the power of the tool is reduced.
In domestic conditions we can adjust the ignition coil gap, which in many cases solves the above-mentioned problems.
Algorithm of setting the gap
To adjust the gap in the ignition coil of a chainsaw, you will need: a template for adjusting the gap or a dipstick (most often a homemade blank is used, for example, a piece of plastic bottle or cardboard), a socket wrench of the required size.
All models have the same coil structure, only the manufacturer’s recommended gap dimensions may differ. Let’s look at the clearance adjustment algorithm for one of the most popular and recognizable chainsaw models. the STIHL 180.
STIHL MS 180 chain saw ignition. A. coil and magnets on flywheel, B. contact location, C. flywheel.
And let’s take everything you need and cut out a strip of unembossed plastic cylinder to serve as a template. The optimum gap for the STIHL 180 chain saw is 0.2 mm. (depending on the model this value may vary from 0.2 mm to 0.4 mm). Next, perform the following sequence of actions:
- Let’s remove the protective cover;
- Let’s take off the module with the spark plug and the high-voltage cable;
- Unscrew the ignition bolts to loosen;
- Let’s bring the magnets located on the flywheel to the coil;
- Press a plastic strip between the flywheel and the coil. By doing so, we set the necessary gap;
- Let’s tighten the bolts and remove the strip of plastic;
- Let’s check: let’s turn the handwheel several times in a full rotation, make sure that the movement was free and the handwheel did not cling to anything.
the smaller the gap, the stronger the magnetic impulse coming from the flywheel where the magnet is located, the stronger the spark will be.
The procedure for adjusting the ignition coil gap will be the same for all brands. However, it should be noted that a distinctive feature of chainsaws made in China is a frequent failure of electronic ignition units and the loosening of the threaded fasteners due to poor-quality assembly.
Consequently, you will have to adjust the gap about 3 times more often than, for example, with the same “Stihl”. It is also worth noting that often Chinese-made saws are supplied with low-quality plugs. It makes sense to have them in advance.
Ways to test the ignition coil with a multimeter for basic faults
The ignition coil is an integral part of the vehicle’s starting system. It is not possible to start the engine without it, but it is possible to start the engine without the battery, which also plays an important role in the formation of the first spark. The ignition coil is constructed quite simply, but even it can be defective if the vehicle has various malfunctions or a factory defect. The ignition coil’s work is not limited to starting the engine, and if it fails when the engine is already running, it will bring it to a complete standstill. Checking the ignition coil with a multimeter is a sure and easy way to determine if the unit is working properly and if it needs to be replaced.
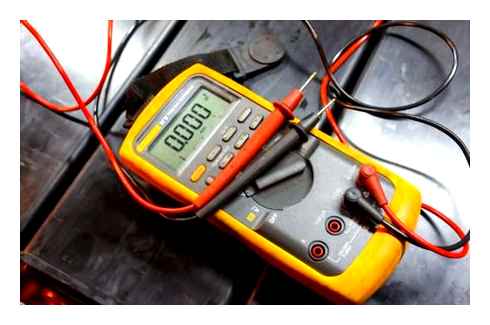
How to check the ignition coil
Checking the ignition coil is a three-step process that begins with preparation, followed by visual inspection and ends with instrument testing. The unit can be checked on specialized diagnostic benches at dealerships or professional services. Self-checking of the ignition coil is done with a multimeter. a universal diagnostic device of wide application.
Preparatory stage
Before proceeding directly to the diagnosis of the ignition coil, it is necessary to get a multimeter (capable of determining the voltage and electrical resistance, ohms) and find the technical documentation for the car. Various ignition coils are installed in cars, and the parameters of a particular model are prescribed in the “passport” of the car. If the car was bought “from hand”, the technical information about its aggregates can be easily found on the Internet.
The parameters of the ignition coil, necessary for its diagnostics, are the resistance of the primary winding and the resistance of the secondary winding. If you could not find them, you can rely on the general figures, which will be discussed below, when testing the element.
Visual inspection of the ignition coil
The appearance of the ignition coil may vary, depending on the model. It has characteristic details. housing, cover, two contacts and the central terminal. During visual inspection, it is sufficient to look closely at the housing and look for chips, cracks or burned areas. The body is made of ebonite and it does not conduct current, in most cases the malfunction of the coil is due to internal damage.
Checking the ignition coil with a multimeter
Diagnosis of the electronic engine control system and the electrical circuit of the tramplate
The ignition coil is located in the ignition coil, and to check the voltage you must bend the ratchet lock and remove the wires that fit it. Next, you need to take a multimeter and set the parameters on it for measuring the voltage. After that, one of the wires of the multimeter is attached to the terminal of the ignition coil, and the second to the car body (that is, to the mass).
The result of such measurement when the ignition coil is functioning should be 12 volts, displayed on the multimeter. If there is a problem with the engine controls or the starter box circuit, it will read 0 volt.
Check the secondary winding for open circuit
In order to carry out such a diagnostic procedure, it is necessary to set the multimeter to electrical resistance (Ohm) measurement mode. Next, connect one of the diagnostic device wires to the positive or negative terminal of the ignition coil, and the other to the central terminal.
If you get a value of about 6-8 kohms as a result of the measurement, it is considered normal for most coils. Some may give values up to 15 kOhm, which is also considered acceptable, but it is better to clarify this parameter in the vehicle’s technical documentation. In the case when the deviations of the measured results are serious in relation to the figures indicated in the technical documentation, it is possible to speak about a breakage in the secondary winding.
Check the primary winding for breakage
Ignition Coil Testing with ohm meter for small engines. Briggs-Tecumseh. How To
The procedure for diagnosing the primary winding of the ignition coil is virtually the same as checking the secondary winding. Again take a multimeter, which has a mode of measurement of electrical resistance, and connect its wires to the positive and negative terminals of the ignition coil, that is, to the external contacts (in most cases).
If, as a result of the measurement, the multimeter shows values of about 0.5-2 ohms, then there is no problem with the primary winding and it works in normal mode. When the resistance differs from these values, the fact of breakage of the primary winding is stated.