How to drill a hole in the wall. practical tips for different materials
Drilling large holes is not a problem if you choose the right tool. For example, carrying out such work may be necessary to fix a channel or metal angle. The easiest way is to use an electric drill, but it takes a lot of effort to get a hole 15mm in diameter, for example. To drill a large diameter hole in metal, special devices and core drilling technology are used.
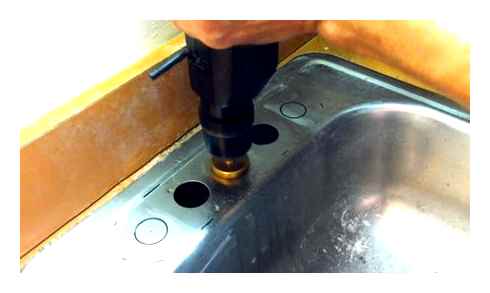
The following basic tools and equipment are used for metal drilling.
- Domestic and industrial drills.
- Holders for them that rigidly fix the tools and enable smooth and accurate feeding.
- Handheld drilling machines.
- Stationary machines for metal drilling (vertical and horizontal types, deep hole drilling, etc.).).
- Various metal drills.
Photo : Portable drilling machine ECO.50-T on magnetic base
Metal drilling techniques used in the home
Three techniques are used at home to drill holes in metal. Workpieces and sheets are clamped using clamps and vices. Household drills and twist drill bits are most often used in the home.
Traditional drilling
This is a metal drilling technique that everyone is familiar with.
- Marking takes place.
- The hole is marked out with a hammer and punch.
- The workpiece is clamped in a vice or using a clamping clamp.
- Insert the drill bit with the required diameter in the chuck of the drill and clamp it.
- The tool is centered.
- A through hole or a blind hole is drilled.
Picture : drilling metal at home
Reboring
Metal drilling is the technique of enlarging the diameter of a previously made hole. This is made by using drills with larger diameters.
At home, the holes usually have to be drilled in stages, gradually increasing the diameter of the tools used. This is due to the fact that the power of a household drill in many cases is not enough to drill holes of large diameters in thick workpieces. In addition the stepwise approach reduces the axial pressure on the drills. This considerably reduces the probability of breakage.
Image : The principle of drilling large diameter holes in thick metal at home
Reducing the diameters of the deeper parts of the holes
In this drilling technology, first drill a shallow hole of large diameter, and then use smaller tools. The technology looks like this.
Image : Technology for reducing hole diameters in metal
How to make a big hole in metal?
Today, every home craftsman has the necessary tool for cutting metal, drilling, stripping. But what if you need to drill a hole with a large diameter?? After all, the maximum cross section of an ordinary drill bit for a manual electric drill is only 20 mm.
There are several ways to drill a hole with a diameter greater than 20 mm. Special devices are used for this purpose:
- Cone drill. It is not possible to drill a large number of openings of the same size. But for home use it is quite acceptable. Maximum cross section up to 40 mm. The thickness of the processed metal is 5-6 mm.
- Stepped cone drill. convenient to use, because each step is formed by a smooth spiral transition. When drilling, it makes it easy to trace the actual diameter of the hole. It can be used to drill circles up to 40 mm in diameter on metal up to 6 mm thick.
- Bimetal bits. suitable for preparing holes up to 109 mm in steel products up to 5 mm thick. It is strongly recommended to use specialized cooling and lubricating compositions to ensure maximum service life of the cutting tool. You also need an adapter to mount the tool on an electric drill. On average, a bimetal drill bit can be used to drill 5-20 holes. depending on its quality, which is accordingly reflected in the cost.
How to drill a big hole with no extra cost?
For this method you will need a drill with a small cross section (5-6 mm is enough), and a cutter or used scraping wheel (corresponding to or slightly less than the diameter of the hole) for the angle grinder. The option is more labor-intensive, so it takes considerably more time.
On the metal workpiece with a pencil outline 2 circles:
- 1. for the future hole.
- 2. depends on the cross section of the drill bit, i.e. if you use a 6 mm instrument, the diameter of the planned circle will be 6 mm less than the previous one.
On the 2nd circle it is necessary to chisel 2 places in opposite places and drill a hole with a 6 mm drill bit. Step back about 3 mm from the obtained openings along the marked line and re-drill the places for drilling. Holes are drilled along the contour of the entire circumference. If necessary, the remaining areas can be chopped off with a chisel.
The hole will be jagged, so it must be bored out. This can be carried out with an electric drill and bit, but much more conveniently with an angle grinder using scraping abrasive wheels of suitable diameter. Use a grinder to quickly and accurately bore the hole to the required diameter.
Therefore, do not throw away spent grinding wheels for angle grinder with a diameter even less than 45 mm. they can always be useful at home.
Homemade drill bit
It is not necessary to buy an expensive drill for the work, in some cases it can be made at home. The rod made of cobalt and tungsten alloy is best suited for this purpose. the victor. Such a rod is easy to recognize among other iron: it will not be amenable to cutting with a metal blade. Next, do the following:
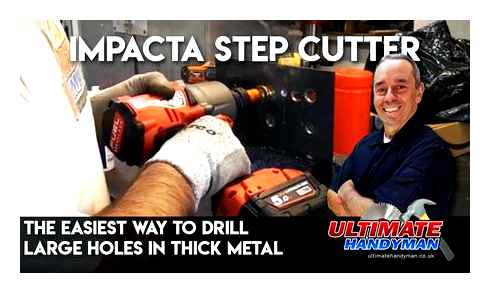
- Set the diamond wheel on the emery wheel.
- Flatten one side of the rod and grind slits on this side, as on a flat screwdriver.
- Grinding down the sides to achieve a sharp cone.
Dear visitors, share your suggestions in the Комментарии и мнения владельцев, how else you can drill a hole in steel, which has been subjected to hardening.
Drilling through thick workpieces
Not many novice craftsmen know how to drill a hole in metal of great thickness. Deeper drilling is more difficult than normal. It is drilled in production using lathes. The workpiece is then clamped in the sliding spindle, which rotates it.
If there is no possibility to use industrial equipment, you can drill a deep hole with a drill. You need to buy special guides for power tools. In addition, machine oil is required for cooling. During the work, you need to stop from time to time to clean the chips and let it cool down.
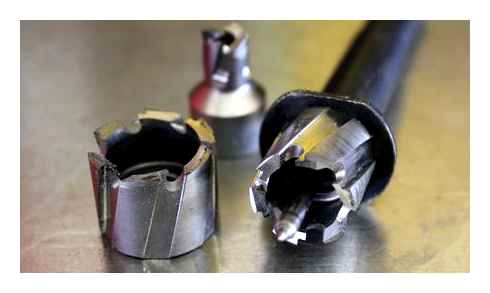
Devices and technology of core drilling
Drilling large diameter holes in metal is not particularly difficult, provided that the tool is chosen correctly. Suppose you need to carry out a similar procedure to install a channel or a metal angle. Of course, you can use an electric drill, but if the hole must be, for example, 15 cm in diameter, such work requires considerable effort. Therefore, to obtain large holes in metal, core drilling technology and the corresponding devices are usually used.
The tapered or stepped cone bit must have a smaller diameter than the required hole.
Metal core bit
Large holes in metal, plastic, wood, etc. п. Diameter from 19 mm to 102 mm. it is easy to make with a bimetal core bit from Hilti.
These crowns have proven very useful for drilling large numbers of holes for fittings in metal cable ducts (metal thickness of 2 mm).).
A clear plus is that the crown is demountable. If the pilot drill bit gets blunt or breaks,
But for each diameter is necessary to use a separate tooth, which costs (depending on diameter) from 400 to 1200, and add 1000 for the adapter.
Read also: Is it possible to cut insulating glass units
How to drill a large hole in metal
Making large holes is a laborious task. Special core bits of appropriate diameter or taper drill bits should be used for this kind of work. Metal drill bits are similar to their concrete or drywall counterparts.
They can have a special diamond coating for a clearer, cleaner and faster cut. Special tapered drills are often used for the work (can have hexagonal or cylindrical shanks). The cutting edge can remove burrs and shavings, making the hole straight at a glance.
How to drill with an electric screwdriver?
Drill metal workpieces can be drilled not only with industrial equipment or an electric drill, but also using a cordless electric screwdriver. This power tool has low power. Because of this it is suitable for drilling holes of small diameter and depth.
Drilling is performed with industrial equipment and power tools. It is important to choose the right tooling, and to consider the depth, the diameter of the hole. Coolant should be used to keep the tooling in place for longer periods of time. Drilling should be perpendicular to avoid damage to the workpiece, tool.
Drilling, boring, reaming on lathes
Lathe. a universal machine for a variety of work with rotating workpieces. Therefore, it can also be used for various hole machining: drilling, reaming, reaming, countersinking, countersinking, etc. To simplify the work on a lathe, use special equipment. CNC (numerical control). CNC-equipment installation is possible on various types of lathes. For this purpose, both screw-turning and carousel lathes, revolvers and other types are suitable. Also with the help of CNC machines can be made drilling.
Drilling process on the lathe
Countersinking is increasing the diameter of the hole with a countersink, and countersinking is machining its edge with a countersink.
Types of drilling on a lathe
Conventionally, there are three types of boring process on the lathe by the degree of human intervention:
- Manual. This method involves feeding a cutting tool into the cutting zone with the rear headstock flywheel, driven by human muscular force.
- Mechanical. In this type of hole machining, the drill is fed mechanically from the slide to the tailstock through a special device. Not all lathes have such devices and, accordingly, the ability to perform mechanical drilling.
- With CNC control. Full automation of product processing is possible on CNC machines. On a CNC lathe, it is possible to machine holes in different ways and with different tools without human intervention.
Drilling and reaming on a lathe
To create new holes in a workpiece or change the dimensions of old holes, the following types of operations must be performed on the lathe:
- Align the tailstock so that the axis of the quill coincides with the axis of the spindle.
- Clamp the workpiece in the headstock chuck so that it projects over the level of the jaws as little as possible.
- Install a cutting tool in the tailstock quill. If frequent changes are expected, it is better to use a quick-change chuck and a set of special bushings. This helps to significantly reduce the time for tool changes. When using a quick change chuck, all drills, countersinks, reamers, etc.д. all drills and reamers should have identical Morse taper numbers. The quill at the beginning of the drilling operation should be pulled out of the tailstock as little as possible.
- The first operation is to prepare the face of the workpiece. It must be level. This is done by undercutting the face with a cutter.
- Make a small depression in the face of the workpiece. This operation will help to make drilling exactly at the point of rotation of the workpiece. This is carried out with a thrust chisel or a short drill.
- Drill with the tailstock handwheel. Feed the tool smoothly. Periodically move it out of the cutting zone to free it from chips. Cool the cutting zone with a special emulsion.
- For through machining, you must reduce the feed rate at the exit of the workpiece, in order not to damage it when the load on the cutting edges rises sharply.
- To increase the diameter of holes, you need to: install a drill with a larger diameter and make reaming; use a countersink. to make countersinking; use a boring cutter. to make boring.
- To reduce the roughness. use a reamer (process. reaming).
- To work with edges. use countersinking (process. countersinking).
When working with cast iron a small chip is formed, which, when liquid cooled, clogs the channels for its removal. Therefore emulsion should not be used in such cases.
All of the above processes can be performed not only by laborious manual methods, but also by taking advantage of the possibility of connecting a mechanical feed to the tailstock or the use of CNC. If the cutting processes will be carried out using CNC lathes, all the tools are fastened at the beginning of the preparatory process in special devices, which are changed automatically in a certain sequence.
Deep hole machining
In the case of deep holes, it is necessary to perform all preparatory operations in the same sequence as for normal holes:
- Setting the alignment of the tailstock and spindle.
- Workpiece clamping.
- Preparation and installation of cutting tools.
- Torquing the workpiece.
- Deepening the face of the workpiece.
A few guidelines should be followed in doing so:
- Deep drilling must begin with a short tool to a depth equal to the diameter of the drill bit, and then change to the main tool. This will help to avoid deflection of the main drill from the correct direction.
- At the beginning of cutting in order to increase the rigidity of a long drill bit, it is supported from the side by the reverse side of the cutter fixed in the cutter holder.
Deep hole drilling causes significant thermal and mechanical stress on the cutting tool because of the larger area of the rubbing surfaces. Therefore, more attention must be paid to cooling and timely removal of chips from the cutting zone.
Features of CNC machines
CNC (computer numerical control) can be used when working on a lathe. This is only advantageous when producing large batches. Because debugging and adjustment of such machines is time-consuming, special programs need to be created and qualified operator-adjuster is required.
Advantages of using CNC machines:
- Relieves the operator (turner) from any calculations.
- Greater accuracy in machining parts.
- The human factor is minimized.
- Increased safety at work.
- Increased productivity.
- Round-the-clock availability and no days off.
- Reduces unit manufacturing costs.
Deep hole drilling
High quality requirements to deep holes and necessity to increase productivity of drilling operations determines the use of special cutting tools and unique mechanical machining equipment with high technological capabilities in manufacturing products for nuclear power industry. In order to fulfill the deep hole drilling operations in collectors of coolant of steam generators and tube sheets of high pressure heaters for power units of VVER-1000 type nuclear power plants, CNC-controlled specialized high-capacity six-spindle machines by GERMAN KOLB (Germany) are applied. These machines have the capacity to produce high accuracy holes of 10-25 mm in diameter, up to 1000 mm in depth by single-side cutting gun drill and BTA tool system.
For drilling deep holes in the parts such as tube sheets with thickness up to 300 mm, special double-spindle machines with movable portal (designed by SKBARS, Moscow, Russia) are used. Odessa) equipped with SIEMENS CNC (Germany) mod. Sinumeric880ME and diagnostics of cutting tool condition by SANDVIK COROMANT (Sweden) mod. ТМ2000-014. Machines provide possibility of deep holes drilling by single-side milling cutters with diameter of 11-25 mm, BTA system heads with diameter of 16-40 mm, as well as countersinking, reaming, boring of exact holes on exact coordinates, milling on contour with linear and circular interpolation, threading by taps, cutters and milling cutters by “MS-Planet” method. The machines are also equipped with a special device for high-performance processing of holes by means of the T-MAX and Coromant Delta drills. In the scientific-technical center of problem technologies of OGT the works in the field of deep hole drilling dynamics research, study of drilled holes surface layer parameters (roughness, deformation hardening, residual stresses) with the purpose of their influence on the operational reliability of critical heat exchangers for nuclear power plants are conducted.
Original techniques and equipment for examination of technological residual stresses, providing high reliability of measurement, are developed. The plant specialists have developed devices, allowing to produce deep holes on radial drilling machines of 2M587 type. On the basis of analysis of deep drilling tools designs of the leading tooling companies: SANDVIK COROMANT, GELLER and VOTEK (Germany), JSC “Sestroretsk Tool Works” (Russia) the specialized tooling design bureau of JSC “ZiO-Podolsk” in cooperation with GNTS TSNIITMASH (Moscow), JSC “Sistroretsk Tool Works” (Russia) and the Russian Research and Design Institute of Machine Tools (Moscow). Moscow) developed a range of original high-performance and technologically advanced tools: single-side drills for drilling holes of 8-25 mm in diameter, heads of BTA system of 16-40 mm. Some designs of special tools and their methods of carrying out especially difficult operations are protected by inventor’s certificates and patents.
Metal drilling 11.04.2022 spraying in a short time
Our turning shop is located at 26c2 Eletskaya Street. You can see a picture of our machines. We employ qualified turners.
We are always online you can call us at 8 (499)380-63-37 or send an email to info@cmetall.We will make an estimate in the shortest possible time
We give a guarantee on all kinds of work you order from us. We value our reputation. You are required to provide a complete drawing or 3D model. And we will make your order the best.
Metal drilling
Drilling deep holes | From 50 ₽ |
Large hole drilling | from 70 ₽ |
Vertical hole drilling | from 35 ₽ |
Suitable materials for machining in our company: Steel Aluminum Copper Cast iron Stainless steel Titanium Brass Bronze Other alloys
We also drill holes in the following parts of steel, copper, aluminum, titanium and other different materials
- Machining of bushings
- Turning the bearing housing
- Lever making
- Turning a housing cover
- Turning a pin
- Axle machining
- Making spacers
- Turning: rings
- Making washer
- Making a part: the finger
- Turning: lids
- Plate making on a lathe
- Turning: disc of an electric clutch
- Drive axle fabrication
- Making cup
Drill bit grades for hardened steel
Drills for hardened steel, if we take from the most suitable old Soviet ones, are the tools based on P18 steel. The tooling has up to 18% tungsten, making it highly durable, not prone to overheating and rapid wear. With these drills you can work at high rotation speeds of power tools. Metal produced until the 70’s is a very rare tool. Steel grade Р6М5К5 is a material of domestic production, where tungsten is less, only 6%, but its lack is compensated by cobalt element in the alloy (up to 5%). Cobalt also contributes to tooling hardness, the ability to withstand high thermal loads for a long time while working with hardened materials.
Among the foreign counterparts of high-speed steels suitable for the production of drills for hard metal, it is worth noting the brand HSS-Co. This is essentially the same tool as the previous one, which has a similar composition of the main alloy elements.
SEARCH hard metal drills on AliExpress →
Any ceramic tile drills are also suitable for making holes in hardened metal, but their carbide tips need to be re-tuned.
Calculation of the required piercing force
The quality of the piercing work depends directly on the effort that is applied by the machine. And if the mechanical equipment has to be adjusted manually, for a machine with cnc, this parameter can be entered in the program. The force is calculated by multiplying the four values:
It is calculated in tons per square millimeter. If we compare metals by softness-hardness, the most pliable is soft aluminum (coefficients 0.30-0.50). The highest coefficient of the type of material is stainless steel at 1.50.