What to cut a table-top from an artificial stone
Lack of regular maintenance of the kitchen countertop can lead to the accumulation of persistent dirt on its surface and the formation of stubborn stains. The soap solution alone will not be enough to clean the worktop quickly. The choice of detergent will depend not only on the nature of the contamination, but also on the properties of the surface itself.
There are three types of coating of artificial stone:
Mechanical damage is more visible on a glossy surface, while dirt and stains are more visible on a matte. The color of the countertop also plays an important role.
The surface of dark material is better to clean with special means for composite materials, and tabletops of light shades can be treated with detergents with m chlorine, which has a bleaching and disinfecting effect.
To wash off grease and dirt artificial stone can be both with the help of firm means, specially intended for these purposes, and using proven folk remedies. These include:
- Mustard powder (absorbs and neutralizes grease);
- lemon juice (dissolves tea and coffee stains);
- gel toothpaste (gently cleans and brightens the surface);
- carbonated drinks containing orthophosphoric acid;
- a weak solution of vinegar;
- baking soda.
Rules of daily care of the tabletop
Artificial stone has a fairly dense structure in which there are no microscopic pores, so liquids, dirt and grease are not absorbed into its surface. If you clean the kitchen worktop with an ordinary soapy solution immediately after using it, the dirt will not have time to dry out and will be removed without much difficulty.
For the same reason, you should remove any food residue, traces of liquids and grease stains from the surface of the artificial stone as soon as possible after their appearance.
Regular cleaning of the kitchen worktop should only be carried out with the use of suitable products. It is best to use regular or liquid soaps, dishwashing gels, and other detergents with a maximum of 5% chlorine. Rules of care for artificial stone exclude the use of powder and abrasives, as well as hard brushes and sponges. Another substance not recommended for use is wax, because it forms a noticeable film on the surface of the countertop. At the end of the cleaning process, the countertop should be thoroughly wiped with a dry cloth.
How I made a “stone” countertop
Accidentally came across on the Internet to the instruction on how to make a table top of “cast” marble “by hand”. at home. I read it, I got it. Watched an hour and a half movie that seemed to tell all the nuances.
Ouch, how I rejoiced! To make “stone” countertops for my planned kitchen, spending about 5 times less dough than if I ordered. what could be more enjoyable? Estimated that their cost was close to good quality particle board. So “stone” in any way cooler! There’s nothing scarier than Button, inspired by an idea.
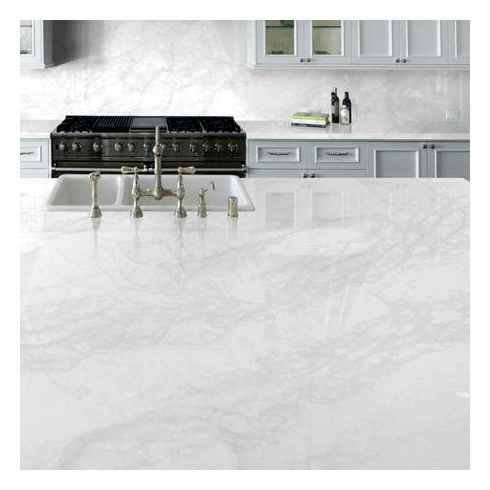
My first idea was to make a dining room table. We have a large family, so the size of 1×1, 5 meters, and I would like to have more, but the size of the living room does not allow. In the event of failure, I reasoned, it could well be used in the gazebo.
The developer of the method promised to send me the ingredients. Googling, made sure that the offered beaujey. And why not? The dude is trying to make money, like everyone else.
Calculated, ordered: 9 kg of polyester resin, hardener, 1.5 liters of gelcoat (it is used as a finishing layer), 9 kg of stone chips of different colors, release compound. Real stone: marble, granite and serpentine, not the ground multicolored plastic offered by most manufacturers. Wow, cool!
I made my first mistake before the process began, due to the ignorance and cockiness of the supplier.
Out of two possible stone fractions, small and large, I chose the small one, 0.5-1mm. But the supplier suddenly clarified that there is no fine white marble, there are 1-3mm. And I agreed to a large. Leaving the size of the granite and serpentine as they were and not buying a special resin filler (microcalcite. I now know that I need it). This resulted in the appearance of the countertop and the consumption of resin. Because, of course, more resin fits between the larger granules than between the smaller ones.
The production of countertops in our high-tech times is put on stream, the technology is mature, it does not require a large expenditure on equipment, but, of course, there must be something. Specifically, a compressor, a spray gun, and a grinder for finishing. It’s not much, if you make tables to order. When making “for myself, my love,” the cost of equipment will be more expensive than if you just go and order ready-made at any firm. But it’s simple. Briefly. We take a base (matrix), for example, fiberboard, sprayed 2-3 layers of plastic chips mixed in resin, dried, covered with a layer of gelcoat (also sprayed), then, after the polymerization process is polished. Voila. The worktop is ready. When making a built-in sink, of course, making the “matrix” becomes more complicated, but the process remains the same.
According to the suggested “garage” technology, the “pie” of the countertop is poured “backwards”. First comes the finishing coat. Gelcoat. applied with a brush, after partially curing, it is smeared with resin and covered with stone chips, which adhere to the surface. Shaking off the excess. Everything is dried, the process is repeated and then the prepared sheet of Particleboard is glued. In the video there was also a sink, and the whole thing was easily removed from the formwork and was almost ready for use. only drill a hole in the sink.
I had a large sheet of laminated chipboard, I intended it for this high mission.
I positioned it horizontally, wiped it clean, outlined the contours of the future countertop
Glued to the double-sided adhesive tape sides from an ordinary plastic corner (my own thought, the video about this is not a word).
Silicone smoothed out the inside corner between the laminated chipboard and the corner. I waited for the silicone to dry.
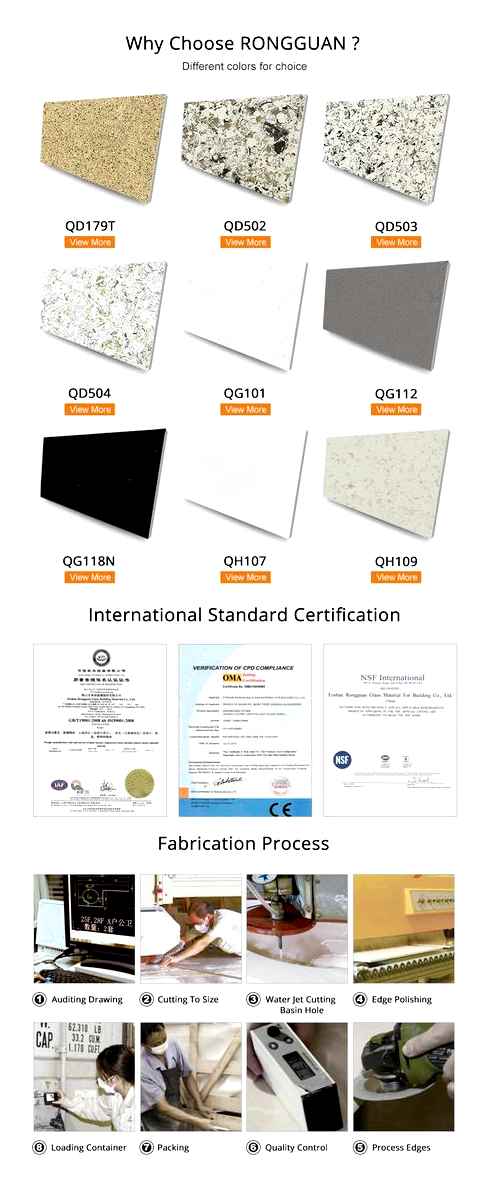
After that, you have to apply blue wax. the divider is wax based. Without it, the gelcoat would stick to the laminated chipboard, and then you can remove the countertop with nothing more than an axe.
And then I made a second mistake. Which, of course, then corrected, but all the fretted with a lot of work. The video uses some tricky alcohol, it’s just applied and smeared. And the wax-based release agent, it turns out, should be properly polished. Had I known in advance what kind of nasty stuff, it would have been better to look for rubbing alcohol. Anyway, I happily smeared the surface with this very wax, and, with some trepidation stirring the gelcoat with hardener, applied it with a brush to the whole mess.
That was the third joint. Although the video recommended to apply gelcoat at the rate of 1 kg per 1 sq. m., really should have done it in two steps. That’s because applying a thick layer of gelcoat evenly with a brush. it’s a challenge. Its consistency is most of all that of a thick, non-fluid gelcoat. When applied with a brush, it leaves streaks, some thicker, some thinner. It doesn’t spread itself, and when you try to smear it, it gets stuck in other stripes. Because of this, on the surface of the finished product is now slightly noticeable, but still visible areas as if with reduced image sharpness.
The gelcoat stinks like a mountain troll’s socks a hundred barrels of paint chemical plant. The fumes are kind of toxic, but I didn’t even have a headache. Having lifted the gate, I left a small slit under it for ventilation and went to bed. This would have been my fourth screw-up, which had some not-so-pleasant consequences. According to the instructions, further manipulation should have been done the next morning: 12 hours. optimal time for partial polymerization of gelcoat.
When I came in the morning I was horrified to find that through a seemingly small crack a neighbor’s cat had somehow leaked in, and, of course, not being embarrassed by the incredible chemical stench, vigorously ran over the freshly applied gelcoat. Smearing it with its paws in all directions.
There were about two dozen such traces, in some places the gelcoat was stripped down to its base, next to. huge knolls.
Rules of sawing
Before sawing, choose a method, as well as accessories and tools.
- duct tape;
- painter’s tape;
- pencil, ruler;
- sandpaper.
- hacksaw;
- router;
- circular saw;
- tire;
- jigsaw;
- sawing machine.
- Dots on the end part of the chipboard. In advance you need to determine what type of cutting will be done. straight or shaped. The technique of sawing they have different.
- Connect the dots in the trimmer fishing line and stick sticky tape on top. Sawing wood chipboard with a laminated surface is desirable with the use of adhesive tape. It will reduce cracks when cutting, since the wood panel is subjected to a lot of pressure with the increase in temperature.
To disguise poor-quality ends use the method of decorative finishing. veneering (gluing the sides). This will not only improve the appearance, but also increase the life of the product.
Only after placing all the necessary tools on the table, can you begin sawing.
Sawing methods Laminated chipboard without splintering
Sawing laminated board needs a special machine (format-cutting machine). But its ) when it comes to using it at home. As an alternative, you can use budget alternatives (hacksaw, jigsaw, etc.), which will take longer to cut.д.), which will take more time when sawing, but will require less cash investment.
With the use of a hacksaw
Sawing with a hacksaw at home is difficult enough. At first it is necessary to cut a line for trimmer with a knife and glue a tape on it. This will protect the top layer from damage. Point the tool at a 30 degree angle. Move the hacksaw back and forth carefully without applying too much pressure. To saw Laminated chipboard without chipping with a hacksaw at home, choose a tool with the finest teeth. In case of damage, go over the place of sawing with a file, guiding it from the edge to the center. To finish, it is necessary to rub it with sandpaper (fine grit) and hide the imperfections under a flexible profile.
Jigsaw
To saw evenly with a jigsaw Chipboard without chipping, you need to choose the device with the minimum size of teeth. It is used for small areas of tiles, moving smoothly without pressure at low speed. If you are using the jigsaw for the first time, you might see some cracks on the back side of the board. With further use, the quality of the cut will improve.
Circular saw
The tool is a table with a toothed disc for chipboard. It is called a circular saw among craftsmen. Cuts through wood with better quality than the jigsaw. Good results without chips are possible by sketching guide lines and securing the circular saw to the board. Chips should not appear at the places where the saw plunges into the board. But the opposite side can be sawed with splinters.
Using a router
Router. power tool, for manual woodworking. Suitable for slotting, shaping, edging and drilling. Before using it, a sheet of wood is sawed with a jigsaw, 3 mm from the marking. Sawing with the cutter should be together with the bearing, which forms the depth of cut to the required level. This is a labor-intensive process that can only be accomplished by skilled craftsmen. High probability of cutting a board awkwardly.
Saws with a panel saw
Place the workpiece on the table and fix it in a fixed position. The necessary markings are made on the sheet and the sawing unit is switched on. When the disc reaches a sufficient speed, the table moves forward with the wooden boards and hits the disc.
Machines for cutting chipboard are divided into 3 types:
- The bed is the fixture on which the entire mechanism rests. The heavy frame adds stability and eliminates vibration. This is important for a quality cut.
- Sawing unit: consists of two flat metal discs. The first one pre-saws the panel, the second one makes a final cut through.
- Work tables. There are three operators involved in the process. The first one is for positioning the assembly, the second one is for feeding the boards to be sawn (movable), the third one is for supporting the sawn parts.
- Carriage. allows the sliding table to move. In this process, the workpiece is held in position by a stop and rulers.
Sawing with undercutting
The process requires a tire. a stop ruler. It is fixed on a board by clamps. Trimming is carried out according to the marks. The bar is set along the line, and the cut is made 10 mm deeper. The second cut is made through. With this method, there will be no chips on either side, as the bottom side of the laminate is already cut.
Liquid acrylic tabletop
Liquid acrylic stone. this is an extremely simple, inexpensive and environmentally friendly material that allows you to make original-looking kitchen countertops. The homeowner can easily buy ready-made liquid material or make it with his own hands.
Countertops of this stone can be made by forward and backward method. When using the direct method will need to make blanks of particle board or sheets of fiberboard, then the “liquid stone” is applied to the workpiece with a gun. The thickness of the material layer is about 2 centimeters. It remains only to wait hardening and spend grinding with the appropriate grinder and manually fine sandpaper.
Using the reverse method of manufacture is more labor-intensive, but it significantly reduces the consumption of material. In this case, you will need to make blanks of fiberboard, which are 5-6 millimeters larger than the size of the future countertop. Such blanks should be glued epoxy glue, then cut appropriate holes for the cooktop and sink, glue on the contour of the blanks of plywood and process them with a grinder.
The completed workpiece is installed in the kitchen, mounted plumbing, after which the existing gaps are plastered with plasticine. It remains only to spray the liquid stone, which is carried out in full compliance with the instructions. The prepared composition hardens quickly, so it is necessary to act carefully and quickly. It is recommended to lay glass fabric on top of the made blank, and then perform spraying. This will ensure the necessary strength of the construction.
Subsequently, the surface is sanded, the edges are milled, and the tabletop, if necessary, is leveled. All such work is not difficult, so to make your own hands a similar piece of interior will not be difficult.
Stone countertop repair
No matter how carefully you use such a tabletop, over time it will have microscopic chips, cracks and other damage. Repair of surfaces made of artificial stone is not difficult, which will restore the original appearance of the kitchen surface.
To fix large chips and cracks you need to degrease the damaged area, slightly widen the crack and fill it with two-component glue. After the glue hardens, the surface is sanded and hand-polished.
Small spots and superficial scratches can be ground with sandpaper. To do this, initially use a sandpaper with coarse grit, gradually moving to a fine grain. You can also additionally polish the surface with a drill and a special felt nozzle.
If you want to eliminate bloating and stains, with the help of a milling machine cut out the defective part, after what the rests of the liquid material is poured the patch. It remains only to wait until the material hardens, perform polishing and buffing of the repaired table top.
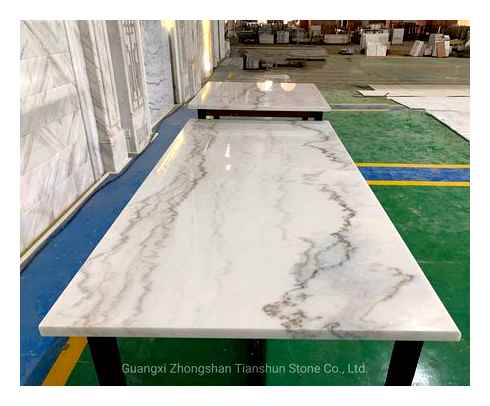
With sheet rock
It would seem that from a sheet of plastic or, as they call it, artificial stone, to make anything is not a problem. That’s how it is. From the sheet cut parts of the desired shape and size, they are glued together. Seams are polished, removing possible height differences at the same time.
A lot of polishing. But it is for any artificial stone
The assembled structure is either glued to a solid base (when the thickness of the stone is up to 10 mm) or make a frame of wood or plywood. It doesn’t seem complicated. Except that:
- A sheet of material weighs a lot, turning it is quite a treat.
- The cuts have to be perfect, so does the fit of the parts. This requires professional equipment and the ability to handle it.
- The joints are glued and fixed with clamps. You put them every 20-30 cm or so. Even for the gradual, unhurried work the number of clamps is about ten.
- You need a good grinder for sanding the joints. You can also do with sanding discs on an angle grinder. But the tool in this case should be with the ability to regulate the speed.
How to beat porcelain stoneware
For drilling faora, as it is very difficult, use a drill with a special nozzle.
It is not easy to drill porcelain tiles, it is one of the most difficult materials to work with. Always start at the front to achieve straight edges. At the exit of the drill may come together, in which case it will remain invisible. If the board you are going to drill is not yet anchored to the floor or wall, put a flat board or a piece of chipboard underneath.
If the diameter of the suggested hole is more than 6-8mm, you should first drill with a tool with a smaller diameter. For work with porcelain tiles it is better to use a peorator or a powerful enough drill.
The drilling speed is low or medium, depending on the diameter of the drill bit. The larger the diameter, the slower the speed. It is better not to use a tup, there is a risk of cracking the plate. In some cases, especially with thicker material, the tumbler is used at low speed if there are no voids under the plate, but everyone does so at their own risk. When drilling, you need to use water to cool it down.
Choice of means
The polishing paste completely fills all micro-cracks and pores of the artificial stone during processing, it prevents dust and dirt from accumulating in them and also gives the surface an aesthetic look.
This compound has a delicate effect on the surface of the stone, does not damage or scratch it, and the special chemical components intensify the saturation of the shade, emphasize the texture and create a thin protective film on the surface.
In order to choose the right tool for sanding tables made of artificial stone, you need to take into account several important criteria.
- The color of the base. the range of colors of artificial stone is very diverse, so going to the store, you need to be well aware of what tints of paste you need. A colorless polish is the universal solution.
- Surface texture. depending on the paste, you can get a glossy, matte or semi-matte countertop. On a matte base is less noticeable flaws, it has little glare, and care for it is not particularly difficult. Semi-matt is also undemanding to care, it assumes a combination of rich color with a slight shimmering shine. Glossy polishing gives a mirror-like surface. It looks luxurious, but any stains and scuffs will immediately catch the eye. Such tabletop will require constant care.
- Distinguish the pastes of increased aggressiveness, which are used for the initial stages of polishing, as well as finishing compositions. One-step polishing pastes are widely available on the market.
Tip: Experienced craftsmen recommend before buying a polish to consult with a specialist, preferably contact the manufacturer of the countertop.
Gypsum stone tiles: textured and structural variations
Stone tile is an elegant and stylish covering, easy to install and perfect for decorative cladding. The tiles are made on the basis of gypsum-polymer components and are high-quality imitation of their natural counterparts.
Example of a stone like gypsum coating
Main qualities and advantages
Decorative tiles have unique properties and characteristics:
- Light weight. it is easier than cement tiles, there is no need to reinforce the base for installation, the elements can be mounted even on plasterboard.
- Thin-layer. allows to save precious centimeters of small size apartments, plus there is no need to fit individual elements together.
- Ease of installation and use. can be laid independently without practical experience and special skills.
- Environmentally friendly. gypsum is a natural mineral.
- Safe for health and the environment.
- odourless.
- Aesthetic appeal.
- A wide decorative range. made under any stone, brick, a variety of textures, patterns and colors.
- Possibility of self-made production.
- Low cost. availability and practicality.
- Lightfastness. the gypsum binders contain modified additives with pigments.
- Hygroscopicity. allows you to regulate the humidity in the room.
- High characteristics of noise absorption and heat insulation.
- Fireproof. suitable for finishing fireplaces and stoves.
- Provides a beneficial, comfortable microclimate in the room.
- The interiors decorated with gypsum tiles are always modern, luxurious and beautiful.
- Large area of application. home interiors, cafes, offices, stores.
- Decorative tile, thanks to its features and qualities allows designers to create exclusive collections of leather, metal, rhinestone elements.
- The covering is easy to cut.
Disadvantages of gypsum products and ways to solve the problem:
- Water absorption. under the influence of moisture the material deforms. To level out the risk, the decorative surface is covered with a specialized water-repellent composition. Acceptable for interior decoration.
- Brittleness, softness and malleability. work with tiles gently, carefully and attentively.
- Low frost resistance. application is limited to dry and indoor areas.
- Difficult to maintain. the embossed surface contributes to the accumulation of dust, for protection is covered with varnish.
Trimming
Gypsum products are easy to cut and machined. The tiles are cut with a hacksaw with a plane or an angle grinder, and the necessary holes are drilled with a drill.
Also, it is necessary to cut the gypsum trim in the joints of walls and floors, where sockets and switches are installed. Curved structures (e.g., arched apertures) require shaped trimming. If necessary, the edge is painted.
To reduce costs and the number of cut tiles, before laying:
Joint expansion
Decorative artificial stone is made with and without banding. Depending on the model chosen, the installation technique is defined. Masonry work with grouting begins at the upper edge of the base, and the vertical joints are not one above the other, but offset. The seamless version starts with the bottom edge.
To seal the gypsum coating, the joints are filled with cement grout or adhesive mortar. Grouting is performed one day after installation, using a special caulk or a construction syringe.

Fill them up to half of the mass. The cavity between the tiles is completely filled with mortar to the full depth of masonry. As soon as the cement mixture has set, use a trowel to remove the excess cement grout.
Then sand the joints with a stiff brush or sandpaper.
The color of the grout is chosen in accordance with the shade of the covering or contrasting, depending on the interior design concept.
Laying
Installation of gypsum tiles is carried out on a prepared, even and dry base:
Acrylic primer is used for a secure bond.
Adhesive composition is prepared, following the manufacturer’s instructions. It is recommended to check the expiry date before application. Mortar sets quickly, so prepare it in small portions. Adhesive types for artificial stone:
- Silicone sealant. provides a high strength of adhesion;
- cement glue. suitable for all types of cladding;
- gypsum plaster. the most preferred for gypsum products, has a white color;
- PVA glue;
- mastic.
- Installation work is carried out at a plus temperature (from 10 degrees);
- Apply a thin layer (5 mm) of glue to the surface in an area for 3-5 tiles;
- The back side of the product is dabbed with an adhesive composition;
- Pressing the element to the base, adjust its position;
- To make the joints even, spacers are used;
- The first row is laid with the construction level.
How to make a gypsum tile
To make gypsum products at home is possible. The process does not require special equipment and tools. For preparation you will need:
The cost of homemade gypsum tiles will be significantly reduced if the plasticizers are replaced by citric acid.
Mix the mixture using a drill or a construction mixer. Prepare mixture of pasty consistency and pour into silicone or polyurethane molds. Plaster hardens quickly, so the mixture is made in portions per pour for the number of molds.
Silicone molds can be purchased in specialized stores or made by yourself.
The mortar is left to harden in the room without air flow at room temperature.
Curing time in the mold is up to 30 minutes, then the tile is removed and left to cure for up to 10 hours. After that, the elements are ready for use.
You can give the desired color to the product in two ways: