Gear and auger lubrication for the Peorator: Proper tool care
Welcome to our website! In this article we discuss how to lubricate the geared motor. Not only does this tool have to be operated with care. It is obligatory to periodically lubricate the gearbox and the chuck.
The gearbox, of course, already comes with lubricant from the factory. But over time, the grease leaks somewhere and dries out somewhere. over, it is designed only to reduce friction, not eliminate it. So one way or another, the parts still rub against each other, resulting in the formation of fine metal dust, which remains in the grease.
As a result of this mixing of metal and lubricant, the properties of the latter are gradually lost and the wear of parts is accelerated.
Inexpensive Chinese rotary screwdrivers may be badly oiled at the factory. The experienced masters of service centers recommend after buying even a new such apparatus to disassemble and lubricate it at once
The cartridge comes dry at the factory. Here, in fact, not the chuck itself is greased completely, but only the place of it that is in contact with the drill bit, because this is where the strong friction occurs, and without reducing it both the chuck and the drill bit shank can be damaged.
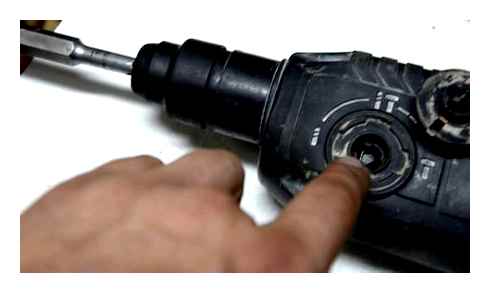
So, below we will consider how and what to lubricate these elements. We will consider the peorator SDS with the horizontal motor location, as it is used in the vast majority of cases by home masters, and the article is mainly written for them.
Huge selection of power tools and gasoline equipment at low prices. Free delivery to your region. Payment on receipt or online.
Why do elements of the torus need lubrication
Lubricant, including that used for the peorator, is a viscous substance, whose use is necessary to reduce the friction coefficient between moving relative to each other elements of the design of a mechanical device. Thus, the grease only reduces friction, but does not eliminate it completely, so the lubricant is gradually saturated with wear products of rubbing parts. metal dust. Not only the viscosity of the lubricant changes as a result, but it also causes more wear and tear on the equipment.
It should be noted right away that viscosity is the most important parameter, which should be considered when choosing a lubricant of a certain type.
Over time, grease becomes contaminated and loses its properties
How to choose proper grease for a certain model of torque converter? In the first place it is necessary to take into account the recommendations of the equipment manufacturer who will certainly indicate both the type of grease required and the frequency of its replacement. It is especially important to follow such recommendations until the warranty period for the torque generator has not expired. Otherwise in case of a breakdown of the device you will not be able to use the warranty obligations of the manufacturer.
Many owners of peorators after warranty period expiration start to use for greasing not branded compositions but their cheaper analogs. lithol or solidol. such lubricants can cause no damage to the drill bit structure elements, but when using them, you have to take into account that they need to be replaced much more often.
What has to be lubricated
In accordance with the instruction manual, the gearbox and bearings inside the rotary tool should be lubricated. Maintenance can be done with your own hands.
Drill shank
Concrete dust is an excellent abrasive material. by penetrating inside, it speeds up the wear of the chuck and bit shank. Before each insertion of the core bit into the chuck, the drill shank is thoroughly cleaned of dust and other dirt and lubricated. Apply “Lithol” on slots of shank. in closed and open grooves, which is evenly distributed along their entire length.
Most tool owners prefer the supplied release agent, but
Many people prefer the classic grease grease or “Lithol. The latter shows good results, but is not without its disadvantages.
- The material is known for its low water resistance. it is able to let moisture to the contact surfaces, which causes corrosion of metal components. Rust accelerates chuck wear.
- The peculiarity of lithol as a lubricant for a peorator cartridge is fast wear and tear. After a dozen minutes of use, “Lithol” turns into machining, its mechanical performance drops, and efficiency decreases.
- Cost. Yes, yes, affordability is the weak point in this situation. If the grease is cheap, it means it is applied without sparing, and in vain. Not a single peorator cartridge has yet benefited from such generosity.
- ready to stop work periodically to replace the worn-out grease with the new one in the volumes recommended by the manufacturer. a drop in each groove;
- Not working and not storing the torch in humid conditions;
- to those who want to save money on lubricants;
- Those, who own inexpensive torch. it is not recommended to save money on consumables for professional models.
If during work, drops of oil fly out of the chuck, it means that it is not designed for high temperature operation, the shank of the tool is too hot, or too much oil is applied.
Gearbox
There are two types of gearboxes. For units with cranked crank mechanism, it is a separate model from the percussion group, with oscillating bearing. implemented by ratchet type.
Gearbox is a pair of spur or bevel gears that transmit the torque to the chuck with the bit. Peorator gear lubricant is generously applied to the teeth of all gears and components of the “drunken bearing” percussion group. To do this, you must disassemble the device, get rid of the used compound, and assess the condition of the mechanical components at the same time to see if it is time to replace them.
Lubricant must be inert to the plastic of which a large portion of the housings, especially inexpensive rotary gearboxes, are made.
The frequency of relubrication of a particular model is indicated in the instruction manual, it depends:
- quality of metal of which the rubbing parts are made;
- the intensity of use of the tool;
- The level of heat of the components;
- Lubricant quality, quantity of lubricant;
- working conditions.
For most inexpensive tools, maintenance is recommended every 200 hours of operation, provided you use good quality lubricant. If the tool is used infrequently, lubricate every six months before use. Any synthetic grease will decompose over time and lose its initial properties.
Before operating in cold and sub-zero temperatures, operate the unit for a minute or two at a low idle speed to warm the grease. thickened grease is not as effective.
Gear and bearing grease should fill about 1/3 of the free volume. If applied more, it will start to heat up, speeding up the aging of the metal.
Chuck
The gator cartridge is not lubricated separately. It is sufficient to apply the compound to the shank of the drill bit or drill bit.
Lubrication requirements
Gearbox and tooling require different oils-the parts work under different conditions, pressures, and temperatures. We recommend to buy formulations created by the drill manufacturers. If your tool is Bosh or Makita, it means you should buy consumable material of this brand, too.
Drill Shank Grease
There are many compounds on the market that are designed for application on the drill shank. They differ in viscosity, but the viscosity is usually thicker than the gear lubricant’s thickness. Compound recommended by drill manufacturer should be used. If you have run out of supplied lubricant for auger shanks, you should buy it from your local dealer.
Gearbox Lubricant
Properly lubricate the gearbox during assembly. As a result of operation, the compound wears down and wears out, so it needs to be periodically replaced. Sometimes dust particles or pieces of metal that have broken off from gears penetrate into it, they become abrasive materials that accelerate wear of parts. The oils used in the gearbox must meet a number of requirements:
- Water repellency. protects parts from moisture when working and storing gears in wet areas;
- operation at high temperature;
- self-repair;
- high adhesion. adhesion to steel surface, formation of oil film between parts;
- inertia in relation to steel. gears are made, plastic and aluminum. housing;
- protecting the metal from oxidation;
- high dropping point. prevents grease from falling down under the action of centrifugal force;
- Containment and removal of contaminants from the parts contact area.
Many professional torches are equipped with a hole for adding grease to the gearbox. Waste oil can be drained out of the unit through these; the hole is sealed with a rubber or plastic plug. These models use liquid grease. The consistency is similar to engine oil, but it is not substituted by oil. It washes the contents of the gearbox, so it doesn’t need to stick.
Repairing a plain bearing
When the bearing in an electric drill fails, the chuck vibrates. The thin drill bits break as a result. The holes made with the power drill are jagged. The bushings are dirty and worn out.
When a dirty bushing on a housing is thoroughly cleaned and well coated with a lubricant, its service life will be prolonged.
But the bearing, which is made of bronze and pressed into the gear disk, usually fails, and has to be replaced.
The sleeve, on the other hand, is replaced with a new one, which is turned by a lathe. You need great precision here. This is difficult to do at home, since it requires skilled use of a lathe.
But to cope with the dismantling of the old worn bearing, and then with the installation of a new one will be able to any owner of an electric drill.
To remove the broken bearing, use a drilling jig that includes bolts, nuts and washers.
The threads will be tapped inside the sleeve when you screw in the bolt. It is very important to choose the correct size bolt. To facilitate this work, try on a vise with a wrench. You will quickly remove the bushing. This can now be sent in as a sample for the turner to make a new part.
Put the new bearing part back in the same way as for the old plain bearing. In order to do this correctly and successfully, it will be necessary to center the part and equip it so that the force is distributed evenly.
Drill a hole in the middle of the mandrel in one axis of the sleeve. Fit a screw with a countersunk head that fits into this hole.
Screw a nut on top of the screw and push the sleeve into the mandrel.
How to Determine Stator Continuity Without Disassembling the Emitter
To determine the integrity of the stator, you must test its windings, measure the winding resistance and insulation resistance.
Stator and rotor wiring diagram
To measure the resistance of the Makita perator winding you need to connect one end of the tester to the freed brush holder, and the other to one of the ends of the plug. If it shows nothing, change the other end of the plug. If the resistance is infinity, the stator is open and needs to be replaced or repaired. Don’t forget, you can’t do without the circuit diagram of the Makita 2450, 2470.
Simple Collector Motor Wiring Diagram
If it shows any resistance, it’s important to measure the exact value. As a general rule, the winding resistance of a Makita 2450 stator at 20ºC is in the range of 25 ohms.
Understand in more detail why armature collector sparking occurs and what brushes are better? Help to understand the video at the end of the video review important tips on selecting brushes
How to remove a Makita 2450 and 2470 stator for accurate diagnosis and repair
To remove the stator you need to.59, remove the brushes, unscrew the four screws fixing the cover of the mechanical block. They are screwed into the endcap. By pulling the black housing and the green one in different directions you can free the housing with stator. The stator is fixed in the green case.
To remove it you should take out the plastic gasket pos.58 and by tapping on the housing face with a wooden mallet or bar. The stator will come out by itself, just pull it out, blow on it and check it finally.
And here is the stator
If you have a short circuit checker you can check the stator for short circuits straight away. The device is called the IK-32. To check the stator windings accurately disconnect the two stator windings from each other via the circuitry. Check the resistances of each winding, they should be exactly the same. If there is a difference in resistance, the lower resistance winding is more likely to have an inter-twist fault.
Checking the stator of a Makita 2470 and 2450 with your own hands Diagnosing the armature, stator with a KZ and homemade
Percussion shaft assembly
First you need to grease the inside of the cylinder pos.32 and insert the striker pos.30.
It remains in the inner housing pos.49 put the lubricated barrel assembly pos.21 in place by putting it on the lubricated cylinder pos.32. As a lubricant, we recommend using a special grease designed for Makita beater. Several types of grease are available: Makita P-08361 and Makita 183477-5 SDS-PLUS. Makita 183477-5 SDS-PLUS grease is recommended for the gearbox. Makita 196804-7 brand grease is used for the drill shanks.
The greases are different colors, but have exactly the same characteristics. Also what kind of grease is used in the Makita 2450 and 2470 peorator?
Here we have the assembled mechanical unit.
Now let’s lubricate all parts of the mechanical unit with the recommended grease. Here is an example of how to properly apply grease to rotating surfaces. Here’s another example of generous lubrication of the mechanical block.
You can’t go wrong with butter
This is also allowed to apply grease. You can’t ruin a thing with butter!
Make sure to cover the lubricated mechanical block with the plastic cover pos.14 black. Laying the housing on top of the assembly, press the housing down until the assembly is fully seated in it. Loosen the four bolts pos.10 into the housing and screw. Now it’s time to attach the mechanical part of the electric motor rotor.
Installing the rotor
The helical gear of the rotor is inserted tightly into the housing of the mechanical block and pressed down.
Remain to insert the four m4×60 self-tapping screws pos.57. and screw them into the housing.
Installing the electric brushes
Remove dirt from the brush holder grooves and put the brushes in place by fixing them with clips.
Now it’s time to check the performance. Plug in the machine, switch on the machine briefly in drilling mode. After making sure that the tool is in working order, turn it off. Set the mode switch to the “shock” position. Do not insert tool. Check that the pelerator works in this position. At the same time you have checked that the mode switch works.
Now you can check the placement of the RPM knob, make sure the pins are securely fastened, and then install the cover on the cover.
Installing the Cover
The cover is fastened with three self-tapping screws M×4 of different lengths.
Connect the furnace to the mains 220Β and check in all modes. Your Makita 2450 or 2470 is assembled and working properly!
How to choose and use grease for your torch. Zuzako Editors’ Note
Check lubrication before switching the unit on again. If necessary, the old compound should be replaced with a new one. When choosing the latter, be sure to follow our editorial advice. They can help you find the best quality product at an affordable price.
Gear Lubricant
Lubricant for the different parts of the gearbox is used to prevent dust and dirt from getting onto the working parts of the power tool. It also helps reduce the friction force, high values of which quickly knock out different gearbox elements.
- Try to buy a lubricant that will protect the metal parts of the gearbox from corrosion. It will allow to avoid rust formation on their surface that will only increase friction and accelerate tool wear.
- Pay attention to adhesive properties when selecting a lubricant. It will determine how long the product lasts on the gearbox, which vibrates a lot during operation.
- Best choose water-resistant greases. They will protect the gearbox from condensation, which often forms on the inner parts of the power tool.
- The grease you choose must be able to regain its properties after you have finished using it. Otherwise, it is only enough for one working day.
Work tool lubricant
The working tool (auger) is under tremendous strain as it rotates in the chuck. To protect it from excessive heat and rapid breakage, a special lubricant is used. It helps reduce friction and prolong tool life.
- We recommend choosing branded lubricants designed for specific brands of torque motors. The grease has the right composition and set of properties to achieve the maximum reduction of friction force.
- Grease should be bought depending on how often you use the power tool. For daily use, formulations designed for long-term operation at elevated temperatures are suitable. If you use your engine once or twice a month, a universal formulation will suffice.
- The grease for working tools should be as thick as possible. Otherwise, when the drill is heated during work, it will simply flow on its surface and provide protection only for a short period of time.
- Before ordering grease for the drill and chuck, be sure to study customer reviews. They will help to learn in advance about all pros and cons of the considered means.
To drill holes in hard materials, it is advisable not to use an ordinary drill with a standard drill bit, but a peorator with a special drill bit. This power tool is indispensable when working at home, in the country house or in the workshops of industrial enterprises. For its normal operation you need a special grease, which you can find and buy in our article. There are the highest quality compositions designed for tools of different models.
Be sure to like it and write a small comment. Also remember to share troubleshooting information on all available social media.
Brush replacement
If the brushes are very hot, the part most likely needs to be replaced. It is advisable to first check the condition of the elements: the replacement is carried out if they are completely worn out. For the procedure you will need a good quality wiring screwdriver.
Disassemble the unit according to the described instructions, and then put new parts in place of the old brushes.
Warning! Some models have a clamping mechanism, so before replacing it will have to be removed.
We recommend applying fresh lubricant to all parts
Troubleshooting
Makita makes tools that are very reliable. However, in some cases there are problems, so you need to know how to deal with it:
- Chuck not turning. This situation is possible in case of damage to the engine or motor. You need to disassemble the product and inspect it carefully. Sometimes the cause may be a breakage of the start button or a short circuit of the coils.
- Drill bit not holding in chuck. In most cases the problem is caused by old parts or a defective cartridge. It is recommended to disassemble the device and look for a solution. Sometimes it is enough to replace some parts with new ones.
- Change of armature. In this case, the procedure is carried out in several steps. First open the cover on the back, remove the brushes, disconnect the gear housing. After cleaning the parts from dirt, replace the armature with a new one, then put on shock absorbers made of rubber and a new air intake plate. Reassemble the gearbox.
- Tool does not chisel. The cause is often found to be either floating bearing failure, or a cracked striker. Both will require replacement of parts.
- Start button replacement. Breakage of the start button requires its replacement. It is necessary to disassemble the device. remove the cover, disconnect the contacts, remove the old button and replace it with a new one. Then assemble everything in reverse order.
- Overheating while using. This situation occurs if the device is used incorrectly. If you have an unpleasant odor, it is recommended to disassemble the device and check everything.
If necessary parts are replaced with new ones
Description Grease for gear reducer 30 gr Makita 181490-7
Buy grease for Makita gear piston 30 gr price, photos, description, reviews at an affordable price you can in the Internet. RotorUA store with delivery in Ukraine.
Reviews (4) Grease for the beater 30 gr Makita 181490-7
Ivanov Mikhail Viktorovich
Stepan
Kvasnikevich Vitaly Mironovich
Ordered parts for a Makita HR2450 on this site. When the order was placed, manager quickly responded. Checked and confirmed that everything is available.I made payment for the order and in a couple of years the order was already delivered by forwarder. All was well packed when you received it. All ordered spare parts are of good and proper quality. I am satisfied with the product. If necessary, I will order again from this online store. Thank you very much ROTORUA.
Burdilny Alexander Grigorovich
Gearbox Lubrication
Gearbox of the torus is the most complex unit by design, so it requires special attention. It is not so difficult to perform lubrication of the geared motor, but it may be quite difficult to assemble the disassembled unit on your own. If your torch is still under warranty, the question of lubrication of its gearbox is best addressed to a specialized workshop that provides warranty service for such equipment.
The detailed scheme of your torotor will help you to understand the mechanism and assemble the tool correctly
If your torch, the owner of which you are, does not fall under any warranty obligations, or the warranty period for your equipment has expired, and the authorized service center is located far enough, you can grease the reducer yourself, taking into account the maximum carefulness and caution. For this you will need:
- A set of locksmith’s tools with which you will assemble and disassemble the geared motor;
- clean rags;
- The compound itself to make the grease.
“Makita P-08361 Native Gear Lubricant. Refilled during initial tool assembly and recommended for maintenance
Better if the lubricant is a brand-name product specifically designed for a particular brand of equipment. So, it can be grease for a Makita torch or grease for a Bosch torch. If you do not have a brand lubricant, and you can not buy it, you can use inexpensive domestic lubricants.
It is very important that you have the instruction manual for the torch that you are going to lubricate. Naturally, if you own a Makita or Bosch torch, it should be the manual for these brands of equipment.
All gear parts should be completely cleaned of old grease
After carefully following the instructions of the Geareducer, you may start the lubrication of the Geareducer.
- Clean dust well before disassembling.
- When disassembling the gearbox, it is advisable to memorize immediately the location of the structural elements in the gearbox. Please note that it is not recommended to disassemble and lubricate the Geareducer immediately after you have finished using it. This is because parts of the gearbox can lose their physical properties if they come into contact with cold lubricants.
- After all the components have been removed from the gearbox housing, they should be thoroughly washed with gasoline or spindle oil and wiped dry.
- The interior of the gear unit housing must also be rinsed and wiped dry (as thoroughly as possible).
- When disassembling the Geareducer you may notice that some elements of its construction are not greased. This means only that such parts do not need to be lubricated and there is no need to apply it to them.
- As mentioned above, it is better to use a proprietary lubricant for the gearbox of the drill or the torch, which is characterized by a number of advantages. In particular, brand-name lubricants retain their original characteristics for much longer, so they can be used much less frequently. over, the branded lubricant is water-resistant and therefore effectively protects the metal parts of the rotary table saw against moisture and thus against corrosion. Metabo oil is a good alternative to brand-name gear lubricants for your rotary table or drill and is reasonably priced.
- After lubricating all the elements the gearbox has to be carefully assembled in the reverse order.
Not only lubricating the gearbox but also applying a lubricant to the drill shank of the used drill bit is part of the maintenance of the torch.
Clean tool shank thoroughly before starting this procedure. After that special grease for auger drills or ordinary lithol is usually used. over, if you have an open chuck installed in your geared motor, it is advisable to wipe its gland beforehand, which will provide better protection of the internal part of the device from dust penetration.
Reasons for overheating
Many DIY enthusiasts have a question about how to use the torch so that the gear housing does not overheat. The cause of overheating must first be determined. One of such causes can be too much grease in the internal part of the gearbox, which also negatively affects the performance of the device.
The reason for the intense heating of the circular saw gearbox may also be the fact that insufficient lubricant is supplied to its internal parts. This can occur when the drill is used for too long in drilling mode.
This hole in the gear housing is periodically filled with grease during operation
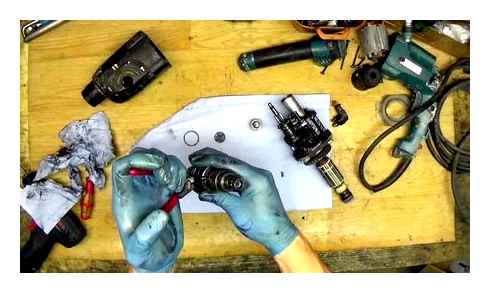
Another common cause of overheating is that the holes that carry cooling air to the motor are blocked. In such cases, the drive unit should be thoroughly cleaned of dust and returned to normal drilling mode for a short period. If you work sparingly like this for about half an hour, the temperature of the gear housing should decrease.
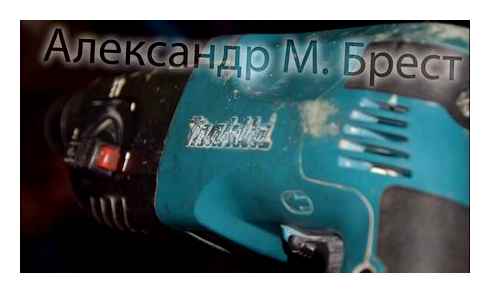
If the tool is properly maintained and all recommendations regarding its use are followed, the gear housing should not overheat under any operating conditions.
How to Grease a Drill Bit
The drill bit lubricant is somewhat different from the gear lubricant. After all, the working conditions in the tool chuck are strikingly different. So it is not surprising that products have a different composition.
- All loads have a variable vector. And they go both in transverse direction as well as longitudinally.
- There is a technological backlash, and it allows the tip to pull away from the surface. And this runs the risk of tearing the oil film.
- Most movements are erratic and multi-directional. And at extreme points, the shock load can completely displace the lubricant.
Dust and debris in abundance on the work site significantly impair working conditions. And in some cases a large amount of moisture. And all of these factors allow the lubricant to keep its performance only for one cycle. Therefore, when you change the tip it is necessary to apply a fresh compound to a new drill.
Severe requirements that drill bit lubrication has, do not allow the use of universal compositions, such as “Lithol. Unless, of course, there are critical situations when you don’t have the right lubricant on hand. over, immediately after a single use it is recommended to carefully remove universal grease from the surface, both from the drill shank and the inner part of the chuck.
Taking into account criticality of working conditions it is better to pay attention to specialized compounds from leading producers of tools. The same Bosch, Makita, as well as domestic Interskol produce compounds that are ideal for chucks and drills. And all products of famous brands guarantee reliable protection of the tool and its components.
The main points in a nutshell
To increase the power tool lifetime, it is necessary to use only quality lubricant. especially for trouble-free work of the torch it is better to choose specialized compounds that the producer bundles his products with. This will ensure that you have the right lubricant components for the model in question.
You can also use products from leading manufacturers of oils and lubricants. Their universal materials are of high quality and not much inferior to specialized products. The only condition in this case is the need to change the oil more often than usual.