Cutting to size and joining kitchen worktops
The problem For the precise and high quality manufacture of the corner joint of the table top. In addition to a special template and router, you need a high-performance vertical router. For the craftsman who rarely needs to join worktops, it is not worth buying this expensive special tool.
In such cases both parts can be cut at an angle and joined together. Using this method, you can easily cut almost any angle on the workpiece. This is particularly advantageous if a joint angle of 90 to 135 degrees is required. Another advantage of this method is that the grain fibres of solid wood or wood veneer panels with a decorative surface finish converge exactly at the required angle. When working with the method shown in fig. 1, the grain fibers of the two workpieces are perpendicular to one another. If the worktop surface has a fine pattern or a stone look to it, even a 90 degree joint is almost invisible. Even so, a perfect fillet joint is more difficult to achieve than a 90° angle joint. The only disadvantage of joining at an angle: the length of the workpiece to make a tabletop 60 cm wide must be 60 cm longer.
You will need the following tool to connect the countertop:. circular saw: e.g. Festool TS 55 R. The Z 48 HW saw blade with fine tooth. FS 1400 or longer guide rail with two threaded clamps. an edge band end cap for the guide rail. router for making the sockets for flat spikes and flat spike sizes. 20. drilling machine and Förstner drill ø 35 mm. router OF 1400 and router bits ø 8-10 mm. worktop connectors. silicone (color: transparent)
Dust extraction must always be guaranteed when working, which is why we need a CTM series dust extractor for industrial applications in joinery and carpentry workshops. The unit can be connected to all Festool hand-held circular saws.
First support the worktop on the trestle or on a workbench with wood under it. the excess material to be sawn off must not hang and must be supported over the entire surface.
Use a pencil to mark the cut trimmer line at an angle on the top side of the countertop. To do this, use a miter saw or large adjusting angle or a small saw.
If necessary, replace the circular saw blade with the fine-toothed blade (48) of the HW version.
If the guide rail’s splinterguard is not yet in line with the saw’s cutting line, first cut through the full length of the guide rail to a depth of approx. 6 mm at 1 rpm
Align the guide rail’s splinterguard precisely in accordance with the alignment marks and secure the guide rail to the tabletop with screw clamps.
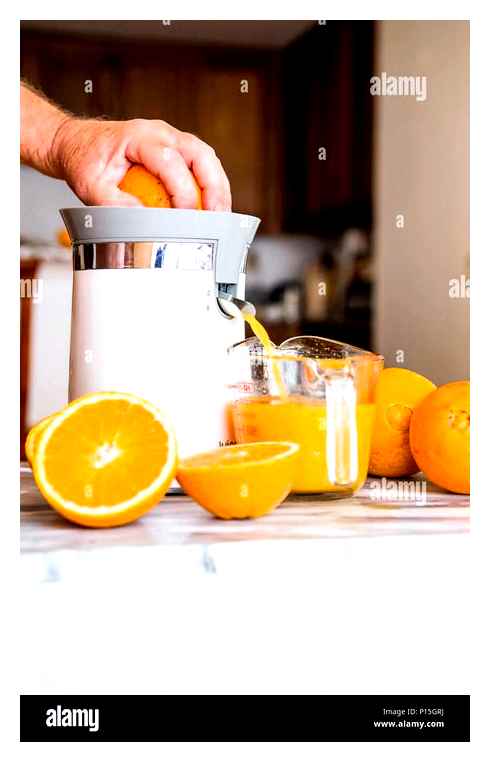
Use a screwdriver (size 0,8 x 4 x 100) to hold the black stop on the saw blade platen in relation to the guide rail and leave no gap.
Set (with a countertop thickness of 38 mm) the depth of the circular saw to 48 mm (t. е. approx. 10 mm thicker than the tabletop thickness).
Set saw blade speed to maximum (6).
Saw a tabletop squarely and accurately with the Festool TS 55 R circular saw with the Festool FS 1400 guide rail. RECOMMENDATION In order to cut a 60 cm wide worktop exactly at an angle, you will need: a Festool FS 1400 guide rail with the appropriate clamping clamp and a circular saw suitable for the guide (e.g. Festool TS 55 R). We recommend the use of an end cap for the buttress as an accessory. It prevents the dust extraction hose and power cable from snagging on the end of the guide rail. The prerequisite for a clean and chip-free cut is the use of the right saw blade. Sawing worktops with plastic coatings and veneered worktops requires a saw blade with fine tooth (48 pieces).) in the HW design. A good splinterguard is necessary in addition to a matching saw blade. When first sawing, it cuts precisely in the cutting line of the saw and the stop bar. This achieves a precise cut on the guide and a splinter-free cut. If the splinterguard is damaged, it must always be replaced with a new one.
On the cuts, use the router to cut four slots on the underside of the worktop and four on the uppermost.
RECOMMENDATION : If the worktops do not match exactly in thickness, the flat spikes must be inserted in the sockets on the top side only, i.e. е. on the tabletop side. This ensures that, at least on the upper side, the transition from one part of the tabletop to the other is not noticeable. The underside, as a rule, faces the cabinet elements, so here the inaccuracies are not visible at all. Although the flat spike can be shifted slightly lengthwise, the sockets of both table tops must be exactly opposite each other.
Tabletop connectors are available in different lengths. In certain situations, longer connectors may be more suitable for mounting. However, the short ones are absolutely sufficient in the standard case. To cut the connectors you will need a ø 35 mm Förstner drill or drill bit for complicated work and a vertical router with a slot cutter ø 8-10 mm.
Using an angle piece, mark out three points on the connectors.
Characteristics influencing the accuracy of the cut
Certain parameters can affect the nature of the cut. When choosing a tool it is worth paying attention to:
- Power level that influences speed and cutting depth. High-powered machines avoid vibrations and bending of the saw blade when working with any material.
- RPM that affects cutting speed. Experts recommend preferring a high stroke frequency if you need to cut soft wood. Low frequency of movement is appropriate for working with steel.
- Smooth start that allows you to perform the cutting operation smoothly and without jerking.
- Weight of the tool. Heavy-duty unit often veers into a different angle during operation.
- RPM adjustable. With this function, the craftsman can select the sawing mode, taking into account the material characteristics of the workpiece.
- RPM under load. Stable cutting unit movement promotes a smooth sawing seam. This rules out the risk of splintering or deviation from the sawing line.
- Blowing direction. A blowing air stream blows air across the cutting area, cools the engine and sweeps away chips. This improves the view of the sawing point.
Important! To increase visual control over the direction of the cut, it is recommended to use a working area light.
To achieve the most accurate cut, the craftsman must keep the direction in one plane
How to cut a tabletop without jagged edges with a hacksaw
A regular hacksaw is good for cutting a tabletop. Make sure, however, that they leave at least 100 mm of headroom when working. The tool must have fine teeth. Better if it is a hacksaw for metal.
You can cut a tabletop with a metal saw.
Attention! The teeth must be hardened and set at ½ the material thickness.
You’ll need paper tape, a file for the rough cut, and sandpaper for the finish.
Take several measurements in order to cut evenly.
How to properly cut a tabletop with a hacksaw:
- With a sharp tool, outline the saw trimmer fishing line;
- paste adhesive paper tape along the lines to protect the upper decorative layer;
- Move the hacksaw to direct at an acute angle to the surface of the sheet (no more than 30 degrees);
- Cut smoothly with medium pressure.
Any irregularities can be covered with sandpaper. If chips appear, they must be treated with a file, moving from the edges to the center. Grind away any remaining small defects with fine sandpaper.
How to cut a countertop without chipping using a hacksaw
An ordinary hacksaw is suitable for cutting the worktop. But remember to leave at least 100 mm of reserve when sanding. The tool must have a coarse toothing. It is better, if it will be a hacksaw for metal.
The metal hacksaw can be used to cut off the countertop.
Attention! The teeth should be hardened and set at ½ the thickness of the material.
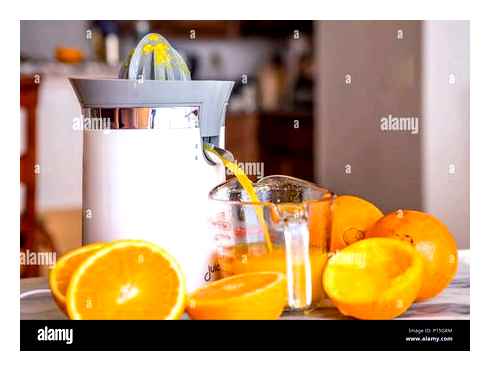
You will need paper tape, a file for the rough cut and sandpaper for finishing.
Take several measurements to cut evenly.
How to cut a tabletop properly with a hacksaw:
- Use a sharp tool to mark the saw trimmer line;
- glue a paper adhesive tape along the marking to protect the top decorative layer;
- guide the movements of the hacksaw at an acute angle to the surface of the sheet (not more than 30 degrees);
- Cut smoothly, with moderate pressure.
Any irregularities can be covered with sandpaper. If chips appear, they must be filed, moving from the edges to the center. sand away any remaining small defects with fine sandpaper.
Marking the kerf line
How to saw with a jigsaw to cut a piece evenly? This question interests many craftsmen engaged in carpentry work. Experts recommend in this situation to outline a fishing line for the trimmer of the cut and securely fix the material on the surface. Working with long blades, it is possible to use flat slats as guides. Clamps are great for securing.
Step by step process of marking the kerf line:
- Before you can evenly cut the workpiece with the jigsaw, it is necessary to make a marking on the material, using the ruler.
- The required distance will need to measure from both sides. The marks are connected, thus forming a fishing line for the trimmer of the cut. If there is a need to create a shaped line, you must first draw it on paper and only after that transfer it to the material to be sawed, using a copier.
- The marking is applied to the surface with a dark-colored marker.
- Sawing the workpiece begins with drilling holes in the central part.
- The saw blade must run from the center of the material to the marking line. Only after that can we saw the workpiece around the circumference of the circle.
Tip! While working, the jigsaw must not be pressed too hard, as you tend to increase the pressure on the material and cut quickly.
When selecting the length you need to consider the thickness of the material
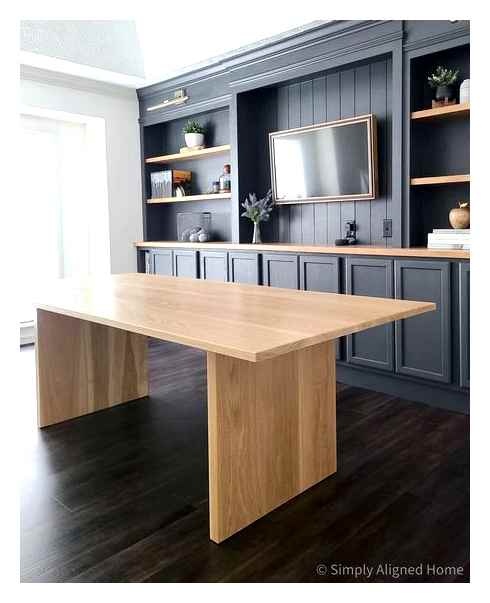
Rules to follow when sawing
With the tools we have already dismantled, now move on to auxiliary devices, which you will need.
The correct procedure for sawing Laminated chipboard looks like this
- First mark out the material. We take a pencil and draw the points of the future sawing on the face of the laminated chipboard. After drawing all the points we connect them into a line for the trimmer and glue the adhesive tape on top of it. Saw wood chipboard with a laminated coating is best to use adhesive tape, so that it reduces the number of cracks when splitting. They appear because laminated chipboard is subjected to high pressure when the temperature rises.
- Then we saw the board. To do this, set the selected tool at the right angle to ensure that the part has straight edges. The process itself should proceed smoothly and accurately, without sudden movements.
- Finishing the board. If irregularities remain on the edges of the board later on, they can be treated with a file. And the cut lines are machined with sandpaper.
Most often amateurs overestimate their strength and take it upon themselves to saw details of Laminated chipboard, and then regret that they did not turn to professionals at once. After all, a specialized company guarantees you finished parts for furniture without chips, made to your drawing to within a millimeter. In addition, finished parts need to glue the edge, which you can not do at home, because this requires a professional gluing line for the trimmer, with which experts and process workpieces.
What tools can be used
A hacksaw
This tool is used for the good old-fashioned scratch method. It must be said that a good quality cut with a hacksaw is difficult to achieve.
- First of all we scratch or cut the fishing line for the trimmer measure on the material with some stabbing tool (for example, a knife) and stick the tape on it. It is needed in order not to damage the laminate surface.
- We guide the hacksaw to the material at an angle of 30 degrees and move it smoothly back and forth. There will definitely be a chip left in this case.
- If damage from the hacksaw remains, go over it with a file (from the edge to the center).
- The final step is to treat the cuts Laminated chipboard with sandpaper, so that no roughness is left.
The main advantage of the hacksaw is its availability and ease of handling, but it does not perform the function we need to prevent splintering, so we do not recommend its use.
Electric jigsaw
Electric jigsaw. this is the most popular solution at home, since the tool itself does not cost a fabulous amount of money, and therefore available to the average consumer.
Saw blades for sawing worktops with a jigsaw should be of small length (not more than 75 cm) with teeth of class A or B, suitable especially for Laminated chipboard.
While cutting with the jigsaw, you need to make smooth, non-pressing movements with the tool at a slightly above-average speed. It is on the opposite side of the board from that into which the jigsaw teeth enter that the chips are most likely to appear.
Chips appear on the reverse side of the board in the process and spoil the appearance of the workpiece. They can only be removed with a router, which means extra work and material waste. Consequently, this tool is not suitable for us either.
Circular saw
Circular (or circular) saw. another tool that can be used for making furniture parts.
For sawing it is necessary to mark out guide lines on the boards and clamp the saw to the board, but it is not guaranteed that the edges of the parts will be straight. Chips appear on the reverse side of the board. And they can only be machined with plastic profiles with snaps on the ends Chipboard. But the circular saw. not the cheapest pleasure, and even with it you can not avoid chips, so in this case there is no sense to overpay.
Router
Another option for sawing laminated chipboard is an electric tool for manual woodworking. It is used in conjunction with a jigsaw. The process looks like this: first, you saw Laminated chipboard with a jigsaw, moving slightly away from the markings, and then with a cutter with a bearing, which deepens the cut to the desired level.
The main disadvantages of this tool is that it is not as common as, for example, an angle grinder, and will not find everyone in the house. Well, its use. it is quite a labor-intensive process, which can handle only qualified specialists, and the beginners should not even approach it.
Cutting and forming machine
The most correct cut and a guarantee of absence of chips can provide only one tool. format-cutting machine, which belongs to the professional equipment. Since the machine is very expensive and is used mainly in manufacturing, amateurs usually can not afford it. The only optimal solution in this case. turn to professionals. Companies that specialize in sawing furniture parts usually use these machines in their work.
Formatting and cutting machines have the following settings, which are set depending on the length and width of the plate to be sawn:
The machines themselves are divided into the following varieties:

The components of a format slicer, which allow for precision and no chipping in the production of parts:
- The bed is the stationary base of the machine, to which all the other mechanisms are attached. The heavier it is, the better for sawing, as it eliminates vibrations and oscillations that can interfere with the process;
- the scoring assembly, an element which pre-saws the workpiece blank and serves to ensure that there are no chips at the bottom;
- the main saw serves for the final sawing of the panel and is responsible for a clean cut without chips on top;
- Work tables. there are three of them. The first is stationary and serves as the base for the undercutting assembly, the second is movable, and on it the plate is fed to the disk, the third serves to support parts that are sawn off the plate;
- The carriage is the part of the machine that allows the format table to move;
- stops and rulers. components whose main function is to hold the plate in position.
The construction of formatting and cutting machines allows them to ensure a precision in cutting laminated chipboard for furniture parts that no other tool can guarantee. This is also the only way to avoid chips entirely.
How to cut with a circular saw
It can be used to make long cuts, but it generates more chips than an electric jigsaw. A saw blade with fine teeth is needed.
Work with power tools should be careful.
As a rule, the side where the teeth are plunged in remains clean, while the opposite side is chipped.
Start cutting from the front edge (facade) to avoid chipping on this part.
It is more convenient to work with the saw fixed on the table. This way the tool is not busy, and you can use the guide. It increases the accuracy of the cut and makes it possible to make several pieces.
Work properly with the tools.
Chips that are formed after the cut can be processed with a file and emery board.
How to saw with a circular saw
The tool can make long cuts, but it produces more splinters (compared to sawing with an electric jigsaw). We need a saw blade with fine teeth.
Work with electrical appliances should be carefully.
As a rule, the side where the teeth are cut remains clean, while the opposite side is chipped.
Start cutting from the front edge (facade) to avoid chips in this part.
It is more convenient to work with the saw fixed on the table. This way the tool is not busy, and you can use the guide. This will increase the accuracy of the cut, allowing you to make several parts.
Work with tools properly.
Chips that are formed after the cut can be filed or emery board.
Sawing with a router
Great way to get a clean cut. First, the material is sawn with the jigsaw with 2-3 mm indent from the marking line. Then the cutter aligns the trimmer line according to a pre-prepared template. A cutter with a bearing is suitable for the work.
When cutting simple chipboard, there can be no problems, but with laminated chipboard it is much more complicated.
Not only straight but also curved cuts and curved pieces can be made with this method.
Circular saw blade choose the one with the biggest number of teeth, to ensure a smooth cut.
The disadvantages of the method: it is necessary to make a precise marking, to file the workpiece in advance and set the template under the milling machine. That is, the tool is inconvenient to cut several identical parts.
Saws with a panel saw
suitable tool for cutting boards and pressed materials of different thicknesses. The cuts are precise and several pieces can be stamped.
Professional machines are used for industry.
Small in size and weight (up to 20 kg), easy to install. The machine can be dismounted and relocated as needed. The tool is suitable for tearing down to a depth of eight centimetres. Also in the home workshop, you can see the tabletop with a circular saw with an extended working table.
Household machines are usually used at home.
They are more convenient than household cutters because they allow you to cut not only along longitudinal but also transverse lines. The maximum cutting depth. Nine centimeters. During the work it is necessary to apply clear markings and observe the safety precautions.
Processing nuances Laminated chipboard
First of all, let’s consider all the materials and tools that will be needed for the work:
By the way, particleboard in the furniture industry and construction began to be used only in 1940 in the United States, but after a fairly short time, the popularity of this material has increased and spread throughout the world. Thanks to this industry has made a significant step forward, and there are all kinds of varieties of this material.
One of the most popular and frequently used types is Laminated chipboard, which is not simply the product of pressing sawdust with glue, subjected to high temperatures, but also acts as additional chemical and physical protection in the form of a melamine film.
Usually there are no complications when sawing Particleboard, but with Laminated Particleboard this seemingly simple process can become complicated. The fact is that the countertops often have a coating from the manufacturer of multi-layer plastic HPL. This significantly complicates the process of sawing. This coating can vary greatly in quality and in basic properties, and it is not always a polymer coating. Therefore, when processing this material, there are many different nuances.
- Using a well-sharpened blade, a groove of 2-3 mm depth is made. In the presence of polymer coatings of various kinds, it is recommended to warm up the blade slightly, and then immediately proceed to direct use. Because of the pressure of cold steel on hard plastic, even if the sharpening is very good, minor microcracks and chips can occur, which is best avoided if possible.
- With a tool called an electric jigsaw, it is necessary to carefully and smoothly make the cut. While working, it is important to carefully adjust the direction of the blade. If there are places where the direction changes, it is better to use an ordinary hand jigsaw as a secondary, auxiliary tool. Or you can use the thinnest file in an electric jigsaw. But this is not always convenient.
After the work is done, you can move on to the final stage of sawing Laminated chipboard.
To sum up
If you faced the question of sawing worktops, then you should not be afraid, because it is quite possible to do it yourself. If there is a possibility, then it is better, of course, to use the services of professionals and take the material for processing to the workshop, where all work will be carried out on special equipment and in a particularly high quality.
In the case of sawing worktops at home, so that there are no chips, use a suitable tool. a jigsaw, adhering to the maximum accuracy and precision when working with the workpiece.
How and what to cut a hole in the countertop properly for the sink?
Admin1 13.10.2018 Renovation Комментарии и мнения владельцев to the entry How and what is correct to cut a hole in the countertop under the sink? Disabled 6,518 Views From our article you will learn how to properly cut a hole for the sink in the countertop, what you need to consider and what is better to cut the countertop under the sink.
“Saving money is the best way to save money,” the careful owner reasoned. And not only ordering a budget kitchen, but also planning to cut a hole in the countertop for the sink on their own. True, this operation only at first glance seems simple. For a successful result, it is necessary:
- Know how to work with this or that material (for example, a quartz countertop will not cause difficulties);
- To have a set of necessary tools (or to know where it can be borrowed);
- Understand the nuances, so as not to spoil the product (expert advice is important here).
Only then is it possible to achieve maximum quality and enjoy a perfectly functioning kitchen for many years after the work has been completed.