How to make a circular saw from a circular saw with his hands
Before constructing a machine, it is important to decide on its purpose. To prepare firewood and perform simple sawing, it is enough to have a securely fixed table, in which there is a slot for the saws. But it is difficult to call such a machine safe or functional.
To do more work, it is worth to make a circular saw equipped with a coordinate table. It should have guides. This will help change the degree. You should also be able to change speeds and change the discs.
You can make a circular saw from a variety of fixtures. Almost every man has an angle grinder in the range of tools. It is often used in the home. To make a stationary unit you need to use a workbench or special table. The tool must be secured from below.
So, how to make a circular saw? To do this, you need to do the following:
- Stretch a metal band clamp on the tool. Its coupler should be placed at the bottom.
- Fold the strip of metal in half and fix it around the holes.
- Make holes in the gearbox of the angle grinder.
- Attach axle handle.
Please note! The handle can be made from a metal bar or tube. In doing so, the workpiece should resemble in the shape of a bracket.
The tool can be made from an angle grinder
Design features
Structurally, a home-made sawing table looks quite simple. The machine consists of a supporting frame for the motor, a transmission unit and a working table with a slot for the cutting disc. The design is equipped with stops for guiding the workpiece and a protective screen that prevents chips from entering and enhances work safety.
Mandatory requirements for the sawing table:
- Rigid, stable construction;
- Smooth surface of the table top;
- Secure fastening of the circular saw blade;
- Fences to protect the operator of the machine (table);
- easy access to the control device (start and stop buttons).
The equipment must be installed on a frame supported not on solid plates, but on legs. This increases convenience, although it makes the saw table less stable. To increase resistance the base frame can be made of metal or reinforced with metal parts. Safety is ensured not only by the protective shield, but also by fixing the disk to the bottom (inside) side. Additional requirements depend on the nature of the work. auxiliary elements help to process parts more accurately, to saw longer boards, as well as thicker logs.
Making a saw table with their own hands, you can get a number of advantages. from reducing costs to the possibility of changing the design as required by the master. If desired, it is possible to replace some parts with more cost-effective parts, use leftover materials from repair or construction. The only disadvantage of the circular saw, independently attached to the machine, is a decrease in the accuracy of positioning of workpieces. But this point still largely depends on the skill of the performer himself.
Rigid, stable design
Smooth surface of the table top
Safe drive mounting
Fences to protect the operator of the machine (table)
Shaft and bearing options, with and without filing
There are a huge number of options for making shafts for circular saws. They all vary in cost, reliability and practicality. The main options for making such a unit are:
- shaft with an open bearing couple. The simplest and most commonly used option. It is characterized by a relatively low cost, ease of maintenance and the possibility of easy and quick change of parts. The disadvantage of such a model is the need for constant cleaning and maintenance due to contamination of the bearings with sawdust;
Optionally, shafts can be made with a right-hand, left-hand or centered drive pulley.
Hand-held circular saw. turning into a stationary saw
It is not difficult to make a stationary saw from a hand-held circular saw, extending its capabilities. The first thing you need is a table. The Finnish plywood is a convenient material, which unlike conventional plywood is laminated. the workpieces slip easily over the surface during machining. It is thick enough to withstand a large weight, moisture-resistant, good machinability. You can use ordinary 20 mm plywood, but it needs to be painted, or better covered with steel plate or textolite.
It should be understood that the depth of cut will be reduced by the thickness of the cover. You will need a large diameter blade so that the functionality is not reduced compared to a portable tool. Make the size of the table top sufficient for the workpiece to fit the width of the workpiece. It should be added that on the wide table you can additionally strengthen the electric planer and jigsaw, which will make the machine versatile.
Using the drawings and explanations, it is not difficult to make additional accessories for the circular saw, which will expand its capabilities.
Mark a rectangle on a piece of plywood with the necessary dimensions, cut it out and trim the edges. With the sole of the hand-held circular to the surface and mark the mounting points with a pencil. Make a cut for the circular saw. You can somewhat deepen the place of attachment, using a mill, but not more than 10 mm, so as not to weaken the table top. This way of manufacturing will bring the depth of cut close to the specified in the data sheet of circular saw.
From boards we make a frame (tsargah), which we will set from below to strengthen the construction. Four planks are fastened together into a box, glued to the table top, and fastened with clamps. Screw self-tapping screws into boards through the table. We countersink the holes for them from above to hide the heads of the self-tapping screws. To the crossbars of the stationary saw we fasten the legs, preferably with bolts with washers and nuts. The table should be provided with additional rigidity, that’s why we make struts at the bottom of the legs.
We make a limiting strip, equal to the length of the working surface. In it we drill two slots perpendicular to disk, in which the bar will move and be fixed at a certain distance from the saw blade. It remains to make changes in the control system: we fix the control button in the enabled state with duct tape. On the tsarga install a socket connected to the mains. Insert a switch in the wire to the saw.
We make circular saw shaft
Slide the bearings onto the shock absorber rod. If the bearings are too tight, pound them using a pipe head.
Clamp the bearings together with the spindle in a vise. Insert the end of the rod without threads into the drill chuck.
Mark the places for the circlips (the shaft length in the example is 16 cm). Using a drill, cut slots for the retaining rings with an angle grinder.
We cut off the excess part of the rod and grind it accurately.
From a metal pipe, the inner diameter of which is slightly less than the outer diameter of the bearings, cut a 16 cm piece.
Grind the inner diameter around the edge of the tube for the bearings.
Insert the rod and bearings into the tube, fixing them on both sides with snap rings.
We cut two legs for the shaft from sheet metal 25×6 cm in size and weld them to the edges of the pipe body. Grind away the weld joints.
Make an adapter from a metal pipe of suitable diameter to compensate for the difference between the diameter of the shaft and the inner diameter of the pulley.
We weld it on the shaft and grind the edges.
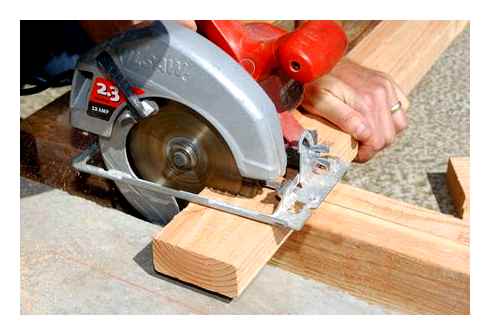
Drill four fixing holes in the shaft legs.
We paint the shaft with spray paint and put a masking tape over the shock absorber shaft.
Assemble the circular saw
Slide the pulley onto the hub and tighten the mounting screws.
On the second side of the shaft we mount the disk saw in the following order: nut. pressure washer. saw disk. centering washer. pressure washer. nut, and we tighten everything well.
Screw the legs of the shaft to the wooden bar with self-tapping screws.
We mount the electric motor so that its pulley and the saw pulley were in one plane and put on a belt. Our circular saw is ready. It only remains to turn on the power and make sure that everything is done correctly.
Which circular saw blades to buy?
The saw blade is the most important part of the circular saw, the working organ it is made for. To the same is tied and the entire design of the machine, so you need to decide in advance what disks will be used in the work, and how to choose the right one in absentia (online) on the designations on it or in the description.
Types and systems of saw blades designation
The two most common systems of notation are. On the first (n. A item. 1 in fig.) are sequentially marked by:
- blade diameter by tooth tips, mm;
- cutting width, mm;
- diameter of mounting hole, mm. The typical (default) tolerance of 0.05 mm is not shown;
- Non-standard fit tolerance (possible);
- Number of teeth;
- The letter T or pictogram shows presence of hardfacing on teeth;
- speed. operating (nominal) simply by digits, maximum permissible speed with prefix max.
For the second system it is obligatory to indicate the size of a circular saw blade: diameter at the tooth flanks, number of teeth, fitting diameter (the default tolerance is the same). e.g., 190-36-30 in item. B pos. 2 means the disk with 190 mm diameter (on tops of teeth would be 200) on 36 teeth for the fitment of 30 mm. The speed is indicated separately, but here it is maximum by default; the working one is 10% less. The other materials are either identified by a symbol (pos. 5) or by a notation (pos. 6). In pos. 2) or textually. The minimum rotational speed at which the quality of the cut is still ensured for certified discs with stabilizing slots (pos. 1, 2, 4, 5) is 50% lower than the working cut, and for solid discs 25% lower.
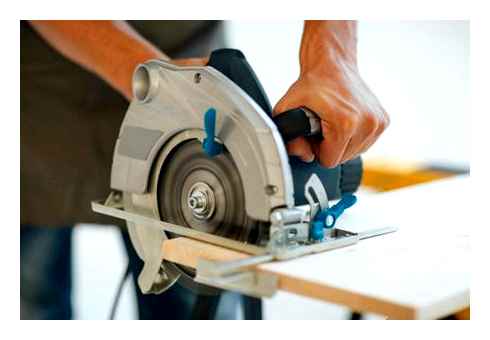
There are quite good quality “off-system” discs on the market (pos. 3-5). But in all cases just “as wood” (pos. 2-4) means qualified industrial wood, plywood, chipboard, laminate, etc. sufficient quality wood materials. It is dangerous to saw with such a disc when the wood is not matured, because it may jam and break off. For sawing wild wood special discs are produced with the designation Forest (wood, pos. 5), Wildwood, Timber, Log, etc.п. Discs with this designation are used in stationary pendulum saws, circular saws, etc. sawing equipment for sawing raw wood.
Note: if you are going to saw metal with your circular saw be careful. blades for steel and aluminum are not interchangeable. Universal saw blades for cutting any material are also sold, but they work roughly. Sawing with “all-purpose saws” laminate, laminated chipboard, etc. not laminated materials. the coating wears off.
Finally, there are a lot of saw blades on sale without any designations, pos. 6 in Fig. In general, they saw, but you have to be careful with them: linear rotation speed of such disc is better not to give more than 40 m/s. To get rotation speed from it (for gear calculation) we measure blade diameter at the teeth base D (in mm) and calculate its operating speed as 60(40 000/(3,1415xD)). For example., operating speed of a “cloudy” disk at 200 mm will turn out 3815 rpm; it is better to take 3500.
Manual with a guide rail
Deep and “long” sawing is not often necessary for the home handyman, and the manual circular saw is a useful thing in its own right. Besides, a manual circular saw with a guide rail can cut wood both crosswise and lengthwise, and at any angle. And a cutting length of up to 1.5-2 m is quite sufficient for almost all finishing work and creative work.
There are enough laths for manual circular saws on sale and they are inexpensive, but there is no universal one. The construction principle of a brand-name guide rail is illustrated in Fig.: The saw’s base plate (shoe) is made with a longitudinal groove, and the guide bar is stamped with the appropriate. ridge (arrow in fig.).
Use of handheld circular saw with guide rail
It is convenient to work: you only need to press the tool from above, and it will not go sideways or sideways. Also handy in competition: making your saws so that they do not sit on the guides of “partners”.
It’s not convenient for the masters. you can’t find a cheaper guide bar. And a circular saw with a groove under the guide costs disproportionately expensive compared to the same, but with a smooth shoe. Amateurs do the opposite: a guide rail with a groove of laminated plywood, and a pair of bosses attached to the shoe (pos. 2b in the big picture. in the beginning). But for this, firstly, you need a router table for wood, which must still make (not easy) or buy (for expensive). Secondly, the already small depth of cut is reduced by 16-20 mm. Thirdly, if the tool is still under warranty, from drilling holes in the shoe the warranty burns out. Fourthly, if the saw is a rental, nothing can be reworked in it.
There is another way, but the tool will need to be held in 3 planes at work: pressed, from leaving sideways and from spinning. The plywood base of the guide in this case can be thinner, 6-8 mm. The actual guide rail will be a flat rail (or a piece of steel angle, etc) fixed to it.п.), see. trail. Fig.:
How to make a guide for a hand circular saw
“Adjustment” of the device is reduced to the fact that the circular saw simply cuts off the excess from the base. Such a guide is attached to a board/sheet of material with screw clamps, just like a proprietary. When working on the workbench under the base put spacers slightly thicker than that of the material; the depth of cut from this corresponds to. is reduced.
Step-by-step assembly
Make your own hands a stationary circular saw can be made from an angle grinder and a hand torch without making any changes in the design of the working tool. The base is made of sawn timber, which greatly simplifies production, eliminating the need to use complex welding equipment. Step by step instruction:
- The base is made of a bar with the size of 40 x 40 millimeters and sheets of plywood.
- Table top is made of lacquered or laminated plywood. In the center of the table top a cut is made, into which the cutting disk will enter.
- The circular saw is secured from below with screws or other fasteners.
- a switch is installed, which allows switching on the saw without raising the table top. It is also possible to make a circular saw without a switch, for which the working saw is switched to “On” mode, and then the only thing left is to apply voltage to the tool.
- From furniture rails you can make a movable support, which is attached to the wall of the circular saw opposite to the switch with angles. The presence of such a stop makes it much easier to cut the wood.
- The longitudinal stop is made of metal angle, and its movement is done by loosening the bolts. Fixing bolts are located in small, parallel to each other kerfs of the table top.
- You only need to run the tool for a test run and make adjustments if necessary.
This variant of making a circular saw will be an excellent choice if you need a tool for sawing boards up to 3 centimeters thick. If you want to make a powerful and multifunctional device for the home, then use electric motors with a capacity of 5 kW or more, which allow you to process and saw boards with a thickness of 5-8 centimeters.
Making a homemade circular saw is not particularly difficult. You can use an angle grinder or hand saws, which are mounted inside the wooden base of the machine.
Some masters make a more complex tool, which implies the use of powerful electric motors, V-belt drive and saw blades of larger diameter. If there are any difficulties, you can find thematic videos on the network, telling how to make a circular saw with your own hands.
Flexible shaft for an engraver or drill
Hi all. A quick look at the flexible shaft, which can be purchased separately for an engraver or drill.
I have already written about how and for what I used a powerful engraver to 400W
And about the homemade stand for the engraver/drill.
It’s not very complicated to make a stand, in fact you can replace it with a piece of board / plywood and a pipe clamp from the hardware store. Diameters: 60 and 35 mm
You can use a special vise-clamp, the price is 10
One of the functions of this stand. to hold the drill while working with flexible shaft.
A few words about the flexible shaft for the engraver
Suitable for high-powered engravers and drills, designed for mounting in a cam chuck. About a meter long, made of quality metal, aluminum handles, shaft mounted on bearings. The handle has a small key chuck for clamping bits with a shank up to 6mm.
of the lot:Material handle: Aluminum alloy Diameter chuck: 6 mm Clamping size:0.5-6.5 mm Max Speed: about 10000 p/m Handle (Length): 15 cm Handle (Diameter): 26 mm Total Length: 110 cm
An image of the shaft shank that is clamped into the drill or engraver. Note the bearing.
Can be used like an engraver. with nozzles or drills.
So, the package came in about 12 days. ordered from stock at
The package was heavy despite its small size.
Inside the package is a small kit: a flexible chuck extension, as well as a wrench to tighten the chuck.
The appearance of the flexible shaft
I liked the workmanship: there are springs and a metal jacket for the shaft
There really is a bearing in the shank.
You can see the retaining ring and 608z bearing inside in the photo
The sleeve is a metal corrugated sleeve
How the handle looks like
Handle size approx. 15 cm
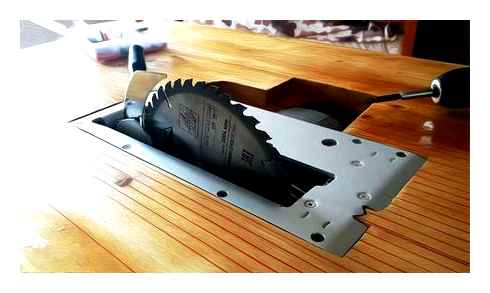
Cam chuck, up to 6.0mm
The handle is similarly fitted with a 608z bearing and a shaft with a slot for mounting a flexible extension.
There is an o-ring on the cap
When assembling, make sure the slot fits into the groove.
Then it snaps with a characteristic sound (on the photo without the cap for clarity)
Assembly and before inserting into the holder.
This shaft is suitable for use with a drill or electric screwdriver with speed control and a cam chuck. The disadvantage is that you will need to use your left hand (left heel, etc.) to.п.) to squeeze the trigger of the tool.
So I recommend to look in the direction of a pedal-type device. You can make a drill clamp like this or look for a vertical stand.
Well, in terms of working with flexible shaft all the nuances repeat the work with the engraver itself. We take a wrench.
Wrench by the way universal. suitable for 400-watt engraver
Clamping the tool and machining.
I use it most often for model postprocessing
Very handy to remove the “elephant’s foot”, seams after gluing, printing defects, etc.п.

As for choice. I took this lot, but as I understand it in stock a little bit left. There is still an alternative lot, with a similar price, differ stock From the accessories still recommend to pay attention to the vertical rack and a special vise-clamp for installing an engraver or a drill.
To be honest, it would be cheaper
Take a set of 400W engraver with a flexible shaft (this is type 5 in the lot). But as they say, the ship has sailed.