Device
Exploded diagram of the chuck
The purpose of the chuck is to hold firmly the working tool (drill) during work and provide a quick tool change when needed.
The first prototypes of modern devices appeared in the first half of the XX century.
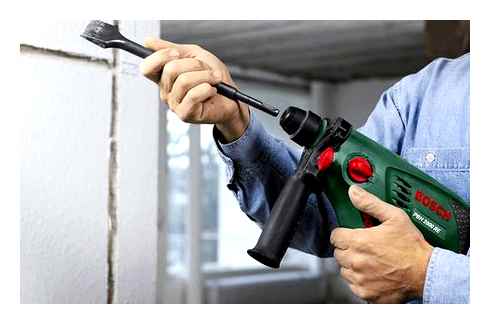
Engineers eventually came to the conclusion that the simpler the chuck design, the more reliable it is.
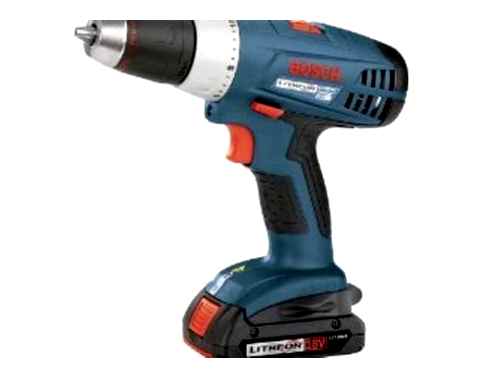
But over time, different modifications began to be developed, each with its own pros and cons.
An important feature of the chuck for the torch chuck is its extreme closed position. This prevents particles of concrete and other materials from entering.
The components of the most common clamping devices:
- The axle, on which is pressed the sleeve with many splines.
- O-ring with conical spring, mounted on the sleeve.
- Locking balls, which are located between the ring and the sleeve.
- A protective cover of plastic or rubber protects the cartridge from ingress of foreign particles.
This type was developed by technicians of the German company Bosh. It is called an SDS chuck and the letters are the first letters in the German “Insert, twist, snap” description of the act of changing the bits.
It is accepted to distinguish the cartridges by the features of attachment of nozzles (drills), some are installed on professional tools, working at high loads. There are less bulky types for use on household tools: drills, screwdrivers.
SDS chuck
All clamping devices of this type allow fast and 100% reliable fixation of the bit by inserting and turning it.
Subtypes, which are produced by modern manufacturers:
- SDS Plus. often found on low-power tools. Diameter. 10 mm, length. 40 mm, there are 2 slots for installation in the holder. Contact diameter from 4 to 26 mm.
- SDS Max. this marking is used on drill shanks with the diameter of the working part of over 26 mm. The length of the part to be tucked into the holder. 90 mm, its diameter. 18 mm.
- SDS Top. not so often encountered, shank length. 70 mm, diameter. 14 mm. On its surface there are 4 slots. 2 open and 2 closed.
- SDS Quick. have non-standard shanks with keys and holders. Needed for fixation under the drill or bit (from an electric screwdriver). Often produced by Bosh.
The main constructional element of the SDS drill is balls, which center the drill shank relatively to the hole, and then fix it.
Toothed-ring key
Standard type, often found on power drills.
They differ in that a special wrench is required to clamp the drill bit/bore shank which has a normal cylindrical shape without any slots.
Drills and drills are held in place by three claws.
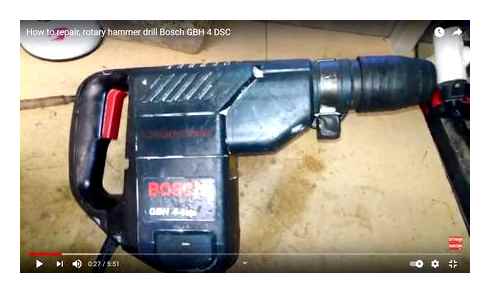
Not suitable for drilling large holes, because the drill bit will constantly twist in the chuck.
Quick-clamping
Can be seen on screwdrivers and some drill models. After the bit has been fitted, it is held in place with both hands: one hand holds the lower part of the chuck (ring) and the other hand tightens the upper ring.
Single sleeve clamping wrench
One of the types of quick-clamp chucks, but only one hand is needed to tighten the bit. But it can only be used on machines that support the automatic locking function of the operating shaft.
Transition
Designed to work with nozzles that cannot be fixed in the chuck of this peorator. That is, they are an independent clamping device (adapter), equipped with a shank.
How to remove, dismantle and change the cartridge
The cartridge is removed either for disassembly, repair and maintenance, or for replacement, if the restoration is not feasible.
Since the clamping devices are attached in approximately the same way, the principle of disassembly will also be similar.

The socket is usually removed for servicing, repair and lubrication. You will need a small set of screwdrivers and a vise for the work.
- It is necessary to remove the protective part of the casing from the side where the end of the lock is located.
- The ring that is behind the plate should be moved using a screwdriver.
- Remove the washer that is behind the ring.
- The second ring can then be removed using a screwdriver.
- The washer must be moved downward (toward the body) together with the spring.
- Use a screwdriver to pry out the metal ball.
- Carefully release the spring washer while pulling out the chuck.
- If the purpose of disassembly is to change the retainer, remove the lower part of the chuck together with the bush: unscrew the grub screw that holds it to the spindle. Now the easiest way is to clamp the sleeve in the jaws of the vise and unscrew it from the spindle (using a suitably sized wrench). Reassemble the new parts in reverse order.
If inspection, cleaning and application of lubricants is necessary, point 8 can be skipped. Reassemble step by step from point 8 to point 1.
Important: Use the grease recommended by the manufacturer for lubricating parts. Or have preventive maintenance done by a service center.
If the chuck is of the toothed-ring type, the sequence of disassembly will be different:
- Spread the jaws as far as possible.
- The chuck is placed on the working currency of the rotary tool (or drill) and secured by the center screw. It must be unscrewed.
- After that the chuck can be unscrewed. On some older models, the chuck device was attached to the cone shaft (not threaded), if you have such a sample of equipment, the chuck is simply knocked down by a hammer with not too strong, but sharp blows.
Reassemble in reverse order.
How are the cartridges for the drive unit constructed?
In order to use the different attachments for the rotary table effectively, you need to make sure they are securely clamped. This is what a special chuck is for. The first models began to be developed in the 1930s, when the first torches were put on the market by the world-famous Bosch company.
Such manual device as a peorator was immediately appreciated by consumers, because it can be used to combine drilling with pulse chiselling, which significantly increases the efficiency of the processing performed. The main drawback of the first twist drill bits was that the chuck was the weakest link in their design and soon became worthless under the action of shock loads.
As a result of long-term development, the manufacturers of torches and chucks have come to the following conclusion: the simpler the design of the clamping device, the more reliable it is in operation.
Externally the geared chuck is a completely closed chuck
The result is three basic types of geared torch cartridges, which are further subdivided into subtypes.
There are chucks in which the actuating cams actuate a special key that tightly clamps the shank of the tool being used. The most important advantage of this type of chucks is that they ensure reliable fixation of the tool used in combination with the geared torch. Meanwhile, to perform the replacement of a working tool in such a chuck for peorator, you will need to spend much more time than with other types of clamping devices.
Basic types of chucks for the rotary table saw
The working head of the rotary tool can also be fixed in the chuck by quick-action chuck (SDS), which is activated only by the force of the operator’s hands. Depending on the design, chucks of this type can be single- or double-joint, which also differ in their operating principles.
One-feed chucks are the easiest to use, but should only be used with drills with automatic shaft locking. One hand is sufficient to actuate this chuck. To use a double-clutch chuck, the user must hold the rear sleeve with one hand and rotate the front one with the other hand.
What is SDS
SDS is an abbreviation made up of the first letters of the words Steck, Dreh, Sitzt, which in German mean “insert, turn, fasten”. This is the simple yet ingenious principle behind the SDS chuck developed by Bosch engineers in the 1980s. Today 90% of all manufactured rotary tools are fitted with this simple-to-use and very secure clamping mechanism.
SDS chucks are often referred to as “quick clamping chucks”, but should not be confused with rotary clamping chucks. Unlike traditional quick-action chucks, the SDS does not need to be rotated to clamp the tool, but is simply held in place by hand.
In order to understand this type of chuck and how it works, all you need to do is look at the tool shank which is designed to be fixed in this device or the SDS adapter. This shank has 4 slots, two of which are open on the shank face and the other two are closed. The open slots also function as guides and ensure that the tool is positioned correctly when inserted in the chuck. Closed grooves ensure the locking of the shank in the combustion chuck.
There are special balls in the inner part of the SDS in the cartridge that simultaneously perform two functions. At the moment when the tool is just being inserted into the rotary tool holder, the balls on which the guiding slots move ensure that the tool is positioned correctly. Once the tool is inserted as far as it will go, these balls fixate the tool by rotating it slightly until the balls are fully seated in the closed slots of the shank. To make the use of SDS bits even easier, not only should the shank of the tool be thoroughly cleaned after each use, but also lubricated.
It should be borne in mind that due to the design features of SDS-patterns, the tool, which is fixed in them, is subject to a slight radial run-out at idle running, which does not affect the accuracy of machining at all. in the meantime, a little play between the shank and the inside of the chuck protects the latter from the impact that drills and drills have to endure while working on the rotary tool.
To protect against contamination, all peorator chucks are equipped with rubber dusters